Caso de Implantação do Total Productive Management (TPM) na Midea-Carrier
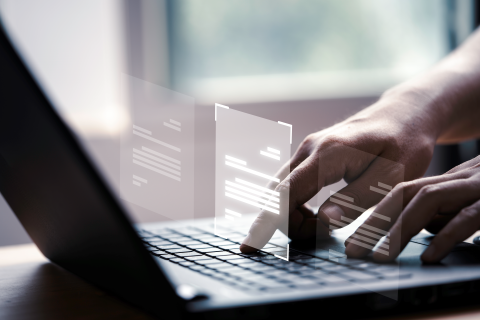
Por: Admin - 15 de Setembro de 2020
Confira a apresentação de Luciano Freitas, Sponsor do Projeto de Implantação da Total Productive Management (TPM) na planta da Midea em Manaus (AM).
Muitos associam o programa TPM à área de manutenção da empresa, visto que a sua tradução carrega a palavra Manutenção.
Contudo, esta palavra é utilizada no sentido de manter a produtividade total da empresa.
A Midea é uma empresa fabricante de eletrodomésticos e, neste vídeo, Luciano nos traz todo o processo de implantação da metodologia TPM e os principais resultados conquistado pela empresa.
Este vídeo foi extraído do evento online "Implantação do TPM: Rotinas, processo e padronização". Clique aqui para assistir o webinar na íntegra.
A empresa
A Midea é uma das líderes em fabricação de eletrodomésticos e equipamentos de climatização, produzindo cerca de 5 milhões de produtos ao ano.
Foi fundada pelo criador do primeiro sistema de ar-condicionado do mundo, Willis Carrier e, na América do Sul, possui unidades no Brasil, Argentina e Chile.
A sua planta de Manaus é o maior centro fabril em produção de ar-condicionado na América Latina, com mais de 1.200 funcionários.
A produção dos sistemas de climatização de ar, principal produto produzido pela Midea, é extremamente sazonal: em um semestre a fábrica trabalha com cerca de 35% da capacidade, enquanto no segundo semestre, com 90-95%.
Dessa forma, os equipamentos tornam-se críticos durante a high season.
Para iniciar a implantação da TPM, foi escolhido o setor de estamparia de serpentinas, visto que é um componente extremamente crítico do ar-condicionado, possuindo, neste setor, nove prensas e diversas outras máquinas, tornando-o uma restrição no sistema produtivo.
Porque a Midea optou por implementar a TPM?
Devido a sazonalidade do principal produto da planta de Manaus, a Midea buscava:
- Seguir os conceitos de manufatura enxuta;
- Garantir a performance dos equipamentos;
- Garantir atendimento aos clientes;
- Garantir o plano de produção na high season;
- Reduzir as despesas como horas extras e elevados custos de manutenção imprevistos para o atendimento do plano de produção.
Para isso, em 2018 começou-se a implantação do TPM com quatro pilares dos oito da metodologia: Manutenção Autônoma, Manutenção Planejada, Melhoria Focalizada, Educação & Treinamento.
Luciano ressaltou a importância do apoio de consultoria na implantação definitiva, visto que a Midea tentou outras vezes implantar o TPM por conta própria, sem obter os resultados necessários.
Processo de implementação na Midea
A Midea tinha um prazo de 12 meses para a implantação do TPM. A primeira etapa foi a escolha de consultoria TPM, tendo em vista que as tentativas de implantação com pessoal próprio não atingiram as metas propostas. A falta de conhecimento da real abrangência da metodologia TPM resultou em uma limitação para a concretização das metas.
Com o auxílio da consultoria, foram definidos os pilares que a empresa iria implantar: Manutenção Autônoma, Manutenção Planejada, Melhoria Focalizada e Educação & Treinamento.
Após a escolha dos pilares, foram definidos os equipamentos que seriam focados, prensas de aletas, e o comitê diretivo.
Para o engajamento total do time, foram realizados treinamentos com os operadores e áreas de apoio, para posterior realização do dia D (dia da grande limpeza e localização das pequenas falhas).
O dia D nos equipamentos foi realizado, com a participação de todas as áreas, que auxiliaram na colocação de cartões (etiquetas) para cada defeito localizado nas máquinas.
Para fixação e manutenção do programa, e das melhorias, são realizadas auditorias e reuniões diárias para análise do indicador de Eficiência Global (OEE).
Por fim, para análise dos resultados e acompanhamento do status do programa, o Comitê Diretivo se reúne mensalmente.
Pilar Manutenção Autônoma
Para inserir a cultura de que os operadores são os responsáveis pelos equipamentos, foi iniciada a implantação deste pilar com treinamento para todos os trabalhadores.
