Engenharia de Produção Lucrativa (Moreku) com Junico Antunes
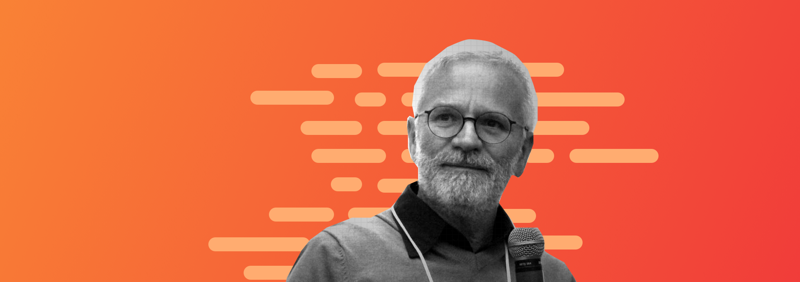
Por: Admin - 23 de Março de 2020
Neste episódio do Podcast Produttare, conversamos com o nosso CEO, Junico Antunes, um dos precursores no Brasil do Sistema Toyota de Produção e do Lean Manufacturing. A conversa abordou o Sistema Toyota de Produção e também o conceito de Engenharia de Produção Lucrativa, que foi assunto de um dos artigos publicados em nosso site.
Disponível também no Spotify:
Em vez de escutar o podcast, você pode ler o conteúdo transcrito abaixo:
Ivan: Olá, bem vindos a esta edição do Podcast Produttare. Eu sou Ivan De Pellegrin, sócio-diretor da empresa e hoje vamos conversar com o nosso CEO, Junico Antunes, um dos nossos sócios fundadores e um dos precursores no Brasil do sistema Toyota de Produção e do Lean Manufacturing. Bem-vindo, Junico. A nossa conversa hoje vai falar sobre sistema Toyota de produção e sobre o conceito de engenharia de produção lucrativa, esse assunto que foi alvo de um dos seus artigos publicados no site da Produttare e que é sempre bastante explorado por você nos seus cursos. Por favor Junico fique a vontade para suas considerações iniciais e nos conte como que iniciou o seu contato com o Sistema Toyota de Produção.
Junico: Bom dia, Ivan. É um prazer trabalhar contigo e fazer assim entrevista. nós temos uma experiência do sistema toyota de produção que originalmente veio das traduções dos livros originais de Shingeo Shingo e do Taiichi Ohno com uma editora que é muito importante para o Rio Grande do Sul e para o Brasil, chamada editora Bookman. Então nós tivemos a oportunidade de traduzir os principais livros dos nossos amigos Shingeo Shingo e Taiichi Ohno para o Brasil. Então esse é um contato importante do ponto de visto teórico. Do ponto de vista prático, nós viemos trabalhando desde a década de 80, 1980, trabalhando com vários casos práticos aí associados a implantação das dos princípios, métodos e técnicas do Sistema Toyota de Produção e evidentemente esses dois aspectos, aspectos teóricos e aspectos práticos, são fundamentais do prisma da implantação - e da implantação eficaz - das ferramentas, princípios e técnicas do Sistema Toyota de Produção em empresas industriais e de serviços.
Ivan: Muito bem, ótimo Junico. Obrigado pelas suas considerações iniciais. Vamos então mergulhar no tema de hoje. No seu artigo que mencionamos há pouco, você vai buscar o conceito de Engenharia de Produção Lucrativa ou Moreku, em japonês, em autores que participaram ativamente da construção do Sistema Toyota de Produção. Fala um pouco para nós sobre isso. O que é afinal de contas a Engenharia de Produção Lucrativa?
Junico: Inicialmente, como eu já falei, os autores seminais, ou seja, aqueles autores raízes, que implantaram o Sistema Toyota de Produção foram Taiichi Ohno e Shingeo Shingo. Sendo assim, é de compreender em profundidade os seus pensamentos e colocá-los em prática nas empresas é uma tarefa central de profissionais e pesquisadores que tratam do tema. E o tema central da Engenharia de Produção à la Toyota japonesa é a o tema da engenharia de Produção Lucrativa, que é muito pouca explorada na visão do Lean Manufacturing norte-americano.
