Aplicativo para o Cálculo das Necessidades de Materiais para Pequenas Empresas
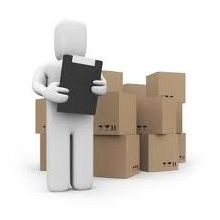
Por: Admin - 24 de Novembro de 2014
Autores:
Marcelo Klippel (UNISINOS) marcelo@klippel.com.br
Ricardo Brandão Mansilha (UNISINOS) rmansilha@terra.com.br
Resumo
O presente artigo tem por objetivo apresentar o desenvolvimento de um aplicativo para o cálculo das necessidades dos materiais para empresas de pequeno porte, baseado em planilhas eletrônicas. O desenvolvimento do protótipo se deu pela necessidade de aperfeiçoamento na área de gestão de estoques de pequenas empresas, mas com o objetivo maior em servir de modelo na construção de aplicativos de baixo custo para empresas de pequeno porte.
Como resultado, para a construção do aplicativo foi de suma importância os principais conceitos, obtidos pela revisão bibliográfica, os dados levantados, bem como, a validação do protótipo através de testes de simulações. Os autores buscam conceituar e apontar as principais atividades que se inter-relacionam com o cálculo de necessidade dos materiais.
Palavras chave: Materiais, MRP, Gestão.
1. Introdução
A partir da revolução industrial, diversas organizações começaram a crescer e a expandir seus produtos para o mundo todo. Estas organizações tornaram-se ainda maiores com o passar dos anos e as atividades de gestão dos materiais, itens e componentes necessários para a produção, foram tornando-se cada vez mais complexos. Com a chegada dos computadores, as empresas de médio e grande porte solucionaram seus problemas, pois a capacidade de armazenamento de dados e a praticidade da efetuação de cálculos matemáticos foram adaptadas e implementadas nestas empresas. Porém o alto custo de aquisição de computadores durante um longo período forçou as pequenas empresas a continuarem a resolverem seus problemas administrativos manualmente.
Com o advento da era da informática, os computadores encontram-se disponíveis na maioria das empresas de pequeno porte, mas a falta de organização dos dados e os problemas matemáticos persistem devido à dificuldade da programação destas máquinas e pela falta de conhecimentos administrativos. Estas dificuldades refletem na construção de modelos que auxiliariam na obtenção de informações referentes a determinadas áreas e setores da administração. Softwares especializados encontram-se no mercado e tem como proposta a resolução dos problemas existentes mencionados acima. Entretanto, grande parte das pequenas empresas ainda de depara com grandes dificuldades para a aquisição destes softwares, principalmente devido ao seu alto custo. Sendo assim, estas empresas acabam buscando meios para a resolução de seus problemas, utilizando antiquados métodos administrativos.
A proposta de desenvolvimento de aplicativos através do uso de planilhas eletrônicas sugere uma infinidade de modelos de cálculos possíveis que se enquadram a diversos grupos de informações, isto implica saber as necessidades das empresas para a construção de protótipos específicos que resolvam seus problemas.
O cálculo das necessidades de materiais é um modelo que permite auxiliar na gestão dos estoques das empresas, mas a obtenção de softwares especializados nesta área ainda hoje é inviável para as empresas de pequeno porte devido ao seu alto custo, podendo acarretar em grandes problemas de gestão, gerado pelo excesso ou pela falta de matéria-prima e insumos. Como solução as empresas caminham na tentativa de elaborar seus próprios meios de controle, mas acabam encontrando como barreira o desenvolver de um aplicativo computacional por não existir no mercado modelos de construção de protótipos a baixo custo.
A presente pesquisa terá como linha mestra o desenvolvimento de um aplicativo para a gestão de materiais baseado na teoria do MRP – Planejamento das Necessidades de Materiais (Material Requirement Planning) e estruturado em planilhas eletrônicas do Microsoft Excel.
2. Referencial Teórico
Segundo Slack (1997), o MRP - Material Requirements Planning – original data dos anos 60, implica que as empresas calculem o número de materiais necessários e o momento da utilização de cada item. Para calcular, o MRP utiliza os pedidos em carteira como previsão para o número de itens a serem fabricados. Verificam-se, então, todos os componentes que são necessários à produção para preencher a previsão, e garantir o prazo de entrega.
