Proposta de um Modelo para a Redução de Resíduos pela Eliminação de Perdas Internas em Empresas do Setor Metal-Mecânico
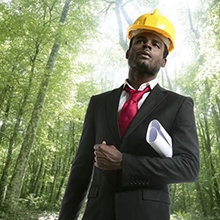
Por: Admin - 16 de Dezembro de 2014
Autores
Eliane Cortez (UNILASALLE) eliane@lasalle.tche.br
José Antonio Valle Antunes Júnior (UNISINOS) junico@produttare.com.br
Marcelo Klippel (UNISINOS) marcelo@klippel.com.br
Resumo
O presente artigo busca evidenciar a importância dos aspectos relacionados ao meio ambiente e os efeitos do desenvolvimento industrial neste meio, ao mesmo tempo em que apresenta uma proposta de um modelo específico para o tratamento de Perdas Ambientais Internas dos Sistemas Produtivos da Indústria Metal-Mecânica. Os autores definiram como ponto de partida da presente pesquisa o Modelo de Análise de Ciclo de Vida proposto por Sarkis e Rasheed (1995), a partir do qual é sugerido um incremento em termos de contribuição ao presente Modelo. Ou seja, o objetivo consiste em facilitar a identificação e posterior tratamento das Perdas Ambientais na Indústria Metal-Mecânica.
Palavras chave: Perdas, Gestão, Ambiental.
1. Introdução
O presente artigo parte do Modelo de Análise de Ciclo de Vida proposto por Sarkis e Rasheed (1995). Este modelo é genérico tratando da temática da gestão ambiental nas Fases de Obtenção, Produção e Distribuição. Na parte de Produção propriamente dita o Modelo propõe, de forma genérica, ações para a redução das Perdas tanto na etapa de Fabricação quanto na de Montagem.
Este trabalho, tendo como base a realidade específica do segmento metal-mecânico, propõe que sejam realizadas melhorias na parte de Produção no Modelo de Análise do Ciclo de Vida de Sarkis e Rasheed (1995). Para isso, utiliza a seguinte lógica geral: i) Descreve o Referencial Teórico proposto por Sarkis e Rasheed (1995); ii) Apresenta uma proposta de modelo para o tratamento das Perdas Ambientais nos Sistema Produtivos da Indústria Metal-Mecânica; iii) Mostra a inserção da contribuição proposta no âmbito do Modelo de Sarkis e Rasheed (1995); iv) Apresenta as conclusões do trabalho e faz algumas sugestões para o desenvolvimento de trabalhos futuros.
2. Referencial Teórico
Segundo Sarkis e Rasheed (1995), a proposta de avaliação do uso tradicional da Análise do Ciclo de Vida – ACV - enfoca o ciclo de vida dos produtos industrializados e a escolha de produtos alternativos especialmente de materiais que podem ser utilizados na fabricação. É possível aplicar essa abordagem para incluir análises de processos alternativos e tecnologias que podem ser usadas para fabricar o mesmo produto.
O ciclo de vida de um produto dentro de um processo produtivo, em forma de fluxo esquematizado, é apresentado na Figura 1. Na Figura 1 estão identificadas três fases primárias do ciclo sob uma perspectiva operacional composta por: obtenção, produção e distribuição. É possível observar no esquema que cada uma das grandes atividades gera resíduo. Qualquer resíduo que não possa ser eliminado pode ser reutilizado, reciclado, remanufaturado ou pode ser disposto. O principal objetivo é manter todos os materiais dentro do ciclo de vida e diminuir qualquer circulação no ambiente externo.
A Figura 1 demonstra que a única atividade que se opõe a esse objetivo é a de disposição. Até mesmo no "pós-mercado" os produtos e materiais podem seguir as mesmas estratégias para reintegrar o produto ao ciclo de vida. As setas do esquema mostram o destino comum que os produtos e materiais deveriam tomar preferencialmente.
Figura 1 - Ciclo de Vida / Processo Produtivo (Sarkis e Rasheed, 1995)
O modelo proposto Sarkis e Rasheed (1995) é interessante na medida em que prevê uma hierarquia para trabalhar as Perdas do sistema. É possível verificar que, reuso, remanufatura e reciclagem trabalham as perdas recolocando-as de alguma forma novamente no processo produtivo.
Autores como May e Flannery (1995), estabelecem uma hierarquia para a redução de desperdício que segue as seguintes prioridades gerais:
• Prevenção e redução do desperdício: são de extrema importância na prevenção e redução do desperdício os procedimentos internos de manutenção, monitoramento de válvulas com vazamento e ajustes. Também contribui para prevenção e redução o correto manejo e transferência de matéria-prima, eliminação de fluxos de desperdício. O controle rígido de inventário possibilita a identificação de passivo ambiental. A substituição de materiais ou produtos perigosos por menos perigosos ou com menor potencial tóxico. Utilização de tintas e solventes à base de água. A modificação dos processos, utilizando a reengenharia ambiental para mudar a forma de pensar sobre o impacto ambiental dos processos e produtos, pode prevenir e reduzir desperdícios.
