Princípios Básicos de Construção de Sistemas de Produção com Estoque-Zero / Sistema Toyota de Produção – Uma Abordagem Analítica
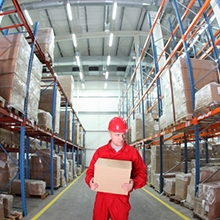
Por: Admin - 29 de Dezembro de 2014
Autores:
José Antonio Valle Antunes Júnior (UNISINOS) junico@produttare.com.br
Marcelo Klippel (UNISINOS) marcelo@klippel.com.br
Rodrigo Pinto Leis (UNISINOS) rodrigo@efact.com.br
Resumo
O presente artigo busca apresentar as principais questões envolvidas com a construção de Sistemas de Produção com Estoque Zero, originalmente conhecidos como Sistema Toyota de Produção. Para tanto, os autores analisam criticamente os princípios básicos de construção destes Sistemas: o Mecanismo da Função Produção, o Princípio do Não-Custo e as Perdas nos Sistemas Produtivos.
O artigo busca evidenciar os principais aspectos envolvendo os três princípios colocados, evidenciando a importância significativa destes dentro do escopo geral dos Sistemas Produtivos com Estoque-Zero / STP. Por fim, os autores analisam os aspectos dinâmicos acerca das Perdas nos Sistemas Produtivos.
Palavras chave: MFP, Perdas, STP.
1. Introdução
Os Princípios básicos de construção de Sistemas de Produção com Estoque-Zero / Sistema Toyota de Produção – STP são: o Mecanismo da Função Produção – MFP, o Princípio do não-custo e as Perdas nos Sistemas Produtivos. Como esses temas são profundamente inter-relacionados eles serão apresentados de forma conjunta no presente artigo. As origens históricas dos princípios básicos de construção do STP encontram-se enraizadas nas obras teóricas de Shigeo Shingo e Taiichi Ohno. Por sua vez estas obras estão diretamente relacionadas com ações práticas efetivadas quando da construção do chamado STP que, inegavelmente, constituíram-se em um benchmark internacional dentro da “indústria que mudou o mundo” - a automobilística. O STP apresenta muitas variantes no Japão e é mais conhecido no ocidente, especialmente nos EUA, como Just-In-Time (uma visão restrita do STP) ou, mais recentemente, como Produção Enxuta.
O método de construção do STP não está completamente formalizado nos livros, embora uma leitura atenta e crítica da Parte 1, intitulada “Uma Abordagem Fundamental para a Melhoria da Produção” do livro “O Sistema Toyota de Produção - Do Ponto-de-Vista da Engenharia de Produção” (Shingo, 1996a), permita apresentar de forma concreta e didática o método de construção do esquema proposto. É o que os autores do presente trabalho pretendem explicitar nos itens que se seguem.
2. Aspectos Gerais que Constituem a Lógica de Construção dos Sistemas de Produção com Estoque Zero/STP
A lógica global de construção do esquema proposto parte da noção geral segundo a qual os Sistemas Produtivos podem ser analisados, compreendidos e construídos a partir de 3 etapas básicas, hierarquicamente seqüenciadas: i) Interpretação dos Sistemas Produtivos a partir de uma base analítica conceitual de construção destes Sistemas; ii) Construção dos Sistemas Produtivos levando em conta as condições sócio-econômicas de contorno nas quais estão inseridas as organizações em análise; iii) A criação e/ou utilização de técnicas convencionais que servirão para promover as melhorias concretas necessárias para a construção dos Sistemas Produtivos. Em uma primeira aproximação da utilização dos pressupostos acima expostos procurar-se-á analisar criticamente a lógica analítica de construção do STP. Para que isto possa ser feito utilizar-se-á basicamente a estrutura mostrada na Figura 1.
Figura 1 - Aspectos Básicos de Análise e de Construção do Sistema Toyota de Produção.
Inicialmente far-se-á uma discussão crítica do referencial analítico proposto por Shingo em 1945, intitulado de Mecanismo da Função Produção - MFP, isto será feito a partir do artigo “O Mecanismo da Função Produção: A Análise dos Sistemas Produtivos do Ponto-de-vista de uma Rede de Processos e Operações” (ANTUNES, 1994).
