Proposta de Metodologia para a Análise da relação de Capacidade e Demanda nas Empresas Industriais
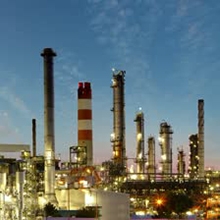
Por: Admin - 29 de Dezembro de 2014
Autores:
Altair Flamarion Klippel (KLIPPEL Consultores Associados) altair@klippel.com.br
José Antonio Valle Antunes Júnior (UNISINOS) junico@produttare.com.br
Marcelo Klippel (UNISINOS) marcelo@klippel.com.br
Paulo Regner Boeira (PRODUTTARE Consultores Associados) pboeira@produttare.com.br
Resumo
O presente artigo propõe uma abordagem metodológica visando avaliar a relação entre a Capacidade e a Demanda dos diferentes recursos que compõe um Sistema Produtivo. Parte das noções básicas propugnadas pelo Sistema Toyota de Produção. De um lado – o da Oferta – propõe-se que o cálculo de Capacidade seja feito levando em conta uma clara Definição de Fábrica em termos de Tempo e o Cálculo da Eficiência global dos recursos críticos baseadas nos conceitos do TPM. De outro lado – o da Demanda – o cálculo será realizado levando em conta as Quantidades requeridas pelo mercado e pelos tempos consumidos nos diversos recursos. Uma confrontação da Oferta/Capacidade e da Demanda possibilitará identificar os recursos restritivos – os chamados gargalos produtivos. A partir da identificação dos Recursos Críticos é possível, a partir de uma visão sistêmica do processo produtivo, orientar as ações de melhorias necessárias para o atendimento da demanda prevista, com custos compatíveis.
Palavras chave: Capacidade, Oferta, Demanda.
1. Introdução
A necessidade de resposta quase imediata as oscilações na demanda do mercado e as alterações na Programação tem levado diversas Organizações a repensar a maneira pela qual executam a sua Programação de Produção. Neste sentido, deve-se levar em consideração a alocação de recursos necessários (equipamentos, máquinas, pessoas), a capacidade de produção de cada recurso de forma individual, a sua eficiência global e, também, o tempo disponível para produzir, de forma a calcular a Capacidade real do sistema produtivo para atender a uma Demanda específica. O conhecimento desta Demanda é obtido considerando-se os tempos de ciclo (ou tempo padrão) de produção de cada produto a ser fabricado e as respectivas quantidades demandadas.
A Capacidade de produção de um Sistema é limitada pela capacidade de seu recurso restritivo – o gargalo – cuja Demanda será, em um ambiente no qual a demanda é superior à oferta, igual a Capacidade de produção deste recurso restritivo.
Este artigo tem por objetivo propor um método objetivo para o cálculo da Capacidade Grosseira de Produção e da Demanda dos Produtos dos diferentes recursos que constituem o Sistema Produtivo, tendo como base os princípios e conceitos propugnados pelo Sistema Toyota de Produção (STP).
2. Referencial Teórico
Uma das importantes contribuições do STP para o entendimento dos Sistema Produtivos foi, sem dúvida, o revolucionário conceito do que vem a ser o fenômeno da produção. O paradigma da análise deste fenômeno através da análise das operações que compõem um processo produtivo tornou-se ultrapassado. De acordo com este paradigma, o processo era visualizado enquanto um somatório de operações. Desta forma, quando alguma operação era melhorado tinha-se a ‘percepção conceitual’ que o processo como um todo também estava sendo melhorado.
A partir do surgimento do STP, o fenômeno da produção passou a ser percebido a partir de uma perspectiva diferenciada. Shingo (1966b, p.29) postula que a “produção constitui-se de uma rede de processos e operações, fenômenos que se posicionam ao longo de eixos que se interseccionam. Em melhorias de produção, deverá ser dada prioridade máxima para os fenômenos de processo”. Shingo propõe que todos os fenômenos que ocorrem nos sistemas produtivos possam ser visualizados a partir da Função Processo – de agora em diante intitulado de Processo – e da Função Operação – que na sequência será intitulado somente de Operação.
