Perdas Ambientais no Processo Produtivo em uma Indústria Metal-Mecânica – Um Estudo de Caso
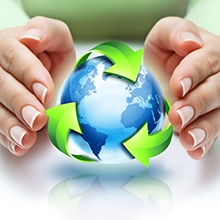
Por: Admin - 03 de Dezembro de 2014
Autores:
Eliane Cortez (UNILASALLE) eliane@lasalle.tche.br
José Antonio Valle Antunes Júnior (UNISINOS) junico@produttare.com.br
Marcelo Klippel (UNISINOS) marcelo@klippel.com.br
Resumo
O presente artigo consiste em um Estudo de Caso sobre a implementação de novas alternativas de gestão ambiental em uma indústria do setor metal-mecânica através da estruturação de um Sistema de Gestão Ambiental - SGA. A partir do modelo genérico proposto por Sarkis e Rasheed (1995) e Chebehe (1998) é proposto um modelo específico de redução de resíduos pela eliminação de perdas internas no sistema produtivo. A idéia consiste em controlar os resíduos gerados durante o processo produtivo, em contraposição a fazê-lo no final da Operação.
O modelo proposto visa constituir-se em uma ferramenta eficaz para o controle dos resíduos gerados nos Sistemas Produtivos. Visando apresentar uma aplicação prática do Modelo Proposto é estudado um caso prático na Indústria Metal-Mecânica.
Palavras chave: Perdas, Gestão Ambiental, Sistema.
1.) Introdução
Nos dias atuais a consciência ecológica se amplia na sociedade. As empresas voltam-se cada vez mais para um maior comprometimento com seus consumidores com relação às questões ambientais. Observa-se uma tendência no sentido do incremento da demanda por produtos não ofensivos ao meio ambiente.
O presente artigo parte das considerações de Sarkis e Rasheed (1995) e Chehebe (1998) relacionadas com a Análise do Ciclo de Vida - ACV dos produtos. O Modelo proposto por Sarkis e Rasheed é genérico. Trata da temática da gestão ambiental nas Fases de Obtenção, Produção e Distribuição. De acordo com Chehebe (1998), a ACV encoraja as indústrias a sistematicamente consideraram questões ambientais associadas aos sistemas de produção: insumo, matéria-prima, manufatura, distribuição, uso, disposição, reciclagem, o ciclo de vida do produto. O presente estudo de caso é focado na parte do processo global que trata da redução dos resíduos pela eliminação de perdas internas no processo produtivo.
2.) Considerações sobre a empresa objeto do Estudo de Caso
A empresa onde o trabalho foi realizado localiza-se na cidade de São Leopoldo, Rio Grande do Sul. Atua no ramo metalúrgico, fabricando bombas centrifugas e helicoidais de cavidade progressiva. Em 1996 a mesma foi adquirida por uma indústria americana, que fabrica e abastece campos petrolíferos com equipamentos de perfuração de poços de petróleo.
A empresa conta com 175 funcionários e é considerada de médio porte. A fábrica trabalha com um sistema de produção misto (linha e/ou células), onde são produzidos cerca de 600 itens distintos, desde aqueles utilizados para a montagem dos produtos até os necessários para disponibilizar peças de reposição.
A empresa tem implementado um sistema da qualidade sólido que faz parte de sua cultura, tendo recebido a certificação ISO 9002 em 1997. A mesma utiliza, de forma sistemática, ferramentas de melhoria da qualidade tais como: CEP – Controle Estatístico de Processo, ensaios de confiabilidade, auditoria de fornecedores e outras que permite a melhoria e possibilita sustentar a introdução de novas abordagens como é o caso do Sistema de Gestão Ambiental - SGA.
3.) Referencial Teórico
De acordo com Cortez (2000) é proposta uma adaptação da estrutura estabelecida por Chehebe (1998) e da ACV proposta por Sarkis e Rasheed (1995), de forma que a redução de resíduos pela eliminação perdas internas, com foco na produção, tenha como base o Sistema de Gestão Ambiental – SGA da Empresa, conforme apresentado na Figura 1.