O ponto de partida para a compreensão do chamado MFP consiste em estabelecer uma clara diferenciação entre o que Shingo denomina de Função-Processo e Função-Operação. A Função-Processo consiste conceitualmente em observar o fluxo do objeto de trabalho (material, serviços ou mesmo idéias) no tempo e no espaço. A Função-Operação consiste, por outro lado, no acompanhamento do fluxo do sujeito do trabalho (Homens-Trabalho vivo; Máquinas-Trabalho morto) no tempo e no espaço. Portanto, segundo Shingo (1996a) todos os Sistemas Produtivos podem ser compreendidos como uma rede funcional de processos e operações, sendo assim o STP não se constituiria em uma exceção.
Este conceito é importante, precisamente porque ele promove um rompimento conceitual com a Administração da Produção de origem norte-americana representada por Taylor / Gilbreth’s / Ford. Por que este rompimento conceitual? Porque na tradição americana relativa à Administração da Produção os processos eram visualizados como um conjunto de operações. Sendo assim, as melhorias nas operações levariam imediatamente a melhorias no processo. Esta hipótese básica pode ser falseada. Por exemplo, ao comprar-se uma máquina para aumentar a capacidade em uma operação não gargalo, a operação está sendo melhorada (as máquinas foram melhoradas), porém o processo piorou porque o fluxo de materiais continua restringido pelo gargalo e os custos totais da fábrica aumentaram. Isto implicará no fato de que a Produtividade Econômica será reduzida.
Shingo (1996a) então responde de forma conclusiva à pergunta: “Quais melhorias são mais importantes e prioritárias: aquelas associadas à Função-Processo ou aquelas associadas à Função-Operação?” A resposta pragmática é que as melhorias que devem ser priorizadas nos Sistemas Produtivos devem estar associadas à Função-Processo. Ou seja, cria-se uma Administração da Produção no Japão, associada, inicialmente às práticas da Toyota, voltada diretamente para a melhoria da Função-Processo nos Sistemas Produtivos. Este autor ainda utiliza-se dos conceitos desenvolvidos pelos Gilbreth’s, porém sob um enfoque completamente novo, para propor um detalhamento dos processos. Estes processos são divididos em unidades pequenas (micro-unidades) de análise: a) Processamento: transformação dos materiais, caracterizado por mudanças na qualidade do objeto de trabalho; b) Inspeção: significa a comparação do objeto de trabalho contra um determinado padrão pré-estabelecido; c) Transporte: implica na modificação da posição ou de localização do objeto de trabalho; d) Estocagem ou Espera: nesta definição observa-se que o objeto de trabalho está em uma situação de espera (ou de estoque) sempre que ele não estiver sendo transportado, processado ou inspecionado.
O estudo das esperas é fundamental na lógica do STP, porque as esperas acarretam em uma série de conseqüências problemáticas na fábrica tais como: longos tempos de atravessamento e o aumento do nível de defeitos e retrabalhos. Desta forma, o processo de estocagem será subdividido, para fins de estudo, em 4 categorias: esperas do processo, espera do lote, espera ou estocagem de matérias-primas e espera ou estocagem dos produtos acabados. A discussão crítica destas esperas é importante para compreender o desenvolvimento histórico e teórico do STP.
Inicialmente é preciso esclarecer a diferença entre as esperas do lote e esperas do processo. A espera do processo implica que um lote inteiro está em situação de espera, enquanto o(s) lote(s) que se segue(m) está(ão) sendo processado(s), inspecionado(s) ou transportado(s). Ou seja, todo o lote está aguardando o(s) próximo(s) processo(s) ser(em) completado(s). A espera do lote relaciona-se com o fato de que uma dada peça do lote está sendo processada, inspecionada ou movimentada enquanto as demais peças do mesmo lote estão em condição de espera. O ataque sistemático às esperas do processo implica em técnicas geralmente associadas ao Planejamento e Controle da Produção – PCP de forma particular e à lógica de sincronização da produção de forma ampla. A melhoria das esperas do lote implica, de forma geral, na necessidade da utilização de ferramentas que modifiquem a realidade física da fábrica tais como: Troca Rápida de Ferramentas – TRF e o Leiaute Celular.