Shingo (1966b) afirma que o Processo pode ser entendido como sendo o fluxo de produtos de um trabalhador para outro, ou seja, os estágios pelos quais a matéria-prima se move até se tornar um produto acabado, pela sua transformação gradativa. Já as Operações referem-se aos distintos estágios pelo qual um trabalhador pode trabalhar em diferentes produtos. A Operação relaciona-se com um fluxo temporal e espacial, que é firmemente centrado no trabalhador. Ao observar o Processo ocorre uma observação do fenômeno produtivo do prisma do objeto de trabalho (materiais ou produtos).
Por outro lado, as Operações podem ser visualisadas como o trabalho – trabalho vivo (pessoas) e trabalho morto (equipamentos) para efetivar este Processo. Conforme citado anteriormente, as máquinas e equipamentos podem estar trabalhando ou sendo aplicados em diferentes produtos. É a observação da produção do ponto de vista do sujeito do trabalho (máquinas e trabalhadores), com o foco dirigido e mantido em um ponto da estrutura de produção ocupado por um operador, uma máquina ou um equipamento, ou ainda, como freqüentemente acontece, como uma combinação de ambos.
Da conceituação acima, constata-se que o Processo nada mais é do que o fluxo do produto. Já as operações representam os fluxos do trabalho. Conforme já mencionado anteriormente, estes dois fluxos não são fenômenos sobrepostos pertencentes a um mesmo eixo de análise. São, na verdade, fenômenos inter-relacionados que pertencem a eixos diferentes os quais visualizados de forma conjunta, enquanto uma Rede de Processos e Operações, se contituem no chamado Mecanismo da Função Produção. Por pertencerem a eixos diferentes, estes fenômenos devem ser analisados separadamente.
Para analisar a capacidade de produção de uma linha deve-se analisar a Oferta de cada máquina ou equipamento (recurso) que compõe esta linha. Esta Oferta está relacionada com a Função Operação, uma vez que a Oferta é diretamente dependende das pessoas e equipamentos envolvidos no sistema produtivo. Por outro lado, ao analisar-se as Demandas dos produtos, isto está diretamente relacionado com os produtos que estão sendo elaborados em determinado sistema produtivo. Desta forma, a Demanda dos produtos está ligada a chamada Função Processo. Observar a problemática da relação entre a Oferta/ Capacidade e Demanda a partir da ótica proposta pelo Mecanismo da Função Produção apresenta pelo mínimo duas vantagens básicas a serem desenvolvidas na prática industrial.
A primeira relaciona-se com a compreensão mais ampla do fenômeno produtivo da Oferta e da Demanda, ou seja, as vantagens didáticas associadas a percepção do fenômeno produtivo. A segunda, consiste em perceber que as ações de melhorias efetivas que podem ser realizadas nos Sistemas Produtivos devem ter dois focos distintos, porém relacionados: i) as ações de melhorias na Capacidade (Função Operação) e ii) as ações de melhorias na Demanda (Função Processo). Na sequência o presente artigo pretende detalhar os aspectos relativos a Oferta (Função Processo) e a Demanda (Função Operação) nos sistemas produtivos.
A Oferta dos recursos produtivos, que equivale a sua Capacidade produtiva, é dada pela fórmula abaixo, na qual a mesma é calculada em unidade de tempo.
Nesta equação observa-se que a multiplicação do tempo de ciclo de um produto pela quantidade produzida deste produto em um recurso corresponde, na realidade, ao tempo de agregação de valor deste recurso no processo de produção. Em outras palavras, representa o tempo em que efetivamente o mesmo funcionou adicionando valor ao produto em elaboração. Deve-se destacar que a demanda também é calculada na unidade de tempo.
Se a Capacidade de Produção de um recurso for superior a Demanda dos produtos no mesmo, então este recurso não é restritivo. Sendo assim, este tipo de recurso não limita a produção (trata-se de um recurso ‘lebre’ e não ‘tartaruga’ na linguagem proposta por Ohno (1997)). De outro lado, se a Capacidade deste recurso for inferior a Demanda dos produtos produzidos pelo mesmo ele passa a ser um recurso restritivo e limita a produção desta linha (trata-se de um recurso gargalo no sentido proposto por Goldratt).