Então no seu livro “O Sistema Toyota de Produção – Além da Produção em Larga Escala”, que nós tivemos oportunidade de traduzir pela editora Bookman, ele utilizou, o Taiiche Ohno, uma abordagem socrática. Ele fez a seguinte pergunta para seus leitores: “Qual a diferença entre a Engenharia de Produção tradicional do tipo taylorista/fordista e o Sistema Toyota de Produção?”. Como você sabe, o Taiiche Ohno, ele aborda os temas sempre a partir de uma questão socrática, ou seja, ao invés de dar respostas, primeiro formular perguntas para que os seus leitores possam pensar no problema. E ele mesmo, após algumas considerações, fornece uma resposta de que a Toyota adota a noção de Engenharia de Produção Lucrativa dado que “... a não ser que a Engenharia de Produção resulte em redução de custos e aumento de lucros, eu acho que ela não tem sentido nenhum”. Ou seja, Taiichi Ohno deixa claro a necessidade dos métodos, técnicas e princípios do método Toyota de Produção serem utilizados a partir da ótica econômica da empresa, visando melhorar dados econômicos da empresa, lucro líquido, retorno sobre investimento e caixa. Portanto, esse conceito da Engenharia de Produção Lucrativa é fundamental para os projetos de sistemas produtivos que sejam sustentáveis da ótica da competitividade.
Por algumas razões eu gostaria de dispor brevemente na sequência:
Em primeiro lugar, existe uma necessidade de compreender que o objetivo/meta no sentido utilizado mais modernamente por Goldratt do Sistema Toyota de Produção, em sua forma original, está totalmente voltada a alcançar resultados econômico-financeiros de médio e longo prazos, eficazes. Em segundo lugar, que a montagem técnico-gerencial dos sistemas de produção, ou seja, que a abordagem tanto técnica quanto de gestão, deve levar em conta, ter o foco nesse elemento econômico, que nós podemos chamar de “microeconomia real da firma”, ou seja, o que acontece realmente com os fatores de produção na fima. Isto implica em compreender, e isso é central, que não existem soluções de projeto de produção únicos e universais. Na verdade, eu preciso adaptar os princípios, métodos e técnicas não só do Sistema Toyota de Produção, mas da Teoria das Restrições, Seis Sigma às necessidades da empresa. E essas necessidades da empresa se traduzem em um ponto de vista prático nos custos relativos dos fatores e produção, nos custos das matérias-primas, do trabalho e do capital. Como a gente sabe, esses custos são substancialmente distintos em diferentes mercados, diferentes regiões, diferentes países. Ou seja, o custo da mão de obra no Brasil e na China e no Japão são distintos, o custo do capital e os custos associados também são distintos em diferentes países, e mesmo em diferentes regiões. Se você analisar os custos fatores de produção de mão de obra no Brasil, verá que existem diferenças significativas se as pessoas estão trabalhando no Ceará, ou se as pessoas estão trabalhando em São Paulo, no ABC Paulista, ou se as pessoas estão ligadas ao Rio Grande do Sul. Então existem diferenças que devem ser consideradas para que os resultados econômicos financeiros possam ser alcançados em diferentes contextos de organização dados os diferentes países e dados os diferentes realidades regionais e locais.
Ivan: Maravilha, ótimo Junico. Ou seja, de nada adianta uma solução técnica de ponta se ela não fizer sentido econômico-financeiro no contexto onde está sendo aplicada, não é isso? Você me fez lembrar agora uma passagem que você mesmo sempre comenta de definição de tecnologia do Bautista Vidal, que tecnologia é o uso dos recursos abundantes, evitando-se a utilização dos recursos escassos. Mas voltando para o artigo que você colocou lá no site da Produttare sobre a questão aí da Engenharia de Produção Lucrativa: no artigo você apresenta uma passagem que ilustra como a maturidade sobre o entendimento do Just in Time pode mudar a forma como uma pessoa vê o seu trabalho e a sua empresa. Nos fala um pouco sobre isso: como que essa linha de raciocínio pode ser útil para empresas brasileiras nessa época de globalização, de indústria 4.0?
Junico: Em primeiro lugar, essa recordação do Dr. Bautista Vidal é muito cara. O Dr. Bautista Vidal foi o homem que coordenou o programa nacional do álcool, que fez com que o Brasil saísse na dianteira internacional da produção de etanol, quando isso se fez necessário no país para a substituição de gasolina. Então a pessoa muito importante. O que o Dr. Bautista ensina é que a tecnologia é exatamente o quê? A maximização da utilização dos recursos abundantes, porque eles são baratos, e a minimização dos seus recursos escassos, porque eles são caros. Então, um país que é autônomo tecnologicamente ele deve utilizar abundantemente os seus recursos que são evidentemente abundantes - no caso do Brasil, a água, ar, terra - e jogar tecnologia em cima disso para obter os resultados. Mas voltando a sua questão, Ivan, na verdade é necessário que as organizações do ponto de vista mais profundo do Sistema Toyota de Produção - do que eu poderia chamar do Sistema Toyota de Produção raíz - implica em desenvolver uma cultura de custos e ganhos em todos os funcionários da organização. Tem uma abordagem do Michikazu Tanaka, que foi gestor da planta da Toyota de Daihatsu, que ele explicita isso ao responder uma pergunta que lhe foi formulado. Um jornalista perguntou o que que ele achava essencial Just In TIme. Essa pergunta é uma pergunta importante, quer dizer, o que você acha essencial do Just In Time? O gerente da planta respondeu o seguinte:
A resposta do iniciante é que o Just in Time é bom bom simplesmente porque reduz os inventários. Isso é verdade, mas é uma visão iniciante, porque o inventário na verdade é a febre. Quando a pessoa tá com febre evidentemente ela tem que procurar saber qual razão está com febre.