Enquanto a trajetória de desenvolvimento dos EUA no pós-guerra privilegiou as melhorias ligadas à espera do processo (por exemplo, via o desenvolvimento das ferramentas computacionais do tipo MRP/MRPII), os japoneses criaram técnicas que privilegiaram uma atuação conjunta na melhoria das esperas do lote (por exemplo, através do desenvolvimento do método da TRF) e das esperas do processo (por exemplo, o Kanban). Este fato é muito importante porque uma vez que na Toyota as técnicas de melhoria na espera do lote funcionaram bem na prática, a estrutura de PCP (ou seja, o tratamento da espera do processo) ficou muito facilitada. Ou seja, o caminho da eliminação sistemática da espera do lote implica em uma racionalização ampla do fluxo físico na fábrica o que facilita diretamente a montagem do fluxo de informações e, no futuro, via simplificação global de toda a fábrica, o processo de Automação global da mesma.
A existência de estoques de produtos acabados também deve ser claramente entendida. Por que existe a necessidade de constituição de produtos acabados na fábrica? A explicação relaciona-se com o estudo da relação entre o chamado Ciclo de Produção - P e o chamado intervalo admissível pelo comprador ou o chamado Ciclo de Entrega - E (Shingo, 1996a, 1996b). Por exemplo, supondo que o Ciclo de Produção de uma dada Fábrica A seja de 30 dias e o Ciclo de Entrega seja de 10 dias, torna-se inevitável a constituição de estoques ou não será possível atender a demanda dos clientes dentro do prazo estabelecido. Se o Ciclo de Produção desta fábrica for reduzido drasticamente para 5 dias, não haverá a necessidade de constituição de estoques de Produtos Acabados. Portanto, de forma genérica pode-se dizer que: i) Se P > E existirá a necessidade de constituição de Estoques de Produtos Acabados; ii) Se P < E não existirá a necessidade de constituição de Estoques de Produtos Acabados.
Sendo assim, duas alternativas são genericamente passíveis de serem utilizadas na prática, objetivando a eliminação dos Estoques de Produtos Acabados: a redução do Ciclo de Produção - P e o incremento do Ciclo de Entrega - E. Na prática atual do mercado, torna-se quase inviável (exceto no caso de empresas monopolistas) a segunda alternativa, uma vez que as dimensões competitivas tempo de atendimento e cumprimento dos prazos torna-se cada vez mais importante. O acirramento da competição, por outro lado, tem levado a uma situação onde os Ciclos de Entrega - E têm se tornado cada vez menores. A alternativa da Toyota constituiu-se exatamente em buscar radicalmente a alternativa de reduzir os Ciclos de Entrega de seus produtos. Porém de que dependem estes Ciclos de Entrega (ou tempos de atravessamento globais dos produtos)? Precisamente da existência das chamadas esperas do lote e das esperas do processo. De forma mais significativa, dado que com elevados tempos de preparação torna-se necessário uma produção em grandes lotes e, por conseqüência, os tempos de atravessamento serão altos. O ataque às esperas internas na fábrica torna-se então essenciais para a eliminação (ou minimização dos estoques) nas Empresas.
E quanto aos estoques de matérias-primas, assunto essencial para a Toyota devido a sua ampla política de desenvolvimento de fornecedores? Neste caso, o desenvolvimento do STP seguiu a mesma lógica da relação entre E e P. A Toyota adotou uma firme lógica de desenvolvimento de fornecedores adotando Ciclos de Entrega próximos de zero (E muito pequeno). Ou seja, adotando a lógica da entrega do tipo Just-In-Time. Para os fornecedores da Toyota duas alternativas genéricas tornaram-se possíveis: assumir o custo financeiro dos estoques de produtos acabados em suas fábricas devido ao fato que seus Ciclos de Produção - P eram maiores do que os Ciclos de Entrega - E propostos pela Toyota, ou trabalhar internamente na fábrica com o objetivo de reduzir seus Ciclos de Entrega - E. A segunda alternativa implicava no fornecedor atacar suas esperas do lote e do processo. Da mesma forma, os fornecedores diretos da Toyota negociaram com seus fornecedores e, assim, o desenvolvimento da cadeia produtiva foi ocorrendo desde um ponto-de-vista prático.