Neste caso, este recurso estará produzindo em sua capacidade plena. Isto significa dizer que, caso não sejam realizadas melhorias em termos da Oferta e/ou Demanda, a sua Demanda será igual a sua Capacidade de produção. Ao se igualar as equações que representam a Capacidade (Operação) e a Demanda (Processo), obter-se-á a fórmula do cálculo do Índice de Eficiência Global do recurso restritivo. Este Índice está relacionado com a principal referência de medição da chamada Manutenção Produtiva Total (TPM).
Em um recurso restritivo (gargalo), considerando que todo o tempo existente deve ser utilizado para produção, pois como afirma Goldratt (1997) “uma hora perdida no gargalo é uma hora perdida em todo o sistema”. Neste caso este medidor será denominado de TEEP (Total Effective Equipment Productivity – Produtividade Efetiva Total do Equipamento). Qual o significado deste indicador do prisma do Sistema Toyota de Produção? Ele faz a medição do percentual de valor agregado no Posto de Trabalho em questão. Isto na medida em que o numerador representa o tempo de valor agregado aos produtos (somatório dos tempos X quantidades) e o denominador o tempo total de produção disponível neste mesmo recurso. Neste sentido, este é o mais importante medidor do Sistema Toyota de Produção do prisma da Função Operação – onde estão envolvidos as pessoas e/ou máquinas.
Já para calcular a eficiência global do equipamento em um recurso não gargalo é utilizado no denominador – ao invés do tempo total disponível no recurso – o tempo que o recurso foi efetivamente programado para produzir. Em um recurso não gargalo, por definição, este tempo programado será inferior ao tempo total. Isto na medida em que, em um recurso não gargalo, necessariamente haverá uma ociosidade do recurso. Nos recursos não restritivos o medidor do TPM é denominado de OEE (Overall Equipment Efficiency – Eficiência Global do Equipamento). Este medidor representa a eficácia do equipamento durante o tempo em que ele está efetivamente programado para produzir.
Para aumentar a capacidade de um sistema produtivo é fundamental realizar melhorias nas máquinas restritivas. Neste sentido, existem duas possibilidades: (a) aumentar a Oferta destes recursos críticos; ou (b) reduzir a Demanda dos produtos nos recursos restritivos.
O acréscimo da Oferta nas restrições pode ser feita de duas formas: i) aumento do tempo total disponível - T; ii) aumentar o TEEP - µglobal.
Na primeira situação, caso este recurso opere durante 24 horas por dia, as paradas programadas devem ser completamente eliminada. Se o recurso crítico opera em um tempo menor (por exemplo, 1 ou 2 turnos por dia), o tempo total disponível pode ser incrementado através da utilização de horas extras ou pela adição de mais turnos de produção. Ou seja, dentro dos limites das possibilidades, pode-se alterar a chamada ‘Definição da Fábrica’ (Antunes, 1998). Ainda, se podem adquirir novas máquinas ou, alternativamente, utilizar máquinas já existentes que possam realizar as operações necessárias.
Outra forma de aumentar a Capacidade de Produção do gargalo consiste em incrementar o valor do TEEP, através de ações que aumentem a eficiência do gargalo. A idéia básica consiste em identificar os potenciais de melhorias no recurso restritivo com o objetivo de aumentar a sua eficiência. Isto implica na identificação das principais causas que reduzem a eficiência do gargalo o que possibilita a elaboração de Plano de Ação visando a redução/eliminação das principais perdas mapeadas quando do cálculo do TEEP (Exemplo: Tempos Globais de setup, Manutenção Corretiva, Paradas para Refeição, Falta de Operador etc.).
Já a redução da Demanda nas restrições pode ser levada adiante a partir de duas maneiras genéricas, a saber: i) Redução dos Tempos de Processamento das peças que passam no gargalo - tpi; ii) Reduzir a quantidade das peças que passam no gargalo – qi.
A redução dos Tempos de Processamento de peças podem envolver ações tais como: i) redução dos tempos de ciclo/tempos de processamento das peças através da análise de da chamada Engenharia de Métodos; ii) reduzir os tempos de abastecimento e desabastecimento do recurso; iii) transferir parte das operações que são realizadas no gargalo (micro-operações) para outros recursos não gargalos; iv) mudança do projeto do produto visando a redução do tempo de processamento/tempo de ciclo.