Uma resposta de nível intermediário é que o Just in Time permite a descoberta de problemas e promove a sua solução através do Kaizen. Ou seja, na verdade, para que você consiga resolver os estoques e para que você consiga melhoria, é preciso eliminação das perdas do sistema de produção. E isso implica em atuar na organização visando a eliminação dessas perdas.
Porém, a terceira resposta que é mais madura e que realmente é essencial, é que o Just in Time deve infundir, ou seja, deve colocar nas pessoas, uma consciência de custos em todos os empregados organização, do nível mais baixo da hierarquia ao presidente da empresa. Ou seja eu devo enxergar os problemas econômico, pequenas perdas, médias perdas e grandes perdas, todas elas são fundamentais para alcançar o resultado. Então nós necessitamos desenvolver uma cultura voltada aos resultados, mas não apenas na alta direção da empresa senão todas as os níveis hierárquicos da organização. Isso é realmente importante. O ponto aqui ressaltar que o Taiichi Ohno e o Sistema Toyota de Produção, em sua versão seminal de concepção, implantação, ou seja, como eu disse, o conceito raiz, ele necessita ser lido e relido, novamente lido e relido, na verdade a partir de uma ótica da produção lucrativa, onde nós devemos, sim, entender os custos globais da organização, dos diferentes setores, das diferentes diretorias,etc etc.
Eu vou tomar aqui duas questões para exemplificar o argumento. Vamos trabalhar um pouquinho com a visão prática - e eu vou botar aqui a ideia socrática que é muito caro ao Taiichi Ohno, é muito caro ao nosso amigo Goldrat. A pergunta é:
Teria sentido uma aplicação do sistema Toyota de produção nas empresas brasileiras hoje, nos dias atuais, a partir da seção central da chamada força minimizada de trabalho, ou seja, cujo foco é a minimização do trabalho, ou seja, tendo foco principal a minimização das pessoas para implantação do Sistema Toyota de Produção?
Essa é uma pergunta. Poderia fazer a segunda pergunta uma segunda reflexão: Por que no livro “O Sistema Toyota de Produção - Além da produção em Larga Escala”, que foi trazido para o Brasil 1997, não existem referências a utilização do OEE (Overall Effectiveness Equipment), que nós chamamos aqui na Produttare de Índice de Rendimento Operacional Global do Equipamento, como medidor central de uma abordagem, que também nos é cara que é abordagem do TPM, ou seja, da Manutenção Produtiva Total. Por que não há menção no livro do “Sistema Toyota de Produção - Além da Produção em Larga Escala” a esse importante conceito do OEE?
São questões socráticas que poderiam fazer os nossos ouvintes pensar em porque realmente aparentemente aí algum nível de contradição. Porém, se é possível compreender e responder na profundidade as questões que foram expostas, nós precisamos olhar os aspectos objetivos da “microeconomia da fábrica”. Aí temos que voltar ao contexto, temos que voltar a história. Nesse caso, especificamente, no contexto dos custos relativos dos fatores de produção, do trabalho e do capital, que eu mencionei anteriormente. No período e contexto específico da implantação do Sistema Produção do Japão o que acontecia, e o Shigo diz isso no seu livro “Sistema Toyota de Produção – Do Ponto-De-Vista da Engenharia de Produção” que o custo-hora das pessoas eram aproximadamente 5 vezes maior que a depreciação horária dos equipamentos. Evidentemente, que esses números podem variar de empresa a empresa. Mas o fato é que o custo-hora das pessoas é muito superior ao custo-hora da depreciação das máquinas. Diante desse cenário econômico, cujo fator restritivo mais importante a ser considerado para o projeto do sistema de produção está muito associado ao trabalho, ao custo das pessoas, e não necessário o uso das máquinas, é necessário refletir sobre o que fazer. Além disso, por relações históricas, a Toyota não poderia naquele período histórico fazer demissões, ou seja, precisava trabalhar com a ideia da mão-de-obra das dos profissionais como recursos fixos.