Já na análise da operação, Shingo adotou as proposições de Taylor que atacavam de forma geral esta problemática. As operações podem ser divididas em duas grandes linhas: as operações que se repetem regularmente e as operações que não se repetem regularmente. Entre as operações que se repetem regularmente encontram-se: a) Aquelas que se relacionam com a produção de uma única peça, ou seja, estão ligadas à produtividade horária da máquina (alimentação/desalimentação de matérias primas, ligar/desligar máquinas, operação propriamente dita); b) Aquelas que se relacionam com a produção de um lote (a lógica do Tempo de Preparação). É preciso observar que as operações que se repetem regularmente podem ser padronizadas e calculadas. Entre as operações que não se repetem regularmente encontram-se: a) Folgas ligadas ao pessoal (folgas físicas e higiênicas); b) Folgas não ligadas ao pessoal (por exemplo, lubrificação, parada de máquinas, etc.). Estas operações podem ser calculadas, por exemplo, via a utilização de procedimentos estatísticos, mas não podem ser padronizadas. De outra parte, toda a lógica da disciplina ergonomia, ou seja, a análise da relação homem/máquina, será discutido de um ponto-de-vista sistêmico no STP a partir da Função-Operação.
De forma sucinta pode-se dizer que o MFP: a) Constitui-se em um elemento invariante de análise dado que todas as produções podem ser compreendidas como uma rede funcional de processos e operações (Shingo, 1996a); b) Deixa claro que os Administradores de Produção devem privilegiar as melhorias baseadas na Função-Processo. Muitos anos depois, importantes Teorias, Princípios e Técnicas vão respaldar esta proposição como, por exemplo, a Teoria das Restrições e a Reengenharia de Negócios e de Processos; c) Os Princípios e Técnicas utilizados (já existentes) e/ou desenvolvidos no STP tiveram caráter dedutivo a partir da ótica global expressa no MFP, visando fundamentalmente responder às necessidades de melhorias na Função-Processo. Isto explica a necessidade de Shingo criar o sistema SMED (Single Minute Exchange of Die and Tools) para reduzir os tempos de preparação e o Controle de Qualidade Zero-Defeitos e de Ohno desenvolver o Sistema Kanban e utilizar de forma ampla o Princípio da Autonomação; d) A definição das
Perdas a serem atacadas visando debelar os custos desnecessários à produção estão diretamente relacionados com a ótica do MFP.
Um segundo tópico a ser analisado para compreender o esquema geral do STP, consiste em compreender a lógica das Perdas nos Sistemas de Produção. Para isto será usado o artigo “A Lógica das Perdas nos Sistemas Produtivos - Uma Análise Crítica” (ANTUNES, 1995). Tudo parte da compreensão das normas de concorrência. Antes da crise do petróleo pode-se dizer que (SHINGO, 1996a, 1996b; OHNO, 1997): Preço de Venda = Custo de Produção + Lucro. A partir da crise do petróleo a equação inverteu-se e, então pode se dizer que (SHINGO, 1996a; OHNO, 1997): Lucro = Preço de Venda – Custo de Produção.
Na formulação econômica proposta acima alguns tópicos devem ser ressaltados: a) Os preços de venda passam a ser fortemente influenciados pelo mercado, não sendo determinados pelas Empresas a partir de seus custos (formação do preço de venda). Conforme Ohno (1997) é o mercado quem decide os preços de venda. Segundo Shingo, “é o mercado (o consumidor) quem sempre determina o preço de venda adequado” (SHINGO, 1996a, p. 109); b) Segundo Shingo (1996a, p. 109) o aumento dos lucros “...só pode ser feito pela redução dos custos”.
A partir das constatações anteriores Shingo (1996a) deixa claro que a construção do STP deve ser pensado teoricamente dentro da lógica do Princípio do Não-Custo. Para entender o Princípio do Não-Custo, torna-se necessário definir com clareza: a) a relação de custo entre os fatores de produção quando da construção do modelo STP; b) o significado do trabalho e das Perdas dentro da lógica do STP; c) a relação entre os custos e as Perdas dentro do modelo.
Quando do processo histórico de construção do STP o custo-horário do fator trabalho era, em média na indústria automobilística japonesa, 3 a 5 vezes maior do que o custo-horário das máquinas (SHINGO, 1996a). Portanto, tornou-se necessário aos precursores do modelo traduzir a linguagem econômica da relação entre os fatores de produção em uma linguagem tecnológica compatível com a realidade industrial japonesa.