Figura 1 - Estrutura de mudança construída a partir da adaptação das propostas por Chehebe (1998) e Sarkis e Rasheed (1995)
Fonte: Cortez (2000, pg. 57)
Para a implementação do SGA é importante a mudança comportamental da alta gerência. Isto possibilita que seja iniciado e mantido um amplo e contínuo processo de mudança. A qualidade ambiental pressupõe a implantação dos princípios e técnicas do SGA e conduz a uma mudança de mentalidade, objetivando a realização de um amplo leque de melhorias.
Na estrutura proposta na Figura 1: i) a Qualidade ambiental considera, além dos princípios propostos para implementação do SGA, a manutenção de um clima voltado para a implementação de melhorias; ii) a ISO 14001 constitui-se em uma ferramenta útil para a empresa controlar efetivamente seu desempenho ambiental; iii) o Clima organizacional deve propiciar a implementação dos princípios e técnicas do SGA através da aceitação e participação dos funcionários da empresa no processo de mudanças; iv) o Aumento da moral dos trabalhadores e o respeito à condição humana tornam-se cada vez mais importantes por influenciarem diretamente na saúde do trabalhador e no seu rendimento profissional e v) a Qualidade ambiental assegurada pode ser conseguida através da identificação e monitoramento de fatores do meio-ambiente, tais como gases, poeira, vapores, luz, ruído, temperatura, ventilação e umidade.
Para a efetiva busca da qualidade ambiental e redução ou eliminação de resíduos, este artigo propõe que o processo seja entendido a partir da ótica de um modelo específico proposto, explicitado na Figura 2, identificando os materiais que entram e saem de cada operação do processo.
Figura 2 – Modelo específico proposto para o tratamento das perdas ambientais
internas dos sistemas produtivos da indústria metal-mecânica
Fonte: Cortez (2000 pg. 62)
O modelo específico proposto demonstra que o processo produtivo recebe o aporte de insumos para a produção, de duas vias distintas. Da mesma forma, os resultados do processo são identificados em duas vias distintas.
No Sistema Principal a matéria-prima entra no processo, percorre todo o fluxo produtivo, sendo encontrada no produto acabado.
Neste Sistema Principal o que sai do processo compreende: i) o material em processo; ii) o refugo; iii) o retrabalho e iv) o subproduto, como sendo todo o resíduo proveniente da matéria-prima. As perdas geradas durante o sistema principal são contabilizadas, recebem um tratamento denominado, pelo modelo específico proposto, de Tratamento 1 - T1 que é a reutilização.
Por sua vez, neste modelo, no Sistema Secundário entram os materiais indiretos, que vêm a ser aqueles consumidos no posto operacional específico e que estão vinculados apenas ao funcionamento do mesmo, tais como: i) óleo lubrificante; ii) os produtos químicos e panos para limpeza e iii) os agentes refrigerantes. Neste Sistema Secundário, o que sai do processo são: i) os agentes refrigerantes contaminados que recebe Tratamento 3 – T 3, que é a disposição e posterior encaminhamento para depósito de resíduos industriais; ii) os panos para limpeza contaminados que recebe também Tratamento 3 – T 3; iii) os óleos lubrificantes vencidos que recebe o Tratamento 2 – T 2 e retorna ao processo como material indireto; iv) produto químico para limpeza contaminado que recebe também o Tratamento 2 – T2; v) agente refrigerante filtrado que recebe o Tratamento 4 – T4, reuso, retornando ao processo como material indireto e vi) agente refrigerante modificado, material com características originais modificadas que se dispersa no meio-ambiente e que não recebe tratamento no modelo proposto, tendo a identificação Tratamento 0 – T0.