Qual é a lógica que o projeto da época realmente considerou? Como você tinha os investimentos adicionais em máquinas muito mais barato que os das pessoas, o que eu devo fazer? Eu devo maximizar, otimizar, melhorar ao máximo o que as pessoas, o grupo de pessoas, as equipes estão fazendo na organização. Ou seja, buscar uma Força Minimizada do Trabalho utilizando da melhor maneira o recurso restritivo, e o recurso restritivo época exatamente os trabalhadores que estavam lá frequentando as atividades produtivas.
Agora a pergunta que não quer calar: isso faria sentido no Brasil de hoje, nas empresas, por exemplo, no setor metal-mecânico? Essa pergunta remete para os custos fatores de produção.
Se comparado com o Japão o país como Estados Unidos e Alemanha, os custos relativos das máquinas são muito mais altos no Brasil. Ou seja, nós temos os custos das máquinas talvez mais ou menos igual, ou pelo menos muito parecido, com o custo-horário das pessoas. Nesse sentido, para nós, para a nossa realidade, nossas máquinas, nossos ativos que estão em máquinas são realmente fatores restritivos. Adicionado a isso, o fato da dificuldade de financiamento, das taxas de juros, que historicamente estão os postulados no Brasil. Aí eu sempre digo, se o Ohno resuscitate e viesse ao Brasil agora… Ora, se o Ohno estivesse vivo certamente ele não iria abandonar a noção da Força Minimizada de Trabalho (uma vez que a racionalização da utilização da força de trabalho é relevante em todos os casos), mas certamente daria atenção especial para o tema da maximização da utilização. E, para isso, atuaria para implantar, controlar e melhorar o OEE, ou melhorar o Índice de Eficiência Global dos Equipamentos, o Índice de Rendimento Operacional Global dos Equipamentos, uma vez que essas máquinas são muito caras e eu preciso utilizar esses ativos no máximo possível. Isso é fundamental. Historicamente, nós desenvolvemos vários trabalhos em empresas brasileiras do ramo metal-mecânico, que são nossos parceiros desde muitos anos, com o objetivo de aumentar esse Índice de Rendimento Operacional Global dos Equipamentos. Inclusive tratando de métodos para aumentar esse rendimento operacional dos equipamentos através de um livro, que eu produzi, que é o livro “Gestão do Posto de Trabalho”. Nós produzimos, eu, Marcelo Klippel e outras pessoas da Produttare. O objetivo desse método é aumentar o rendimento das máquinas. Inclusive isso é tão importante que é um dos temas centrais que nós temos em uma outra empresa do grupo, chamada eFact, que tem por base a metodologia do GPT e do OEE, só que através dos sistemas MES, ou seja, colocando a questão eletrônica da digitalização nesse processo. Então isso daí realmente são temas fundamentais. Ou seja, o STP necessita ser percebido de maneira mais dinâmica, dado que as ações necessárias devem partir da ótica da Engenharia de Produção Lucrativa. Ou seja, na verdade, produzir técnicas do Sistema Toyota de Produção, Teoria das Restrições e Seis Sigma, eles possuem, na verdade um “alvo móvel”,tendo em conta existe a dinâmica de alteração dos custos relativos dos fatores de produção ao longo do tempo e do espaço. Ou seja, historicamente nesses custos relativos dos fatores de produção, os custos associados com mão de obra, pessoas, cresceu significativamente, portanto esses números variam no tempo. E também variam no espaço porque em diferentes regiões, em diferentes países evidentemente você tem diferentes custos de produção. Aqui existe um ponto que eu gostaria de ressaltar, Ivan, e não quero me alongar mais. Não é admissível pensar na velha ideia taylorista, que foi uma ideia importante para gerar o sistema americano de produção, “the one and the best way”, a única e a melhor maneira de fazer alguma coisa. Ou seja, que existem soluções prontas, já testadas e universais. Não é verdade, porque os enfoques de melhoria necessitam levar em consideração os aspectos ligados aos custos relativos de produção, ou mais amplamente, à Engenharia de Produção Lucrativa. Esse de fato é um dos elementos centrais, senão o mais importante do Sistema Toyota de Produção.
