Lean Construction além da construção civil: case Kepler Weber
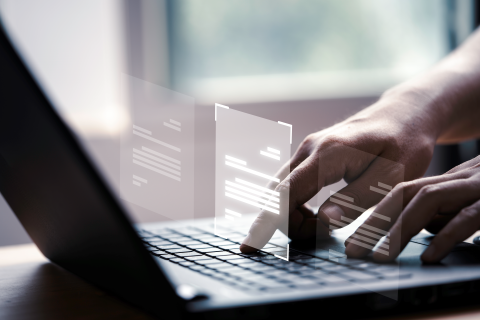
Por: Admin - 25 de Agosto de 2020
Neste vídeo, Diego Wenningkamp, gerente executivo de Implantação de Projetos da Kepler Weber, e Eduardo de Oliveira, diretor e consultor-sênior da Produttare Lean Construction, apresentam as etapas de implantação para o Lean Construction na Kepler Weber.
A Kepler Weber é uma empresa que oferece para o mercado soluções pós colheita e, além de fabricar os produtos, disponibiliza aos seus clientes o serviço de montagem de seus produtos e gerenciamento de obras.
Visando reduzir perdas, custos com mão de obra, infraestrutura e equipamentos, além de reduzir o prazo de entrega, a empresa buscou inovar seus serviços implantando a filosofia enxuta: Lean Construction.
O vídeo também explora o sistema Last Planner e as oito etapas da metodologia Takt Planning utilizadas na implantação do Lean Construction nas obras da Kepler Weber.
Este vídeo foi extraído do evento on-line "Lean Construction além da construção civil". Clique aqui para assistir o webinar na íntegra.
A empresa
A Kepler Weber é uma empresa que fornece soluções de pós colheita, com unidades fabris em Panambi/RS e Campo Grande/MS, além de um escritório corporativo em São Paulo/SP. Suas duas plantas industriais são capazes de produzir anualmente mais de 5 milhões de toneladas em armazenagem de grãos.
A companhia possui três pilares estratégicos: produtos, serviços e relacionamento. No pilar produto a empresa já possui alto reconhecimento no mercado, mas vem buscando fortalecer os pilares de serviços e relacionamento.
No pilar de serviços, a Kepler Weber se posiciona como uma empresa de Engenharia da Construção no Agronegócio, idealizando, projetando, planejando, montando e entregando para seus clientes o empreendimento adquirido.
Após a compra dos produtos da empresa, o cliente acaba obrigatoriamente passando por uma obra, visto que os produtos são entregues desmontados.
Objetivando proporcionar uma excelente experiência ao cliente, a empresa passou a ofertar seus serviços de Engenharia de Construção. Focando no agronegócio, trabalha com mais de 150 obras simultâneas em todo o país. Em 2019, foram 275 obras de armazenagem e 8 obras industriais. Ou seja: 75% das obras referentes aos seus produtos foram montadas pela empresa.
Roadmap Jornada Lean Construction
A Kepler Weber tem como filosofia o conceito Lean. Iniciou a implantação da metodologia na fábrica em 2015 e em suas obras em 2017.
O Lean é uma jornada de transformação cultural, sendo necessárias algumas etapas para engajamento e entendimento da equipe. Assim, Diego apresenta o Roadmap da empresa de 2017 a 2021.
Em 2017, foi iniciado o processo interno com o mapeamento do fluxo de valor e simplificação dos processos através de visitas ao geomba (fábrica) e a padronização das rotinas.
Em 2018, foi dado início a integração de cronogramas entre a fábrica e a montagem dos produtos, além da construção de padrões de montagem e reestruturação da equipe no campo.
Em 2019, o programa atingiu estabilidade e, assim, houveram entregas técnicas importantes para empresa. Foi elaborado o programa de desenvolvimento de empreiteiras (PDEK) e capacitações das empreiteiras, chamado de KW University.
Em 2020 iniciaram-se projetos de Lean no campo, buscando excelência operacional, capacitação das pessoas envolvidas, entre funcionários e parceiros, para que, assim, seja possível captar ganhos para a empresa, seus parceiros e clientes.
Fluxo de implantação de projetos
O serviço não é formado só por processos, mas, principalmente, por pessoas. Por isso a empresa visa o engajamento da equipe, além de processos eficientes.