Conforme Moreira (2000), o MRP é uma técnica para converter a previsão de demanda de um item de demanda independente em uma programação das necessidades das partes dependentes do mesmo. O MRP pode ser visto também como um sistema de controle de estoques de itens de demanda dependente, e neste sentido, o cálculo de necessidades dos materiais é um sistema pró-ativo, dado que evita a manutenção de estoques, a não ser aqueles destinados a eventualidades. Para Slack (1997), o MRP é um sistema que ajuda as empresas a calcular o volume e tempos similares a esses, quando existe um grau elevado na complexidade do número existente de itens. Até os anos 60 eram calculadas manualmente estas operações, garantindo os materiais certos no momento certo. Entretanto, com a chegada dos computadores, surgiu a oportunidade e a capacidade da execução destes cálculos detalhados e demorados, com o auxílio dos mesmos de forma rápida e relativamente fácil.
Moreira (2000) ainda afirma que as quantidades dos componentes, necessários à produção, são adquiridas apenas numa data através de revisões periódicas, ou por uma quantidade remanescente, ou seja, por um sistema de revisão contínua. Estes sistemas são reativos, e exigem a manutenção permanente de estoques.
Para Slack (1997), a estrutura do produto mostra certos itens e formam outros, e que estes podem formar terceiros. Corrêa (2001) chama, no jargão do MRP, de itens "filhos" os componentes diretos de outros itens, estes obviamente chamados itens "pais" de seus componentes diretos. Slack (1997) afirma que para poder fabricar um produto qualquer, a empresa precisa saber quais os componentes a serem utilizados para conclusão do mesmo. Caso ela decida utilizar um sistema MRP para realizar esta tarefa, ela necessita de arquivos armazenados em unidades computacionais com os componentes de cada item relacionado a etapas de montagem. Conforme o autor esses arquivos são denominados de Listas de Materiais. De acordo com Arnold (1999), existem três pontos importantes para se chegar a uma lista de materiais. O primeiro ponto é que a lista deva trazer consigo todas as informações sobre peças necessárias para a fabricação de um determinado produto. No segundo ponto, o autor explica que cada peça ou item deve possuir apenas um número para cadastro, padronizando a peça, junto à estrutura do produto. Por terceiro, compreende-se que cada peça é definida por sua forma, ajustamento ou função.
Em termos de estrutura de planejamento do MRP, para a execução dos cálculos de quantidade e tempo envolvidos no planejamento das necessidades de materiais é normalmente requerido que as empresas mantenham dados em arquivos de fácil visualização e atualização. Ou seja, para que se possa compreender a complexidade deste sistema se faz necessário entender os registros apresentados e o uso devido de softwares especializados. De acordo com Moreira (2000), fica fácil distinguir os insumos fundamentais, sem os quais o sistema MRP não pode operar. A partir da programação de produtos finais, é determinada a programação da compra, fabricação ou montagem das partes que compõe o produto final.
Segundo Slack (1997), as primeiras entradas para o cálculo de necessidades de materiais são os pedidos de clientes e a previsão da demanda. Para o autor a carteira de pedidos refere-se a pedidos firmes programados para um determinado tempo, enquanto que a previsão consiste apenas em estimativas realísticas da quantidade e tempo de pedidos futuros. O MRP é executado com base na combinação das duas componentes de demanda citadas anteriormente. Todas as demais etapas são derivadas e dependentes desta demanda. E através disto argumenta-se que o MRP é um sistema de demanda dependente que no qual esta demanda é aquela derivada de decisões tomadas na empresa, enquanto que o sistema independente é adequado para os casos em que a demanda está fora de controle da empresa.
Para Arnold (1999), o MPS é um plano para a produção que reflete as necessidades da demanda e a capacidade produtiva, formando um plano de prioridades para ser seguido pela produção. O MPS estabelece quais produtos serão produzidos e em que datas, portanto, é fundamental para que o MRP possa determinar quanto de cada parte ou componente deve ser adquirido e quando programar a produção.