Ivan: Ok, muito obrigado pela aula Professor Antunes. Estava pensando eu aqui que dificuldade que devem viver algumas empresas brasileiras que estão posicionadas globalmente ou que fazem parte de grandes corporações internacionais que normalmente utilizam os mesmos indicadores os mesmos KPIs para mensurar os resultados, a performance operacional das suas várias unidades espalhadas pelo mundo, não é? Porque, como você tava comentando, deve fazer muito mais sentido para uma empresa que está no Brasil, talvez na América Latina em geral, a atenção para o OEE, eficiência do capital das máquinas, do que para empresas para unidades que estejam nos Estados Unidos ou na Europa no Japão, enquanto para eles lá pode fazer mais sentido do que aqui as preocupações com a minimização da força de trabalho. Foi o que eu entendi agora da sua explicação, é isso? Mas voltando para a questão das passagens que você explora muito bem no artigo, tem uma outra passagem que vai também ao encontro de alguns comentários seus, que diz respeito a uma declaração do Taiichi Ohno quando ele afirma que aprendeu a fazer setup rápidos numa fábrica de forjaria da Toyota no Brasil. Olha só que interessante isso, né? Taiichi Ohno, com a sua humildade, dizendo que aprendeu a fazer troca rápida de ferramentas aqui no Brasil, numa unidade Nacional aqui nossa da Toyota. Isso vai de certa forma na direção do que você colocava antes que às vezes a gente tem ainda alguma dificuldade de convencer um empresário brasileiro de que construir uma solução própria customizada pode fazer muito mais sentido do que trazer, importar uma solução que já deu certo lá fora, correto?
Junico: Vamos lá. Em primeiro lugar, a tecnologia de troca rápida de ferramentas, na verdade, ela foi criada pelo Shigeo Shingo, no chamado SMED - Single Minute Exchange of Die and Tools. Foi originalmente criada pelo Shigeo Shingo. Porém, o Taiichi Ohno, que trabalhou em conjunto com Shigeo Shingo, vice presidente da Toyota Motor Company, ele realmente se apropriou dessa tecnologia de troca de ferramenta e, evidentemente, utilizou ela em várias partes do mundo. Então no riquíssimo livro que nós traduzimos pela editora Bookman - riquíssimo livro realmente - intitulado “Gestão dos Postos de Trabalho” (aliás, esse nome que me inspirou a escrever essa Metodologia da Gestão do Posto de Trabalho. Não é a mesma coisa, totalmente diferente, mas eu gostei muito do título do trabalho esse título). Esse livro foi comemorativo aos 100 anos do nascimento de Taiichi Ohno. Existe uma verdadeira preciosidade histórica para nós brasileiros que somos homens criativos, precisamos ter autoestima elevada e humildade para transformarmos e darmos competitividade cada vez mais para as nossas empresas, que escrita por ele no seu capítulo 20, cujo título chama-se “Aprendemos a fazer setup na forjaria da Toyota do Brasil”. Então na verdade ele está se referindo aqui a problema na troca de ferramentas na forjaria. Evidentemente, naquela época a Toyota era uma empresa bastante verticalizada, aí tinha setor de forjaria setor de usinagem, coisa que hoje as fábricas são muito mais horizontalizadas e têm de linhas montagem. Nesse momento, ele trabalha com precisão, conceito de engenharia de Produção Lucrativa. Na época da observação, feita pelo Ohno, a Toyota do Brasil, fabricava um volume muito baixo de 40 carros por mês. Nesse contexto da forjaria eles tinham apenas uma máquina que necessitava fazer mais 60 peças diferentes por mês de setup. Ou seja, como o volume de produção era grande, e os lotes pequenos, com uma variedade grande, ele precisava fazer 60 peças diferentes por mês, o que exigia um alto número de setups. Isso é uma realidade brasileira, nós trabalhamos com baixo volume de produção, mas elevada variedade de produtos, o que exige fazer muitas trocas de ferramenta ao longo do tempo. Naquele momento histórico, segundo Ohno, essa deve ter sido a menor empresa automobilistica do mundo. E devido ao pequeno volume de compras envolvido, nenhum fornecedor se interessava em fornecer forjados para a Toyota, muito trabalho. Ele fez um excelente trabalho e árduo – desenvolvido em conjunto por profissionais brasileiros e japoneses – e esse trabalho resultou na redução radical dos tempos de preparação. Ele fez um trabalho, junto com os caras, utilizando