A implementação de uma estrutura de SGA pressupõe um processo de mudança para a implementação de melhorias na Organização, o qual é realizado através da formulação de três perguntas (Goldratt, 1986): i) O que mudar?, correspondendo ao cenário inicial da Empresa; ii) Para o que mudar?, correspondendo à estrutura de mudança proposta para a redução de resíduos pela eliminação de perdas internas do processo produtivo através do SGA e iii) Como realizar a mudança?, correspondendo ao método de mudança proposto. O presente artigo propõe a redução de resíduos pela eliminação de perdas internas, com foco na produção, tendo como base o SGA. Na Figura 3 é proposto um método para a implementação do processo de mudança.
Figura 3 – Método para implementação do processo de mudança.
Fonte: Cortez (2000, pg. 67)
Para a Análise Global do SGA, a Figura 1 serve como referência, uma vez que o modelo proposto possibilita a visualização sistêmica dos processos produtivos. Para a Determinação dos processos críticos é necessária uma análise global do sistema produtivo da Empresa, possibilitando identificar qual é o processo considerado critico do ponto de vista de perdas internas. Uma vez identificados os processos críticos, é necessário identificar as perdas geradas pelos mesmos através de uma Análise detalhada das perdas. A Figura 2 serve como referência para a identificação, análise e tratamento dispensado às perdas.
Uma vez identificadas as perdas, deve ser montado um Plano de ação de melhorias dos processos produtivos, com vistas a auxiliar na implementação do processo de mudanças, seguindo-se as Ações para a implementação do plano de ação.
4.) Estudo de caso: Redução de resíduos pela eliminação de perdas internas nos processos produtivos em uma indústria do setor metal-mecânico
Umas das principais características observadas no processo produtivo da empresa é a diversificação de processos, em função da variedade de itens produzidos, o que ocasiona mudanças freqüentes nas características dos resíduos gerados durante a produção, implicando em um controle maior sobre os mesmos.
Os processos que envolvem tornos (CNC e convencionais), fresadoras, furadeiras, prensas, esmeril e puncionadores automáticos funcionam em sistema de células de produção. Atualmente a empresa trabalha com 10 células produtivas, produzindo cada uma, em média, 22 itens diferentes. Em um sistema de arranjo funcional estão estruturados os processos de vulcanização, solda, serra, jato de areia, pintura e bancada de testes.A produção mensal da Empresa é de em média 10.000 itens, sendo gerados diversos resíduos tais como papel higiênico (80 kg/mês); papel e papelão (400 kg/mês); plásticos (250 kg/mês); serragem com óleo (220 kg/mês); panos (800kg/mês); resíduos de varrição (120 kg/mês); latas com resíduos de tintas (160 latas/mês); latas de solventes e óleos (200 latas/mês); cavacos (24.000 kg/mês); óleo de bancada e de máquinas (350 litros/mês); borra de tinta (200 litros/mês); vidros (80 kg/mês); lâmpadas queimadas (30 unidades/mês); bombonas de óleo solúvel vazias (20 unidades/mês); lodo de jato de areia (2 kg a cada 6 meses); lodo de óleo solúvel (4 kg/mês) e lodo do tratamento do esgoto sanitário (30 kg/dia). Os gastos anuais da Empresa com transporte e disposição de resíduos ficam em torno de U$ 120.000. Este custo provavelmente pode ser reduzido com a implementação do SGA.
Seguindo o método proposto foi definido como processo crítico o processo de usinagem. Isto porque o mesmo gera perdas provenientes da matéria-prima e materiais indiretos que comprometem o SGA. Através da observação, o problema selecionado para análise foi a necessidade de diminuir a quantidade de resíduos e emissões gerados neste processo. Considerando os princípios do SGA e os propostos pela ISO 14001 para melhoria contínua, as alternativas julgadas mais interessantes para a solução do problema foram: i) especificar a quantidade de liquido refrigerante a ser aspergido sobre a peça, conforme a característica do material que está sendo usinado e ii) estabelecer melhorias no processo de usinagem.