Segundo Slack (1997), o programa-mestre de produção (MPS - Master Production Schedule), é a etapa mais importante do planejamento e controle de uma empresa, constituindo-se na principal entrada para o planejamento das necessidades de materiais. Na manufatura, o MPS declara a quantidade e o momento em que os produtos finais devem ser produzidos, direcionando toda a operação em termos de montagem, manufatura e compras. É a base do planejamento da mão-de-obra e maquinários.
Para Arnold (1999), que o MPS forma uma base para que a produção determine o que deve ser produzido. Trata-se de um instrumento de comunicação e base para alterações relacionadas a mudanças na demanda e capacidade da produção.
Um insumo básico para o sistema de MRP é conhecer seu estoque, pois quando é feito cálculos para identificar o necessário, as quantidades disponíveis devem ser consideradas. De acordo com o mesmo existem dois tipos de informações necessários. O primeiro é chamado de fatores de planejamento e inclui dados de quantidades de pedido, lead times e estoque de segurança.
Essas informações não se modificam com freqüência, embora seja necessário planejar quando e quanto encomendar, para que as entregas sejam feitas a tempo de trabalhar o produto e cumprir o prazo com o cliente. Conforme Arnold (1999), o segundo tipo de informação de que se necessita é o status de cada item. O sistema de MRP precisa saber quanto está alocado em estoque e quanto está disponível para demandas futuras. Esse tipo de informação mostra-se dinâmico e é modificado em cada transação.
Para Slack (1997), o MRP é um processo sistemático de tomar todas as informações anteriormente escritas de planejamento e calcular a quantidade e o momento das necessidades que irão satisfazer à demanda. Ainda, o MRP recebe as informações do MPS em relação a cada produto final e "explode" este programa através da lista de materiais, verificando quantas sub-montagens e itens são necessários à produção. Segundo o autor, antes de descer para o nível um da estrutura do produto, o MRP analisa quantos produtos acabados existem no estoque. Gera então, as ’’ordens de produção", requisições para as necessidades líquidas dos itens que serão feitos na empresa. Essas necessidades formam o programa que será explodido através da lista de materiais para o próximo nível abaixo na estrutura. Novamente o estoque disponível dos itens deste novo nível é verificado, novas ordens de trabalho são gerados, como também as respectivas ordens de compra conforme a ausência no estoque. Este processo é de forma contínua até que se chegue ao nível mais baixo da estrutura do produto.
A lista de materiais fornece ao MRP, a base de dados dos componentes ou estrutura do produto para a fabricação. Em vez de tomar esses componentes e simplesmente multiplicá-los pela demanda, de modo a determinar as necessidades totais de materiais, o MRP reconhece que alguns dos itens necessários podem estar disponíveis em estoque, podendo ser este estoque na forma de produtos acabados, intermediários ou mesmo de matéria-prima. É então necessário, começar a análise do estoque pelo nível zero, seguir pelos próximos níveis, para que se possa calcular o que é denominado de necessidade "líquida", ou seja, a quantidade extra necessária para, juntamente com o estoque, atender à demanda. Enfim para fazer isto, o MRP requer que sejam mantidos registros de estoque.
De acordo com Moreira (2000), "a dinâmica de processamento no MRP parte da quantidade desejada de um produto final numa data especificada, informações essas fornecidas pelo "Plano Mestre de Produção". A "partir destas informações, é feito a "explosão" do produto acabado nas necessidades dos itens, com seus devidos tempos de disponibilidade.
3. O Desenvolvimento do Aplicativo para o Cálculo das Necessidades de Materiais para Pequenas Empresas
O aplicativo computacional desenvolvido trata-se do método utilizado pelas empresas para o cálculo de necessidades dos materiais. O desenvolvimento deste aplicativo tem como objetivo maior exemplificar e demonstrar a criação do protótipo, podendo assim, servir como benefício para outras empresas de pequeno porte na elaboração de seus próprios aplicativos que estejam relacionados ao problema de gestão de estoques.
Os dados básicos de entrada são os dados iniciais que devem estar contidos no sistema para que possam ser efetuadas simulações posteriormente. A entrada destes dados se dá através do conjunto de seis planilhas, que são preenchidas com informações referentes aos tempos, matéria-prima e custos da empresa. Estas informações servem para definir as condições e restrições da empresa no momento da simulação e informar as demais planilhas para o efeito de cálculos e análises. A seguir seguem as explicações acerca do desenvolvimento destas planilhas.