Após o treinamento, todos participaram do processo de colocação de etiquetas nos equipamentos, buscando identificar os defeitos a serem corrigidos.
Para análise e manutenção das melhorias, foi implantado quadro para gestão visual por máquina, onde todos podem acompanhar a evolução dos principais indicadores e ações tomadas, bem como os resultados das auditorias periódicas.
Foram desenvolvidas lições de um ponto (LUP) para padronização das atividades de troca de bobinas e matrizes, de operação, de manutenção, de segurança e de garantia da qualidade, entre outras, permitindo uma padronização nas tarefas realizadas em todos os turnos. Também foram desenvolvidas LUPs de melhorias e de resolução de problemas, a fim de manter o histórico de atividades desenvolvidas em cada máquina.
Pilar Manutenção Planejada
Este pilar é mais voltado à área de manutenção em si, possuindo nove subpilares.
Para iniciar a implantação deste, foi realizado um diagnóstico, no períod de um mês, em cada subpilar.
Após o diagnóstico, foram estruturados os indicadores da área de manutenção e os responsáveis para o controle e o acompanhamento da evolução de cada subpilar.
Com isso, foi possível implantar uma gestão de ativos e realizar a classificação ABC das máquinas da empresa. O aumento significativo da disponibilidade de manutenção das prensas se deu, fundamentalmente, pelo trabalho conjunto entre Manutenção e Produção na aplicação da Manutenção Planejada e da Manutenção Autônoma.
Pilar Educação e Treinamento
Para o sucesso deste pilar, é extremamente importante o alinhamento com a área de Recursos Humanos da empresa.
Busca-se identificar as deficiências (’’gaps") em Conhecimentos, Habilidades e Atitudes dos funcionários de todas as áreas. Temas como o conhecimento do método TPM, conhecimentos técnicos e operacionais e das ferramentas para ataque às perdas e desperdícios são elencados e também é elaborada a matriz de qualificação.
Através desta matriz são priorizados os treinamentos que mais impactarão positivamente na obtenção das metas previstas nas diretrizes estratégicas da Midea.
Pilar Melhoria Focalizada
Para implantação deste pilar foram realizados os seguintes passos:
- Definição das paradas históricas (Tipologias);
- Definição dos critérios de disponibilidade, desempenho e qualidade;
- Medição da eficiência [Índice de rendimento operacional global - IROG (OEE)];
- Análise das paradas;
- Estabelecimento de rotinas diárias, semanais e mensais para análise das perdas no IROG (OEE);
- Construção do plano de ação.
No vídeo, Luciano menciona que, a partir do momento em que a empresa percebeu que os ganhos financeiros estavam ligados a este pilar, foi dada uma maior importância e foram aceleradas as ações relacionadas às perdas e às baixas produtividades das máquinas.
Foi criado um fluxo de análise do IROG, com reuniões diárias e semanais, monitorando, assim, se a meta foi atingida.
A medição do IROG foi separada em dois momentos: o primeiro com a coleta de dados manuais, tais como horários e motivos de parada, para depois serem compilados manualmente e analisados.
Na sequência, foi implementado a coleta de dados automática, que permite, com maior acuracidade, saber, em tempo real, como estão as máquinas. Este tipo de coleta permite que o supervisor, o coordenador e o gerente analisem o painel de gestão dos equipamentos e direcionem os recursos.
A empresa realiza a análise das principais paradas do dia anterior, de cada equipamento, permitindo observar os impactos e auxiliando na tomada de ações para melhorar a sua performance.
A partir destas análises, é gerado o plano de ação, visando o melhor controle de perdas e desperdícios, medindo, assim, os ganhos.
Para cada ação, ou seja, proposta de melhoria, é preenchido um formulário padrão, onde coloca-se o investimento, o escopo da melhoria, a proposta, o responsável, as datas e como está sendo realizado.
Principais resultados da Midea
Antes da implantação da TPM, a Midea estava com eficiência geral da empresa em 49% (2018), em 2019 atingiu 62% e ganho de R$ 94.470,00.
No primeiro semestre de 2020 a empresa já conquistou 78% de eficiência e, se mantiver o percentual até o final do ano, terá ganho de R$ 503.839,00.
Além dos resultados na eficiência, o programa conseguiu introduzir a cultura do TPM em toda a fábrica, atingindo o engajamento de todos os operadores e da alta direção, motivando a equipe a manter uma melhoria contínua.
Também auxiliou no aumento da confiabilidade dos equipamentos e na melhoria da gestão dos ativos.
Já nas oficinas de manutenção, a equipe eliminou estoques intermediários, identificou ferramentas, disponibilizando-as com rápido acesso, além de separar kits para manutenção preventiva e organizar as ordens de serviço.