um método geral - que realmente é um método geral de troca de ferramentas feito pelo Shingo - no Brasil, com profissionais brasileiros e que reduziu radicalmente os tempos de preparação. A empresa tornou-se capaz de fabricar, segundo as próprias palavras do Ohno, “mais de sessenta variedades de peças sem provocar a perda de uma única peça”. Segundo Ohno, a fábrica brasileira tornou-se tão eficaz que como resultado, segundo as próprias palavras do Ohno, “os papéis se inverteram e mandamos duas ou três pessoas do Japão para aprender sobre setup de forjamento”. Que coisa bonita, não é verdade? Os japoneses desenvolveram na Toyota um meio de troca de ferramentas, do Shingo, que realmente é robusto e permite fazer vários trabalhos, mas é um método geral, que se aplica de maneira diferente em contexto diferentes. Aí o Ohno usou isso no contexto da forjaria com profissionais brasileiros, chegou a um resultado tão bom que o Ohno decidiu levar de volta práticas para as fábricas da Toyota no Japão. Ou seja, o Ohno tem umas palavras que eu gostaria de colocar aos nossos ouvintes: “... à Toyota do Brasil estava efetivando o Sistema Toyota melhor do que qualquer outra unidade” e, segundo Ohno, apesar do baixo volume (em contraposição a produção em massa), a empresa Toyota do Brasil estava tendo excelente desempenho econômico-financeiro. Ou seja, o ponto central: a ligação da técnica com a melhora significativa do desempenho econômico financeiro. E segundo as palavras do Ohno - palavras lindas - “os papéis se inverteram e mandamos duas ou três pessoas do Japão para aprender sobre setup de forjamento”. Vejam que os trabalhadores brasileiros, nós temos que acreditar cada vez mais nos trabalhadores, fizeram um trabalho de altíssimo nível que virou benchmark na época a Toyota a nível mundial.
Do prisma amplo, o Ohno diz que a Toyota do Brasil estava de fato efetivando o Sistema de Produção melhor do que qualquer unidade. É isso realmente é importante. Apesar do baixo volume em contraposição a produção em massa, o trabalho realmente era excelente. Então as melhorias melhorias efetivadas no sistema produtivo da Toyota do Brasil – que ajudaram a flexibilização da produção e o atendimento de uma demanda, essa demanda caracterizada por uma acoplação de alta variedade com baixo volume –, seguiram com rigor a máxima do Ohno, que essa máxima é fundamental de entender junto com a Engenharia de Produção Lucrativa. ‘Necessidade é a mãe da invenção’, ele não inventou essa frase, mas ele utiliza essa frase ao longo do seu processo.
Portanto, nós não podemos copiar exatamente igual as soluções, nós temos que entender os métodos de produção e utilizá-los de acordo com o contexto de cada empresa. Contexto esse determinado pelos custos relativos de fatores de produção, pelas questões econômicas vigentes. Então o Sistema Toyota de Solução, que originalmente, havia sido construído para uma realidade da produção de baixos volumes e muita variedade, como muito bem coloca os autores que tratam do tema, teve a oportunidade no Brasil de desenvolver soluções específicas para fábrica da Toyota que fazia até pouco tempo atrás o Bandeirantes, criando soluções que foram tão relevantes que foram, de novo, exportadas do Brasil para a Toyota do Japão. História bonita e que realmente representa o pensamento autônomo. Taiichi Ohno não tomou as mesmas decisões técnicas no Brasil e na estrutura japonesa porque realidades distintas exigem que os princípios, métodos e técnicas - que são muito bons e são centrais no Sistema Toyota - sejam aplicadas tendo em conta realidades econômicas que são diferentes de empresa para empresa, que são diferentes de locais para locais, de países para países.
Ivan: De fato é um caso muito inspirador, é um excelente exemplo da criatividade da mão de obra da mente de obra brasileira. Mas, Junico, olhando agora para a sua experiência e para a experiência da produttare, você diria que a aplicabilidade do sistema Toyota de produção ela é ampla, ela pode ir o sistema troca pode ser utilizado como pano de fundo para estruturar sistemas de produção para quaisquer setores da economia ou existem alguns setores onde não se aplicaria? Como é a experiência da Produttare? Tem muitos setores que já avançaram, que estão mais maduros, mas outros que ainda não, não é isso?