• Reciclagem e reuso: a reciclagem e reuso são caracterizadas pela coleta e tratamento dos fluxos de desperdício tais como óleo e solventes usados. A utilização de processos de reciclagem, desenvolvimento de produtos para reuso ou reciclagem, contribuem para que a metodologia de reciclagem e reuso tenha sucesso.
• Tratamento do lixo: o desenvolvimento de metodologias para prevenir que os lixos perigosos entrem em contato com o meio ambiente. Tratar o lixo com processos biológicos, químicos ou físicos. Desenvolver serviços de tratamento de lixo oferecendo este serviço aos clientes e outras empresas.
• Disposição do lixo: para a disposição do lixo é preciso certificar-se que os locais usados para disposição são desenvolvidos para proteger o meio ambiente, em especial fontes de água subterrâneas.
Esta hierarquia, estabelecida por vários autores, é importante para que se faça uma análise das fontes dos problemas, determinando-se posteriormente ações de melhorias para os processos que são as fontes essenciais das perdas.
Os procedimentos adotados em relação aos resíduos em geral são não gerar, minimizar, reutilizar/reciclar para dispor apenas o material que não tiver nenhum outro tipo de solução a ser explorada.
No próximo item do presente trabalho, será feita uma proposta de adaptação e aprofundamento teórico e prático da estrutura proposta por Sarkis e Rasheed (1995) apresentada na Figura 1, para a realidade específica da Indústria Metal-Mecânica.
3. Proposta de um Modelo específico para o tratamento de Perdas Ambientais Internas dos Sistemas Produtivos da Indústria Metal-Mecânica
Os autores citados no item anterior têm como objetivo melhorar o entendimento dos aspectos ambientais ligados aos processos produtivos de uma forma ampla, auxiliando na identificação de prioridades e afastando-se do enfoque tradicional de proteção ambiental caracterizado pela lógica do tipo final-de-tubo.
Partindo da Figura 1, as Empresas podem visualizar de forma ampla os seus processos, quanto à geração de resíduos. No entanto, o modelo proposto não foca seus esforços na observação dos resíduos que estão sendo gerados em cada operação de um macro-processo. O levantamento do resíduo gerado é realizado somente no final de todas as operações do processo, caracterizando um controle tipo final-de-tubo. Esta sistemática de controle dos resíduos adotada pela Empresa não permite a identificação das perdas que ocorrem em cada processo, dificulta a sistematização dos processos no sentido da busca de redução ou eliminação dos resíduos. A Figura 2 exemplifica esquematicamente o processo interno:
Figura 2 - Processo Interno – Resíduos
Como foi comentado anteriormente as Empresas geralmente visualizam o processo de geração de resíduos de forma ampla, sem preocupar-se com os resíduos que estão sendo gerados em cada operação de um processo. Para a efetiva busca da qualidade ambiental e das ações visando à redução de resíduos gerados no interior do Sistema Produtivo este artigo propõe que o processo que seja entendido a partir da ótica do modelo específico explicitado na Figura 3, identificando os materiais que entram e saem de cada operação que constitui o macro-processo geral.
Figura 3 - Modelo específico proposto para o tratamento das perdas ambientais
O modelo específico apresentado na Figura 3 propõe que o processo produtivo recebe o aporte de insumos para a produção, de duas vias distintas. Da mesma forma, os resultados do processo são identificados em duas vias distintas, conforme é descrito a seguir:
a) Sistema Principal
a. O que entra no processo:
• Matéria prima: entende-se por matéria-prima aquela matéria de mais ou menos transformada entra diretamente na fabricação do produto e que permanece no produto até o final (Antunes, 1988). A matéria-prima entra no processo, percorre todo o fluxo produtivo sendo encontrada no produto acabado;
b. O que sai do processo:
• Material em processo: está dentro do especificado, para o item produzido, segue o fluxo normal de produção;
• Refugo: corresponde ao item perdas que não atendem às especificações de projeto. Por exemplo, os itens não atendem à especificação dimensional, a composição metalográfica não corresponde ao especificado. São falhas que não permitem a execução de retrabalho, caracterizando o item como refugo;
• Retrabalho: o item produzido não atende ao especificado, porém existe a possibilidade de retrabalhar o item de forma a que o mesmo atinja às especificações de projeto;
• Subproduto: considera-se subproduto todo resíduo proveniente da matéria-prima. O subproduto deve ser tratado com o mesmo cuidado aplicado no controle da matéria prima, pois desta forma aumenta-se a possibilidade de que possam ser insumos de novos processos produtivos. Os subprodutos são perdas consideradas no projeto.