A Lista de Materiais é considerado o conjunto de informações prioritárias para o desencadeamento do aplicativo. Nesta primeira planilha são encontradas as informações básicas em relação aos custos de cada material, trazendo como variável apenas os valores de matéria-prima e o controle através de datas de atualização. A Figura 1 apresenta a primeira tela do aplicativo:
Figura 1 - Exemplo Parcial da Planilha Lista de Materiais
A planilha lista de materiais foi construída levando-se em consideração questões tais como: i) Especificação do Material; ii) Unidade do Material; iii) Preços Unitários de cada Material.
Com a definição da lista de materiais é preciso estruturar cada produto, com a finalidade de entender as quantidades de materiais que constituem cada um deles. É inserido ao sistema então, a segunda entrada de dados, que diz respeito às quantidades necessárias de materiais para cada produto. Nesta planilha, são listados os materiais da planilha Lista de Materiais, dando prioridade aos itens mais caros referentes à classe A e B. Os dados de entrada são inseridos através de outras colunas denominadas por números que se referem a determinados produtos, sendo suas colunas preenchidas com as informações de necessidade de materiais únicas de cada item para cada tipo de produto.
Os dados de entrada da planilha Tempos de Processo (TP), referem-se principalmente aos espaços de tempo requeridos por cada processo para a produção de cada item. A unidade destes tempos segue a exigência específica de cada empresa. Além de informar os tempos de cada processo, é preciso colocar as informações relativas a "carga de horas diária" e o "número de dias úteis do mês" nas respectivas linhas, onde são dadas como restrições para a capacidade da empresa.
Uma outra planilha consiste na planilha Lead Time de Compras (LTC). As informações contidas nesta planilha são de extrema importância para o planejamento de compras. Os dados inseridos nesta planilha estão relacionados com o tempo existente entre a colocação de um pedido e a entrega do mesmo.
Na seqüência, toma-se a Planilha Quantidades em Estoques (QE), que tem como entrada de dados informações sobre as quantidades existentes de matéria-prima e componentes na empresa que não estão comprometidos com produtos já vendidos.
Os dados revelados por estas quantidades, precisam ser atualizados sempre que existir um novo planejamento. Os cálculos efetuados nesta planilha aparecem apenas em relação ao capital investido em estoque, ou seja, são multiplicados os valores unitários contidos na planilha Lista de Materiais pelas quantidades existentes em estoque. Os dados de entrada desta planilha devem ser atualizados constantemente ou sempre que existir a necessidade de uma simulação, devido à alta rotatividade dos dados apurados pelas entradas e saídas de estoque.
Os estoques de segurança são definidos para precaver futuras falhas no processo. A falta de estoque pode acarretar em prejuízos para as empresas, então uma taxa de segurança é sugerida para que haja uma proteção contra a quebra de rotina nos processos.
A planilha ES primeiramente recebe os dados de "lead times de compras" (tempo entre o pedido e a entrega) e a "necessidades bruta" (quantidade de material necessário para a fabricação de todo o lote simulado) de cada matéria-prima estipulada pela empresa. A seguir calcula-se o "uso diário de material", dividindo a "necessidade bruta" pelo lead time do processo que irá trabalhar a matéria-prima. Encontra-se a "quantidade de materiais gasta durante o lead time de compras", multiplicando o uso diário pelo lead time de compras e enfim revela-se o "estoque de segurança" a ser utilizado, multiplicando a quantidade gasta durante o lead time, pela taxa sugerida para o planejamento.
Respondendo as informações básicas, com o objetivo de alcançar as respostas do MRP, torna-se possível calcular quando é preciso produzir ou comprar. O conjunto de planilhas para o cálculo das necessidades de tempo gera novos dados e informações que permitem, através da simulação, resolver os problemas de quando comprar, quando produzir e assinalar quando há falta de capacidade de produção. Para estas planilhas seguem as explicações abaixo.