Esta tradução da problemática econômica feita por Ohno passa pela concepção do significado do trabalho dentro das indústrias. Mais especificamente, Ohno demonstra uma preocupação teórica em definir o movimento realizado pelos trabalhadores dentro das unidades de produção. Ohno (1997) vai propor uma divisão do movimento dos trabalhadores em três partes: trabalho líquido, trabalho que não adiciona valor, mas suporta o trabalho efetivo e as Perdas. O trabalho líquido ou trabalho efetivo corresponde àquelas parcelas das atividades que geram custos, porém adicionam valor ao produto. Esta parcela corresponde ao que Macedo (1992) denomina, metaforicamente, de custos sadios. Como exemplos destas atividades tem-se: fresagem, usinagem, montagem, pintura, atendimento direto ao cliente, pesquisa e desenvolvimento, etc. O trabalho que não adiciona valor, mas é necessário para a execução da produção durante um certo período dado ou trabalho adicional constitui-se fundamentalmente em um trabalho de suporte à produção, gera custos, porém não agregam diretamente valor ao produto. No momento de tempo considerado estes trabalhos também se constituem em custos sadios. Como exemplo pode-se citar: acionar o botão para dar partida a uma máquina, algum tempo (muito reduzido - menor do que 10 minutos) de Setup, alguma movimentação de materiais, a supervisão do processo produtivo, etc. As Perdas constituem-se em atividades que geram custo e não adicionam nenhum valor ao produto. Portanto, devem ser eliminadas imediatamente. Esta parcela de custos corresponde ao que metaforicamente Macedo (1992) chama de custos doentes. Como exemplo pode-se citar: produção de refugos e retrabalhos, esperas, transportes desnecessários, estocagem de material em processo e produto acabado, inspeção, etc.
O objetivo (Princípio do Não-Custo) do STP pode ser caracterizado como: a) Eliminação completa das Perdas; b) Minimização do trabalho adicional e, no longo prazo, sua possível eliminação; c) Aumento da densidade do trabalho humano, ou seja, aumentar o percentual do tempo que os trabalhadores realizam tarefas que agregam valor relativamente ao tempo total onde permanecem na fábrica. Isto não implica em trabalhar mais tempo, dado que o período global de trabalho permanece o mesmo ou em muitos casos se reduz, mas sim em melhorar a qualidade do trabalho do ponto-de-vista do desempenho econômico-financeiro da Empresa.
Um maior detalhamento das Perdas foi proposto conjuntamente por Ohno (1997) e Shingo (1996a). Trata-se da noção de 7 Perdas. Elas estão diretamente relacionadas com o conceito do MFP. Estas Perdas são: a) Perdas por superprodução (quantitativa e por antecipação); b) Perdas por transporte; c) Perdas no processamento em si; d) Perdas devido à fabricação de produtos defeituosos; e) Perdas nos estoques; f) Perdas no movimento; g) Perdas por espera. As 5 primeiras Perdas relacionam-se com a Função-Processo na medida em que visam racionalizar o fluxo do objeto de trabalho no tempo e no espaço. As 2 últimas (movimento e espera) relacionam-se diretamente com a Função-Operação em função do fato de estarem focadas na análise do sujeito do trabalho (pessoas e equipamentos).
Porém, resta responder objetivamente a pergunta “qual a relação entre Custos e Perdas no modelo de forma mais ampla?” A resposta consiste no fato de que o conceito de Perdas surge precisamente para reduzir sistematicamente os custos do sistema. Isto é importante compreender para verificar a possibilidade de “abrir”, ou seja, usar o modelo em outras circunstâncias históricas onde, por exemplo, as condições sócio-econômicas são objetivamente diferentes. No período de Ohno, a preocupação central era com a mínima utilização da força de trabalho. A explicação é que os custos do fator-trabalho eram muito relevantes quando comparados com o fator custo-horário das máquinas. Hoje, alguns custos relevantes não são explicitamente levados em conta quando confrontados com o modelo histórico tradicional do STP. Por exemplo: a) Custos relativos à questão do meio-ambiente (por exemplo, resíduos sólidos, líquidos, gasosos, etc.); b) Custos relativos aos acidentes de trabalho; c) Custos relacionados com a incorreta utilização da energia (por exemplo, Perdas térmicas decorrentes do uso inadequado de isolamento térmico, dos purgadores de vapor, Perdas elétricas identificadas a partir da medida do baixo fator de potência das indústrias, etc.).