As perdas geradas durante o sistema principal são contabilizadas, recebem um tratamento denominado, pelo modelo específico proposto de Tratamento 1 - T1 - que é a reutilização. A reutilização reduz, simultaneamente, a necessidade de matéria-prima virgem e o impacto causado pela disposição dos resíduos.
b) Sistema Secundário
a. O que entra no processo:
Entram no processo materiais indiretos. Os materiais indiretos são aqueles consumidos no posto operacional específico que estão vinculados apenas ao funcionamento deste posto (Antunes, 1988):
• Óleo lubrificante: utilizado para lubrificar as partes móveis dos equipamentos;
• Produtos químicos para limpeza e panos para limpeza: utilizados para a limpeza de peças e equipamentos;
• Agentes refrigerantes: utilizados para minimizar o excesso de calor gerado nas operações de usinagem e conformação, lubrificam a ferramenta e a peça e auxiliam na remoção do cavaco.
b. O que sai do processo:
• Agentes refrigerantes contaminados: material com características originais modificadas, que é impróprio para utilização no processo. Recebe Tratamento 3 – T3, que é a disposição e posterior encaminhamento para depósito de resíduos industriais;
• Panos para limpeza contaminados: material contaminado com produtos químicos diversos. Recebe Tratamento 3 – T3, que é a disposição e posterior encaminhamento para depósito de resíduos industriais;
• Óleo lubrificante vencido: material com características originais modificadas. Recebe o Tratamento 2 – T2, retorna ao processo como material indireto;
• Produto químico para limpeza contaminado: material com características originais modificadas. Recebe o Tratamento 2 – T2, retorna ao processo como material indireto;
• Agente refrigerante filtrado: material mantém a maioria das características originais. Recebe o Tratamento 4 – T4, reuso, retorna ao processo como material indireto;
• Agente refrigerante modificado: material com características originais modificadas, que se dispersa no meio ambiente. Este resíduo ou emissão não recebe tratamento, identificação Tratamento 0 – T0.
4. A contribuição do present trabalho ao modelo de Sarkis e Rasheed (1995)
A partir do modelo proposto sugere-se um incremento ao modelo de Sarkis e Rasheed (1995) conforme demonstrado na Figura 4 abaixo:
Figura 4 - Contribuição ao modelo de Sarkis e Rasheed (1995)
A proposta prevê a entrada, no processo, dos materiais indiretos e na saída considera o tratamento, que não são contemplados no modelo original. O modelo proposto estabelece o monitoramento individual dos processos, facilitando, desta forma a identificação das perdas internas nos Sistemas Produtivos.
5. Considerações Finais
A partir do Modelo de Análise de Ciclo de Vida proposto Sarkis e Rasheed (1995), os autores buscaram neste artigo apresentar uma proposta de construção de um Modelo específico para o tratamento de Perdas Ambientais Internas dos Sistemas Produtivos da Indústria Metal-Mecânica.
A proposta dos autores deste artigo foi concebida analisando-se o tratamento proposto por Sarkis e Rasheed (1995) de maneira a propor concretamente a necessidade de ampliá-lo e aprofundá-lo a partir de uma perspectiva operacional para a descoberta, tratamento e eliminação das Perdas Ambientais no interior dos Sistema Produtivos.
O modelo proposto neste artigo amplia a visualização tradicional dos Postos de Trabalho da Indústria Metal-Mecânica caracterizado por observar somente os fluxos associados as matérias-primas. Neste trabalho foi proposto, o que é central do prisma da gestão ambiental, uma visão de sistema do Posto de Trabalho que incluo o tratamento dos chamados materiais indiretos. Isto permite, no âmbito do chão-de-fábrica, estabelecer um monitoramento amplo dos processos produtivos, tendo como intuito básico identificar com facilidade as Perdas Ambientais observadas nas Indústrias do setor Metal-Mecânico.
Por fim, cabe ressaltar que a abordagem proposta através do Modelo específico para o tratamento de Perdas Ambientais Internas dos Sistemas Produtivos pode ser aplicada para outros segmentos industriais, para além do setor Metal-Mecânico. Os autores sugerem que o modelo proposto pode servir como um embasamento sólido para o desenvolvimento e implementação da Gestão das Perdas Ambientais internas em outros setores industriais. Isto porque suas bases conceituais são genéricas.
Ainda, o modelo conceitual delineado neste artigo pode ser utilizado visando sustentar um conjunto significativo de de estudos de casos empíricos buscando testar e validar o modelo téorico proposto.
6. Referências
ANTUNES, J. (1988) – Fundamentação do Método das Unidades de Esforços de Produção, Dissertação de Mestrado no Programa de Pós-Graduação em Engenharia de Produção da UFSC.
MAY, Douglas R, FLANNERY, Brenda L (1995). Cutting waste with employee involvement teams. Business Horizons, September-October.
SARKIS, Joseph, RASHEED, Abdul (1995). Greening the Manufacturing Function. Business Horizons, September-October.