Para o desenvolvimento deste eestudo de caso foram selecionadas três células, sendo que dos 22 itens produzidos por estas células foram escolhidos três para serem analisados. Para caracterizar o processo de usinagem, quanto à geração de cavacos e emissões de agentes refrigerantes, as três células produtivas selecionadas foram identificadas como célula E, célula F e célula G, nas quais são produzidos, respectivamente, os itens Cruzeta, Eixo para haste e Rotor. Os itens selecionados para o estudo de caso são dos segmentos de bombas helicoidais e cabeçotes para acionamento de bombas de captação de petróleo, a saber: i) Cruzeta – material ASI 420, utilizada em uma bomba 4HF 60L; ii) Eixo para haste – material SAE 4140, componente utilizado no cabeçote para acionamento de bomba 940-80 e iii) Rotor – material ASI 304, utilizado em bomba HX-80.
O item cruzeta é produzido na célula E que contém tornos mecânicos, tornos CNC, furadeira coluna 25, fresadoras e cabinas para rebarba; o item eixo para haste é produzido na célula F que contém tornos mecânicos, tornos CNC, centro de usinagem, furadeira coluna 25, fresadoras e cabinas para rebarba e o item rotor é realizado na célula G que contém tornos mecânicos, tornos CNC, torno MKD, turbilhonador, furadeira radial, fresadoras e cabinas para rebarba.
Nos meses de fevereiro a abril de 2000 foi realizado um acompanhamento sistemático das células E, F e G, na produção dos itens selecionados, com o objetivo de verificar: refugo, retrabalho, geração de cavacos e a emissão e utilização de agentes refrigerantes, tendo-se coletado os dados mostrados na Figura 4.
Figura 4: Dados coletados nas células E, F e G
A produção mensal de cavaco na Empresa é de 24.000 kg, sendo que, dos itens selecionados, o que mais gera cavaco é o rotor. Durante a usinagem deste item é utilizada uma grande quantidade de agente refrigerante para resfriar o material usinado.
Os agentes refrigerantes constituem-se em agentes nocivos ao homem e ao meio ambiente. O comprometimento do ar no local de trabalho, em decorrência do uso de aerossóis e dos vapores de agentes refrigerantes, varia em função, por exemplo, das propriedades físico-químicas dos refrigerantes, da velocidade de rotação das peças que estão sendo usinadas e do aquecimento das superfícies.
A avaliação toxicológica dos refrigerantes depende de sua composição química.A partir de 1999, a empresa iniciou um trabalho de determinação simultânea da concentração de aerossol de óleo e de vapores. O processo de medição realizado no mês de Março/2000 determinou todos os hidrocarbonetos computados na amostra de ar, tantos os emitidos pelos processos operacionais relacionados com o local de trabalho, quanto os emitidos por processos de trabalho periféricos. A Figura 5 apresenta os resultados das medições. Os valores obtidos para concentração de agentes refrigerantes no ar comprovam que na célula produtiva G, na qual são utilizados principalmente agentes refrigerantes não solúveis em água, o teor de vapor é mais alto do que o teor de aerossol, ultrapassando o limite recomendado.
Figura 5 – Medição de aerossol, vapor e vapor de aerossol nas células E, F e G
A aplicação na célula G do modelo proposto na Figura 2, para a redução de perdas internas no sistema produtivo da indústria metal-mecânica é representado na Figura 6.
Figura 6 – Aplicação do modelo específico proposto para a redução de perdas internas
no sistema produtivo da indústria metal-mecânica
Dentre os materiais indiretos identificados, o mais critico, por sua ação contaminante, foi o agente refrigerante. O cavaco, considerado perda, constitui-se em um subproduto gerado a partir da matéria-prima, e deve sofrer um tratamento para reciclagem e retorno ao processo como matéria-prima. Ele é um subproduto gerado durante a etapa do processo que é enfocado pelo sistema principal, mas como não é considerado perda por este sistema, ele é tratado pelo sistema secundário.
Recebe um tratamento denominado de Tratamento 2 – T2, reciclagem. A reciclagem, na dimensão do SGA, prevê o retorno ao processo em forma de matéria prima.