Para reduzir as peças que passam no gargalo pode se adotar ações do tipo: i) utilização de roteiros alternativos de fabricação; ii) utilização de uma estratégica de terceirização de peças que passam na restrição; iii) não aceitar produzir determinadas peças demandadas pelos clientes (isto, obviamente, pode causar prejuízos para o desempenho econômico-financeiro da Empresa).
Desta forma, torna-se claro que genericamente quatro tipos de ações sistêmicas devem ser geridas com o objetivo de maximizar a utilização do gargalo nos sistemas produtivos. No caso do aumento da Oferta dos recursos críticos devem ser gerenciados de forma eficaz o tempo disponível para produção (T) e a eficiência do gargalo (µglobal). De parte da Demanda dos produtos que passam neste recurso devem ser administrados tanto o tempo de ciclo (tpi) de cada produto como a quantidade produzida (qi).
De um prisma de gestão, propõe-se que os Tempos disponíveis sejam feitos pelos profissionais responsáveis pela Gerencia de Produção e o PCP de forma a mais sincronizada possível. As melhorias da eficiência global podem ser buscadas pelos profissionais relacionados com a Manutenção Produtiva Total – TPM, os grupos de melhorias, a Gerencia e Supervisão de Produção.
Já a gestão da Demanda dos produtos no gargalo, no que tange a redução dos tempos de ciclo dos produtos pode ser realizada em conjunto pelas áreas de Engenharia de Produto e Processo e pela Gerência de Produção. A questão da redução das quantidades pode envolver a Direção Industrial, a área comercial, e o PCP/Logística.
3. Análise da relação de Capacidade e Demanda nas Empresas Industriais – Uma abordagem Metodológica
De acordo com a discussão teórica feita no item 2 deste artigo, a Capacidade grosseira de um recurso é obtida pela multiplicação de sua capacidade nominal (medida em tempo – T) pelo índice de eficiência global calculado para este recurso.
Através da construção da planilha apresentada a seguir, Figura 1, se obtém as capacidades reais dos recursos dos processos produtivos em unidade de tempo levando-se em consideração a eficiência global de cada recurso.
Já a Demanda dos Produtos nos recursos produtivos podem ser calculadas – como demonstrado no item 2 deste artigo – através da multiplicação dos tempos de ciclo multiplicados pelas quantidades obtidas a partir das informações provenientes das previsões da vendas e dos pedidos efetuados – geralmente chamados de ‘pedidos firmes’.
A utilização da planilha mostrado na Figura 1 possibilita identificar os recursos que não poderão atender as Demandas previstas.
Figura 1: Análise da Relação entre a Capacidade Grosseira e a Demanda de Produção
Na planilha acima, analisando-se o equipamento 1, verifica-se que os produtos A, B, C e D passam pelo mesmo, sendo os tempos de ciclo destes produtos, neste equipamento, respectivamente t1a, t1b, t1c e t1d e a programação mensal PMa, PMb, PMc e PMd unidades.
Para a programação mensal prevista no mês 1, a demanda do equipamento 1, em unidade de tempo para os produtos A, B, C e D será, respectivamente, t1a x PMa, t1b x PMb, t1c x PMc e t1d x PMd, totalizando uma demanda mensal D11 (demanda do equipamento 1 no mês 1) em unidades de tempo.
Considerando que o Índice de Rendimento Operacional Global - IROG calculado do equipamento 1 seja µg1 e a capacidade nominal deste equipamento, em unidade de tempo, seja C1, a capacidade real do mesmo será µg1 x C1 em unidades de tempo.
Caso a demanda mensal D11 seja maior do que a capacidade real µg1 x C1, o equipamento 1 será um recurso restritivo por não ter capacidade temporal de atender a demanda prevista. Caso contrário, o mesmo terá capacidade ociosa.
Nos demais equipamentos a mesma análise é feita, sendo que a previsão da demanda mensal total corresponde à soma das demandas mensais previstas para cada equipamento.
4. Exemplo Didático do cálculo da Capacidade Grosseira e da Demanda Agregada da Produção
A planilha apresentada a seguir, Figura 2, foi elaborada com a utilização da metodologia proposta no presente artigo para o cálculo da Capacidade Grosseira e da Demanda Agregada de produção.