A Kepler elaborou seu fluxo de implantação com as seguintes etapas:
- Engenharia de aplicação: Após a decisão de compra do cliente é realizado o desenvolvimento do projeto com a melhor solução e layout para o cliente.
- Planejamento da obra: Esta etapa consiste em reuniões pré-obra com o cliente, criação de cronograma detalhado e plano de ataque monitorado através de gestão visual chamada “esteira de gerenciamento de obras”, controle de requisitos legais para uma segurança jurídica, seguro de risco de engenharia e contratação de empreiteira certificada pela empresa.
- Execução da obra: Equipes no campo organizadas em quatro regionais, dimensionadas para estarem próximos do cliente e gerenciarem os projetos. Também são realizadas reuniões frequentes para garantir o alinhamento com o cliente. Nas obras é possível observar canteiros com organização padrão e gestão visual.
Todas as obras são montadas por parceiros, somando mais de 1.500 pessoas indiretas trabalhando para Kepler e gerenciadas através do Programa de Desenvolvimento de Empreiteiras Kepler (PDEK).
O PDEK conta com um programa de incentivo e bonificação além da KW University, com módulos de desenvolvimento na área de gestão de pessoas, gestão financeira, gestão estratégica, saúde e segurança, execução da obra e lean construction.
- Entrega técnica: Após a montagem, a equipe realiza a entrega técnica com testes a vazio e com produto, treinamento teórico e prático para operadores e operação assistida para garantir o melhor funcionamento dos equipamentos.
- Suporte técnico e garantias: a empresa mantém uma sala de operações para dar suporte durante a obra ou na vigência do prazo de garantia, para resolver de forma rápida qualquer problema ou esclarecer dúvidas.
Projeto Piloto
Para o projeto piloto de Lean Construction na Kepler Weber, foi definida uma obra de porte médio composta por silos de armazenagem, silos pulmão, secador e elevadores.
Para identificação e comunicação do projeto na obra, foi desenvolvida uma placa com a descrição do projeto para que todos os trabalhadores e parceiros tenham conhecimento.
Deu-se início ao projeto piloto no final de março de 2020. Em função da pandemia, foi iniciado de forma remota. De acordo com o planejamento inicial, a montagem mecânica seria executada em 6 meses, iniciando-a em junho de 2020.
Visto que a empresa já possuía um trabalho de padronização anterior, foram utilizados os tempos de ciclo já existentes no trabalho padrão e validados pelo empreiteiro, o envolvendo desde o início.
Sistema Last Planner como pilar
O projeto tem como pilar o sistema Last Planner, que é composto por eventos e rotinas que são interligados dentro do sistema de produção.
O pilar é composto por dois eventos:
- Master Planning: neste evento a empresa já possuía planejamento geral da obra bem consolidado, como os marcos, os equipamentos e seus planejamentos, assim como a quantidade de pessoas necessárias.
- Pull Planning das frentes: este evento consiste em elaborar um planejamento puxado, mapeando quais equipamentos são mais importantes e identificando oportunidades de ganho. É nesta etapa que é utilizado o conceito de Takt (ritmo da produção).
Para identificar e prevenir as restrições que possam acontecer nos eventos, este pilar estabelece rotinas:
- Reunião de 6WLA: planejamento de médio prazo onde são visualizadas as restrições vinculadas nas atividades, a fim de elaborar um plano de ação para mitigá-las ou eliminá-las, de forma que o projeto tenha estabilidade.
- Programação semanal: após a construção do planejamento de médio prazo, é realizada uma programação semanal, dia a dia, com plano congelado.
- Aprendizagem: acompanhamento diariamente do processo, hora a hora, para aprender com os problemas e as dificuldades.
Metodologia “Takt Planning”
Foi utilizado o método “Takt Planning”, de forma a identificar os fluxos repetitivos e balancear as equipes para buscar oportunidades de redução de prazo e custo da obra.
Se associarmos as equipes por onde um produto passa num fluxo como um trem, onde todos os vagões devem andar no mesmo ritmo, percebemos que todas as equipes do fluxo devem também trabalhar no mesmo ritmo para que a obra seja mais eficiente.