5. Análise do Sistema de Gestão Ambiental – SGA na empresa a partir do modelo proposto
O modelo proposto de gestão global do sistema ambiental – Figura 1 – constitui-se em um modelo genérico que serve como base para implantação do SGA e a partir do mesmo foi construído o modelo específico que analisa perdas no processo produtivo – Figura 2.
Uma vez identificadas algumas operações que compõem o mecanismo do processo de usinagem e analisando-as, sob a ótica de melhorias do processo, tornou-se possível identificar perdas existentes nas mesmas. Na análise realizada na empresa, foram identificadas: i) perdas energéticas que ocorrem nos processos em que o item passa pela mesma operação repetidas vezes, como no item rotor, na qual a operação de usinar a barra é realizada em três passadas, gerando maior consumo de energia elétrica; ii) perdas ambientais foram identificadas nesta mesma operação, sendo que a concentração de vapor e aerossol de agentes refrigerantes é maior na célula que produz este item.
Não há padronização para a checagem das máquinas e equipamentos antes do início das operações, gerando paradas de manutenção que constituem perdas por falta de padronização. A análise de algumas operações do processo de usinagem possibilita a identificação destas perdas, a sua posterior eliminação através da implementação de melhorias e padronização das operações, com a conseqüente redução de resíduos como cavacos e agentes refrigerantes. Estas ações constituem-se em elementos importantes no contexto do processo de implantação do SGA.
6. Conclusões
O objetivo principal deste estudo de caso foi propor um modelo geral de estrutura de mudança em SGA. A partir deste modelo específico é possível eliminar, de forma eficaz, as perdas internas nos sistemas produtivos em empresas do ramo metal-mecânico.
O modelo genérico proposto auxilia a: i) análise global do SGA da empresa; ii) visualização sistêmica do processo produtivo; iii) início de um processo de mudanças para a implementação e técnicas do SGA na empresa e iv) implementação do SGA na empresa. Para a efetiva implementação do SGA, este Estudo de Caso propôs que o processo produtivo da Indústria Metal-Mecânica em cena fosse entendido a partir da ótica do modelo específico proposto, o qual permite: i) a análise individual de entradas e saídas de materiais indiretos no processo; ii) a análise sistêmica de entradas e saídas de materiais indiretos no processo; iii) verificar a quantidade e qualidade dos materiais que saem do processo; iv) identificar cada material e o tratamento que deve ser dado ao mesmo e v) identificar os materiais com potencial poluidor.
Com base na análise do modelo específico proposto tornou-se possível elaborar um plano de ação para identificar e eliminar perdas internas nos processos produtivos. Este modelo pode ser considerado uma ferramenta de melhoria contínua, devendo ser utilizada como apoio na implantação do SGA.
Este Estudo de Caso permite concluir, também, que: i) a identificação e eliminação de perdas no processo produtivo – geração de resíduos e de emissões líquidos e gasosos – constitui-se num princípio básico para a redução dos custos globais de produção; ii) o SGA só terá possibilidade de sucesso se houver o comprometimento da administração para sua implantação e contar com a efetiva participação de todos os funcionários, os quais devem estar devidamente preparados e treinados e iii) a empresa necessita dispor de informação sobre as possibilidades de implantação de técnicas de SGA, visando reduzir os resíduos gerados, melhorar a qualidade dos produtos e obter ganhos econômicos.
Finalmente, o artigo mostrou, a título de exemplificação, a aplicação específico em uma parte do Sistema Produtivo da Empresa estudada.
7. Referências
CHEHEBE, B. José Ribamar (1998). Análise do Ciclo de Vida de Produtos. Rio de Janeiro: Ed. Qualitymark.
CORTEZ, Eliane (2000). Estruturação de Modelo que busca a redução de resíduos pela eliminação de perdas internas: uma experiência no setor metal-mecânico. Dissertação de Mestrado PUCRJ.
SARKIS, Joseph, RASHEED, Abdul (1995). Greening the Manufacturing Function. Business Horizons, September-October.