Neste exemplo, o cálculo da capacidade nominal de cada recurso, em unidades de tempo, foi obtido considerando-se que os recursos 1, 2 e 3 operam em dois turnos de 8 horas, com intervalo de 1 hora para descanso, durante 20 dias no mês, totalizando 16.800 minutos. O recurso 4, por sua vez, opera apenas em 1 turno de 8 horas, com intervalo de 1 hora para descanso durante 20 dias por mês.
A análise dos dados da planilha mostra que a eficiência global de todos os recursos é baixa, visto que, segundo Nakajima (1988) as empresas de “Classe Mundial” apresentam uma eficiência global de 85%. Isto significa que, neste exemplo, de imediato se faz necessário a elaboração de um plano de ação visando melhorar o desempenho global destes recursos.
Por outro lado, independentemente destes baixos valores, dois recursos conseguem atender a Demanda, ressalvando-se que o recurso 4 opera em apenas 1 turno, mas mesmo assim consegue atender a previsão de Demanda. Caso este recurso possa fazer operações que são feitas nos recursos 1 e 3, que não atendem a Demanda, pode-se operar um segundo turno neste recurso durante tantos dias quantos forem necessários para atender a programação mensal.
Figura 2: Exemplo Numérico da Relação entre a Capacidade Grosseira e a Demanda de Produção
Desta maneira, tem-se uma clara noção da real capacidade da fábrica, de acordo com as respectivas capacidades de cada recurso produtivo, uma vez que tanto a demanda por equipamento como a capacidade de cada equipamento é estimada em função do tempo disponível e/ou necessário para realizar a produção.
5. Considerações Finais
Os autores do presente artigo procuram mostrar a importância do cálculo simultâneo da chamada Capacidade Grosseira e da Demanda Agregada de Produção. Uma análise crítica dos resultados obtidos permitirá a identificação dos recursos que irão restringir o desempenho global do sistema – os chamados recursos ‘gargalos’
A partir da identificação dos recursos restritivos e do cálculo da real capacidade dos mesmos é possível confrontar estas com a demanda necessária para o atendimento dos pedidos existentes e tomar as ações necessárias, que permitam alcançar os resultados desejados na Organização.
Ações sistêmicas como a realização de melhorias visando aumentar a eficiência dos recursos restritivos e, ainda, a construção do Plano Mestre de Produção para atender a uma demanda de curto prazo (uma semana, um mês) podem ser realizadas à partir desta metodologia. A partir dos conceitos explicitados no presente artigo torna-se claro a possibilidade de realizar ações sistêmicas tanto sobre as variáveis que afetam a Oferta/Capacidade – basicamente os Tempos Disponíveis (Modificações na ‘Definição da Fábrica’) e nas eficiências do gargalo – TEEP – quanto as que afetam a Demanda – basicamente os tempos de processamento/tempos de ciclo e as quantidades demandadas.
Finalmente, torna-se necessário explicitar que a metodologia proposta pode ter um amplo conjunto de outras utilizações tais como: i) Planejamento das melhorias necessárias no Sistema Produtivo com uma perspectiva de longo prazo; ii) Simulações das relações entre a Oferta e a Demanda a partir de modificações na eficiência global dos equipamentos; iii) Gerar ‘Definições de Fábrica’ que possam minimizar os custos globais envolvidos.
6. Referências Bibliográficas
GOLDRATT, Eliyahu M., COX, Jeff. (1997). A Meta. 12.ed. São Paulo: Educator.
NAKAJIMA, S. (1988). Introduction to TPM – Total Productive Maintenance, Cambridge, MA: Productivity Press.
OHNO, Taiichi. (1997). O Sistema Toyota de Produção – Além da Produção em Larga Escala. Porto Alegre: Bookman.
SHINGO, Shigeo. (1996ª). O Sistema Toyota de Produção – Do Ponto de Vista da Engenharia de Produção. Porto Alegre: Bookman.
SHINGO, Shigeo. (1996b). Sistemas de Produção com Estoque Zero: O Sistema Shingo para Melhorias Contínuas. Porto Alegre: Bookman.