Esta metodologia é composta por 8 etapas:
- Divisão em partes e definição do tamanho de lote
- Identificação do sentido construtivo
- Encadeamento das atividades
- Definição do quantitativo
- Identificação das equipes mínimas
- Cálculo takt time
- Ajuste das equipes por atividade
- Elaboração da programação
Divisão em partes, definição do tamanho de lote e identificação do sentido construtivo
Para iniciar é necessário entender como é realizada a montagem dos equipamentos. Para isso, nas etapas 1 e 2, foram escolhidos equipamentos que tivessem maior impacto na redução do lead time ou de custos, e, após estudar com a equipe a sequência de montagem, foram identificados os fluxos repetitivos, como, por exemplo, quatro atividades em duplicidade encontradas na montagem de silos.
Com a análise da sequência de montagem e fluxos foi possível definir o tamanho do lote de cada fluxo e o sentido construtivo.
Encadeamento das atividades
Na etapa 3, foi estudado cada fluxo para entender quais atividades seriam encadeadas. É nesta etapa que a equipe explora todas as possibilidades, discutindo sobre a sequência, agrupamento e eliminação das atividades, bem como a possibilidade da realização de uma pré-montagem na fábrica.
Também é possível identificar atividades restritivas, podendo ser projetado um buffer para absorver variações e proteger as demais atividades.
Definição do quantitativo
Na etapa 4, como o auxílio do projeto, foi definido o quantitativo de cada atividade, ou seja, qual o nível de dificuldade para executar certa atividade em um lote. Por exemplo: quantos parafusos deverão ser utilizados em uma chapa se o lote for uma peça.
A partir da determinação do tamanho do lote, devem ser analisados os quantitativos que irão provocar maior ou menor dificuldade para execução da atividade no lote. Esta etapa dará suporte à etapa 5, para determinação dos recursos necessários.
Identificação das equipes mínimas
Na etapa 5, a partir da análise do quantitativo das atividades, busca-se entender qual a menor composição de equipe e qual a produtividade padrão para cada atividade.
Ao longo do projeto, foi de enorme importância a participação dos empreiteiros e o entendimento dos mesmos quanto à real necessidade de se alcançar a produtividade.
Contudo, vale ressaltar que se deve buscar a produtividade já realizada neste momento e não estipular metas desafiadoras.
Cálculo takt time e ajuste das equipes por atividade
Ao identificar a menor composição possível e a produtividade, é inserido na análise o takt time, que é o ritmo para alcançar o prazo inicial.
O cálculo para encontrar o takt time na construção civil é diferente da produção, visto que, na fábrica, ao encher a linha, dificilmente será esvaziado o fluxo, o que na obra acontece a todo momento.
A partir da análise do takt time, ajustasse as equipes para atendê-lo, reduzindo a distância entre ele e o tempo de ciclo, consequentemente reduzindo desperdícios.
Elaboração da programação
Após analisar o takt time e ajustar as equipes de todos os 16 fluxos, correspondentes a 6 equipamentos, foram retornadas as informações para o planejamento de longo prazo.
Ao analisar o novo planejamento de longo prazo é possível observar que há oportunidade de redução de 2 meses no lead time da obra e 32% no custo, embora a equipe tenha 2 pessoas a mais.
Oportunidades identificadas e planejamento de longo, médio e curto prazo
A partir da definição do planejamento de longo prazo é necessário desmembrá-lo para um planejamento de médio prazo, entendendo as restrições e os possíveis impactos no fluxo.
Para que o fluxo produtivo não sofra interrupções é necessário gerenciar as restrições, ou seja, administrar os entregáveis dos processos de apoio, garantindo a estabilidade do projeto.
Com isso, foi criada uma sistemática de médio prazo, olhando seis semanas à frente, vinculando as restrições com as atividades.
Após a elaboração do planejamento de médio prazo é feito o desdobramento para o planejamento de curto prazo em conjunto com a equipe da obra, abrindo as atividades para que seja possível avaliar diariamente o PPC (Percentual de Planos Concluídos) da semana atual e da próxima.
Métodos de controle e aprendizado
Para fluxos com takt time abaixo de uma hora, a equipe introduziu quadros hora-hora para controle, visto que os ritmos são curtos e necessitam avaliação frequente para não pararem.
O quadro auxilia no aprendizado e no acionamento rápido da cadeia de ajuda quando houver problemas.
Para fluxos com takt time acima de uma hora foi desenvolvido um quadro para avaliar o distanciamento entre as equipes na execução de suas atividades.
Após todo planejamento executado, foi confeccionado pela equipe o relatório A3 para acompanhamento do projeto.
Estes controles e gerenciamento dos planejamentos são importantes para mensurar todos os ganhos e eventuais oportunidade como aprendizado.