Portanto, as Perdas correspondentes a estes custos não são consideradas no STP em sua forma histórica tradicional. De um ponto-de-vista da hipótese geral pode-se dizer que os custos são a causa, as Perdas a conseqüência. Metaforicamente pode-se postular que todos os fatos e dados que não constam nos “autos do processo” (por exemplo, os custos ligados ao meio-ambiente) “não existem”, ou seja, não serão “enxergados” como Perdas. Desta forma, se a eliminação dos “custos doentes” relacionados acima é relevante do ponto-de-vista econômico/social, então se torna necessário ampliar a noção das 7 Perdas criando, por exemplo, “Perdas relativas ao meio-ambiente”, “Perdas ergonômicas”, “Perdas energéticas”, etc. Aparentemente, desde um ponto-de-vista da disciplina Administração da Produção, as Perdas nada mais são do que a transmissão da linguagem dos custos, mais especificamente dos “custos doentes”, para a linguagem técnica do dia-a-dia do chão-de-fábrica.
Da perspectiva da literatura ocidental, a ênfase sobre a noção de Perdas recai sobre uma ótica mais geral que salienta o conceito geral, segundo o qual as Perdas são atividades que geram custo e não adicionam valor ao produto. A discussão sobre as 7 Perdas e sobre uma conceituação mais ampla de Perdas é reduzida. Uma das exceções é o trabalho escrito por Robinson & Schroeder (1992), onde os autores estabelecem uma ampla discussão sobre o significado das Perdas nos Sistemas de Produção. Partem do conceito de Shingo segundo o qual “a maior das Perdas é a Perda que nós não vemos” (SHINGO, 1987, p. 18). Postulam que “detectar e eliminar as Perdas invisíveis tornou-se a mais importante tarefa do gerente de produção” (ROBINSON & SCHROEDER, 1992, p. 37). Os autores sugerem 4 Princípios gerais para eliminar as Perdas invisíveis nos Sistemas Produtivos: a) Quando da avaliação ou da aplicação de uma nova técnica de gerenciamento, identificar as fontes de Perdas que serão expostas ou eliminadas, aquelas que não ficarão expostas nem serão eliminadas, aquelas que serão criadas, e as técnicas necessárias para suprir as limitações das técnicas que serão utilizadas; b) Não limitar o treinamento de pessoal ao desenvolvimento de métodos específicos de trabalho, na medida em que os empregados também devem aprender os pressupostos gerais necessários para a elaboração de melhorias em suas respectivas áreas de atuação; c) aumentar o número de perspectivas e prismas (visões) a partir da qual os processos são geralmente observados; d) Quando são feitas mudanças significativas em qualquer componente, o processo como um todo deve ser reexaminado para verificar as eventuais novas Perdas que possam ter sido introduzidas no sistema. Os autores concluem sugerindo que os gerentes de produção se preocupem em detectar as Perdas invisíveis nos Sistemas de Produção para posteriormente eliminá-las (ROBINSON & SCHROEDER, 1992).
Um último ponto a ressaltar é que, na realidade prática, as Perdas nos Sistemas Produtivos são inter-relacionadas. Ou seja, a realidade das Perdas é dinâmica. Assim, os autores deste trabalho propõem que sejam observadas duas lógicas gerais nesta dinâmica das Perdas: a dinâmica positiva das Perdas e a dinâmica negativa das Perdas. No caso da dinâmica positiva das Perdas, um determinado tipo de ação de melhorias debela ou minimiza simultaneamente duas ou mais Perdas. Por exemplo, ao reduzir-se a troca de ferramentas de uma dada fábrica de móveis de 25 para 6 minutos houve uma redução dos refugos em 70% (refugo gerado durante a troca de ferramentas). Neste caso, minimizam-se as seguintes Perdas associadas ao fenômeno: por superprodução quantitativa, por fabricação de produtos defeituosos, por espera e no movimento. No caso da dinâmica negativa das Perdas, determinado(s) tipo(s) de Perdas são debelados ou minimizados, porém surgem outras adicionais, que não existiam antes das melhorias. Por exemplo, ao melhorar a produtividade Taylorista (produção/hora) de uma dada máquina, esta fica mais exigida do ponto-de-vista da manutenção e acaba aumentando o número de quebras. Neste caso diminuíram as Perdas por processamento em si, porém as Perdas por espera devido à manutenção tendem a aumentar. No caso da dinâmica negativa das Perdas torna-se necessário tomar precauções para enxergar o problema de forma holística.