Junico: Na verdade o Sistema Toyota de Produção é um sistema que funciona muito bem nas empresas de pequeno porte, de médio porte e empresas grandes. Isso significa você tem uma espécie de equação diferencial geral. Existem algumas coisas que são gerais, conceitos fundamentais e universais dos Sistema Toyota de Produção e existem condições de contorno, diferentes realidades econômicas financeiras. Dado que você tem um conjunto de princípios, técnicas e métodos universais bastante bem construídos que nós vamos falar certamente no futuro nas outras entrevistas, como você tem realidades econômicas distintas, você tem que adaptar essa soluções gerais para a realidade econômico-financeira de cada uma das empresas, cada um dos países. Por exemplo no Brasil, que você tem uma dificuldade de utilização dos ativos, que os ativos são caros, que os equipamentos são caros, que as taxas de juros que permitem chegar esse investimento para comprar equipamentos de fato são bastante altos, nós temos que usar da melhor maneira esses equipamentos. Então nosso problema talvez não eu seja a força minimizada do trabalho, seja a melhor utilização possível dos ativos da minha empresa, beleza? Isso não significa que não vou abandonar o conceito de força minimizada trabalho, significa que nós vamos olhar a realidade brasileira e perceber quais são os temas centrais. Um dos temas centrais e nós viemos trabalhando nas empresas exatamente as ideia da força, a ideia do aumento do Índice de Rendimento Operacional Global dos Equipamentos. Vale aqui dizer que isso é perfeitamente possível, dessa maneira, com os mesmos ativos, tu vai ter um resultado de lucro líquido, retorno sobre investimento muito maior. E o recado é realmente é final importante desse ponto de vista é exatamente que nós precisamos, Ivan, trabalhar as ideias sem ortodoxia. nós temos que dominar os conceitos seminais do Sistema Toyota de Produção. Não porque as isso seja historicamente importantes, é também historicamente importante, mas porque, além de historicamente importantes, lá existe uma teoria geral de produção. Sistema Toyota de Produção é constituído de mecanismo da função de produção, das redes, dos processos e das operações. E esse sistema, quando adaptado para a realidade econômica distinta, ele exige que a gente crie sistemas específicos que levem em consideração essas realidades contextuais. Resumindo, tudo é baseado na Engenharia de Produção Lucrativa. Eu gostaria que os leitores tivessem acesso às obras seminais do sistema do STP para compreender com muita profundidade esse conceito de Engenharia de Produção Lucrativa.
Ivan: Muito bom, Junico. De fato, a experiência da Produttare tem mostrado que esses conceitos são aplicáveis em diversos setores, a gente tem tido oportunidade de aplicação na construção civil, em hospitais, além do metal mecânico, que você já citou, têxtil, calçados, auto peças, enfim, uma grande diversidade de setores que consegue se aproveitar, vamos dizer assim, dessas metodologias, desses conceitos para alavancar seus resultados, não é? E para finalizar essa nossa entrevista, Junico, eu gostaria que você também aproveitasse um pouquinho mais dessa sua experiência acumulada e todos esses anos falando a respeito de resultados. Empresas que estão iniciando essa trajetória de caminhada em relação a excelência operacional, estruturando suas departamentos de melhoria contínua, que os resultados principais normalmente são alcançados quando as empresas têm êxito nessa espaços iniciais?
Junico: Em primeiro lugar e já provocando para eventuais outras conversas que a gente possa ter, é muito importante saber que como o STP é baseado numa teoria geral de produção, ela pode ser aplicada num cem números de setores. Hoje em dia, você tem o nome disso não é muito mais dominado pela ideia do Lean, então você tem Lean Manufacturing, você tem Lean Enterprise, você tem Lean Construction, você tem Lean Health Care, você tem Lean service, etc. Ou seja, é uma uma uma lógica de aplicação universal em função de que o STP está baseado, na verdade, foi de que gerou uma teoria geral de produção. Isso permite que você alcance resultados em diferentes segmentos industriais, eu vou dar um exemplo aqui, que é um exemplo importante genérico, feito o trabalho no estaleiro importante no Brasil, onde você tinha uma situação que o conjunto de trabalhadores é expressivo, na verdade bastante alto, e que havia aí, nesse estaleiro, um resultado de lucro líquido menor que zero. Na verdade nós temos aí uma estrutura de prejuízo, mas bastante moderno estaleiro, de quarta geração, estaleiro realmente importante para a realidade brasileira.
Foi feito um trabalho coletivo, envolvendo muitas pessoas, sob coordenação de uma liderança muito forte nesse tema e esse trabalho levou aí talvez 3-4 anos para ser elaborado. O que aconteceu é que o estaleiro anteriormente fazia meio navio por ano com conjunto as pessoas aí talvez estimado ao redor 6 mil pessoas e tendo um prejuízo operacional razoável, que não veio caso aqui discutir. Quatro anos depois, esse mesmo estaleiro, através da melhoria da atenção dos ativos, com a utilização muito forte do Lean Manufacturing e STP, nós passamos a fazer aí 4 navios por ano, de maneira geral, com menos os trabalhadores, com 3.500 trabalhadores, então resultado positivo na organização. E assim o princípio básico da Produção do Lucrativa que fez com que os empregos em estaleiros se conservasse em por um tempo muito grande, porque na verdade as organizações que trabalham no prejuízo elas não se sustentam economicamente no médio-longo prazo. Então alí foi adotado sem dúvida nenhuma o princípio do STP, o princípio da engenharia de Produção Lucrativa porque, vejam, nós permanecemos com os mesmos ativos, basicamente mesmo estaleiro com algumas poucas exceções de alguns investimentos irrisórios para os padrões gerais de operação, e você aumentou em 16 vezes a produtividade das pessoas, porque se fez oito navios e diminuiu em dois as pessoas. Por evidente o nosso objetivo não é diminuir as pessoas. Se estaleiro evidentemente no futuro trabalhar pesadamente, nós vamos avançar competitividade, ainda com pouco vamos retomar esses empregos na organização. Isso é um exemplo claro da Engenharia de Produção Lucrativa. Quando em vez de você pensar em investir, você vai pensar em utilizar da melhor maneira os seus ativos, sejam eles ativos de capital, sejam ativos de conhecimento em métodos e pessoas, e fazer com que o emprego melhore, com que a competitividade melhore, com que todo o país vá para frente, com que se gera imposto e que nós possamos trabalhar ativamente a nível mundial.
Ivan: Excelente, Junico. Muito obrigado pela sua participação nesse nosso canal nesta data e por ter trazido contribuições tão relevantes para os nossos ouvidos. Por favor, fique à vontade para as suas considerações finais e para uma mensagem final para o nosso público.
Junico: Eu gostaria de novamente agradecer a oportunidade dessa a entrevista, Ivan, de trocar ideia aí com os nossos ouvintes. E também de dizer que eu espero que a gente possa ter oportunidade futura de discutir com mais detalhes o Sistema Toyota de Produção raiz, ou seja aqueles processos essenciais que são muito importantes para a competitividade das empresas nacionais. Eu incluiria depois da Engenharia de Produção Lucrativa, que, no meu ponto de vista, é central, os debates sobre de que se constitui o sistema de produção, o que é uma rede de processos e operações, o que é uma função processo, o que é função operação, como você faz melhorias na função processo, enfim, ampliar a nossa conversa com os ouvintes em relação ao que eu sempre gosto de dizer a Engenharia de Produção raiz, que tá lá no Sistema Toyota de Produção. Previdente não é a única contribuição. Teoria das restrições é fundamental, o Seis Sigma é fundamental, os conceitos estratégias de Produção Skinnerianos são fundamentais, nós temos agora os conceitos modernos associados aos elementos habilitadoras da indústria 4.0 são fundamentais, a questão da IoT, os debates Robot Automation, tudo isso são centrais. Mas eu acho que é fundamental para os ouvintes compreender as bases fundamentais que geram a competitividade, seja no setor industrial, seja na construção civil, seja nos serviços. E isso depende do aprofundamento dos conceitos básicos.
Ivan: Ok, Junico. Muito obrigado a você, a nossa equipe que organiza que o Podcast Produttare. Parabéns aí pelo enfrentamento dos desafios constantes junto às empresas brasileiras, especialmente nesses tempos cada vez mais competitivos. Mais uma vez então o nosso muito obrigado também aos nossos ouvintes por participarem do Podcast Produttare. E e eu tenho um pedido especial: aqui é Ivan De Pellegrin, sócio-diretor da Produttare, você que nos ouve se tem algum comentário, alguma pergunta a respeito desse podcast, por favor comente conosco diretamente pelo e-mail contato@produttare.com.br. Abraço a todos.
A Produttare adota diretamente o conceito de Engenharia de Produção Moreku. Isto implica em evitar, sistematicamente, a adoção de soluções prontas e universais, e a ideia de que existem métodos e técnicas milagrosas que resolvem todos os problemas para todas as empresas, em qualquer momento do tempo. A ideia perseguida consiste em tratar as diferentes situações e contextos econômicos de forma dinâmica e específica, tendo como pontos centrais: I) uma compreensão ampla da microeconomia da fábrica e seus desdobramentos em termos dos custos dos fatores de produção envolvidos (capital, trabalho, energia, matérias-primas e materiais); II) possuir um modelo/framework de referência, que intitulamos de Sistema PRODUTTARE de Produção, e que deve ser dinamicamente adaptado e melhorado levando em conta o contexto microeconômico e a estratégia de negócios e produção de cada empresa em particular. Tal tema será abordado em nossos próximos artigos.