3. Síntese das Discussões sobre a Lógica de Construção do STP/Sistemas de Produção com Estoque-Zero
A partir das discussões apresentadas anteriormente, pode-se dizer que a lógica de construção do STP pode ser visualizada de forma abrangente da seguinte forma: a) MFP / Função-Processo e Função-Operação - Invariante do Sistema, ou seja, não se altera se houverem modificações nas condições sócio-econômicas; b) Definição dos Custos a serem eliminados ou minimizados - varia de acordo com as condições de relação da Empresa com o ambiente no tempo. Por exemplo, certos custos ambientais existentes na década de 90 não eram computados na década de 70; c) Perdas a serem atacadas – é função dos custos definidos no item anterior. As Perdas são a transmissão do mundo econômico dos custos para a realidade da fábrica; d) Técnicas específicas que relacionam a Função-Processo / Função-Operação com as Perdas a serem eliminadas ou minimizadas.
O STP representa, de forma geral, a articulação conceitual das Técnicas e Princípios que foram utilizados para debelar as chamadas 7 Perdas. Estas Técnicas e Princípios são: leiaute e fabricação de peças em fluxo unitário, Operação-Padrão, Troca Rápida de Ferramentas - Single Minute Exchange of Die and Tools, Sincronização (Kanban), Inspeção na fonte e Poka-Yoke, Engenharia e Análise de Valor. Estas Técnicas foram articuladas em uma relação de causa-efeito-causa, gerando o chamado STP.
4. Considerações Finais
A partir do desenvolvimento do presente trabalho, pode se analisar criticamente os princípios pelos quais são construídos os Sistemas de Produção com Estoque-Zero / STP. Os princípios básicos de construção são: o MFP, o Princípio do Não-custo e as Perdas nos Sistemas Produtivos. Cabe ressaltar a forma de abordagem dos autores em relação aos Sistemas Produtivos, buscando analisar aspectos relacionados com: i) Sistemas Produtivos a partir de uma base analítica conceitual; ii) Sistemas Produtivos levando em conta as condições sócio-econômicas de contorno; iii) A criação e utilização de técnicas convencionais. Desta maneira, os autores buscaram cobrir os principais aspectos envolvidos com a análise dos Sistemas Produtivos.
Por fim, outro aspecto relevante diz respeito ao tratamento das Perdas nos Sistemas Produtivos como uma realidade dinâmica, na qual está inserida duas lógicas gerais: a dinâmica positiva das Perdas e a dinâmica negativa das Perdas. Ou seja, os autores evidenciam as conseqüências positivas e negativas das melhorias despendidas sobre as Perdas nos Sistemas Produtivos.
Referências
ANTUNES, J. A. V. (1994) – O Mecanismo da Função da Produção: a Análise dos Sistemas Produtivos do ponto-de-vista de uma Rede de Processos e Operações. Revista da Produção, Porto Alegre, v. 4, n. 1, p. 33-46.
ANTUNES, J. A. V. (1995) – A Lógica das Perdas nos Sistemas de Produção - Uma Análise Crítica. Anais do XIX Encontro da Associação Nacional de Programas de Pós-Graduação em Administração, João Pessoa, v. I, n. 7, p. 357- 371.
MACEDO, L. M. (1992) – Sistema de Produção com Inventário Minimizado: Abordagem Técnico-Financeiro. Editora do IMAM, São Paulo.
OHNO, Taiichi. (1997) – O Sistema Toyota de Produção – Além da produção em larga escala. Editora Bookman. Porto Alegre.
ROBINSON, A. G. & SCHROEDER, D. M. (1992) – Detecting and Eliminating Invisible Waste. Production and Inventory Management Journal, Fourth Quarter, p. 37-42.
SHINGO, Shigeo. (1996a) – O Sistema Toyota de Produção – Do ponto de vista da engenhara de produção. Editora Bookman. Porto Alegre.
SHINGO, Shigeo. (1996b) – Sistemas de Produção com Estoque Zero: O Sistema Shingo para Melhorias Contínuas. Porto Alegre: Bookman.