No momento em que se dão os dados da planilha TP, o cálculo de capacidade é efetuado automaticamente. Em primeiro plano é encontrado o produto da carga de horas diária e multiplicado pelo número de dias úteis existentes no mês em que será efetivada a produção. Tendo encontrado o produto desta multiplicação, este mesmo número, é inserido por toda coluna Horas Mensais (HM) da Tabela Itens de Produção contida na planilha Cálculo de Capacidade (CC), então este valor é multiplicado mais uma vez por cada número de Processo, dados da Coluna "NP", informando o número de horas totais (HT) disponíveis a serem trabalhadas, para cada "item de processo".
Em segundo plano, são convertidos os tempos de cada processo registrados na planilha TP em Horas e multiplicado pela previsão de demanda de cada produto, revelando os cálculos de horas necessárias para a produção, relativo às unidades (RU) e relativo aos lotes simulados pela previsão da demanda (RL). Por terceiro, é constituída a tabela de lead time de Produção, onde é revelado os totais de horas necessárias para a produção do lote e o número de dias necessário para a passagem de todos os produtos por cada processo. E como complemento é dado o total de horas de sobra ou sobrecarga na coluna HD (horas disponíveis), subtraindo-se o número de horas necessárias para a produção, pelo número de horas disponíveis de processo.
A planilha Lead Time de Produção e de Compras (LPC) reúne todos os tempos de fornecedores e de processos, existentes na empresa facilitando a visualização. As informações atribuídas são vinculadas das planilhas Lead Time de Compras (LTC) e cálculo de capacidades (CC). Com os dados atualizados dos Lead Time relativo as compras e processos, torna-se possível voltar no tempo a partir de uma data específica de entrega, somando esses tempos. Após determinar quais os itens e seus respectivos níveis que merecem aparecer na árvore do produto, é preciso buscar as informações da planilha LPC. Com exceção do primeiro nível que representa o lead time da montagem final, as informações devem ser iguais aos dados de lead times da planilha LPC, mas somados ao tempo do nível superior. A planilha Cálculo do Sequenciamento das Ordens, é responsável por informar a planilha do Cálculo do Lote Disponível, quantos dias é preciso voltar no tempo para o início de um determinado processo.
Quando é definida a data de planejamento através da planilha de simulação, O cálculo do lead time total de produção se encarrega de buscar estas informações e “jogá-las” no tempo definindo automaticamente quando o lote se encontrará disponível pela empresa. Sendo assim basta acrescentar o tempo de entrega do produto, que no caso depende das distâncias das regiões envolvidas, para o futuro desembarque.
Ao interpretar as restrições existentes de tempo, é preciso separar os dias úteis dos dias não produtivos. Sendo assim a planilha CDM busca a data em que o lote estará a dispor, calculado pela planilha CLT e distribui no tempo destacando os finais de semana, e guardando os dias que realmente são de interesse para o MRP. Após a distribuição dos dados, três colunas isoladas informam ao processo, o número de dias que é preciso voltar no tempo, para que ocorra o início de cada processo. As datas de emissão são encontradas aplicando-se uma fórmula de condição que compara os tempos ditados pelo cálculo do sequenciamento das ordens (CSO), com os números distribuídos nesta planilha, relacionando os tempos de início de processo com as datas do calendário. Destacando os dias em que não ocorre produção. Para a disposição das datas desta planilha, é buscado o dia em que o lote torna-se disponível calculado pela planilha anterior e aplicado uma fórmula de subtração simples.
Conjuntamente ao cálculo das necessidades de tempo, o MRP faz necessário o cálculo das necessidades líquidas de materiais, onde é informado o quanto é necessário comprar. E para concluir esta necessidade é preciso buscar informações através da lista de materiais (LM) e quantidade de materiais (QM), formando novas planilhas que possibilitem efetuar este cálculo.
Após obter as informações de necessidades de materiais e seus relativos custos, as planilhas que compõe a Necessidade Bruta (NBM e NBT) buscam na planilha Plano Mestre (PM), a demanda projetada e então é multiplicado a estes dados as quantidades unitárias e custos relativos, formando a necessidade bruta do lote simulado.
Os primeiros dados oferecidos pelas planilhas anteriores informam ao cálculo das necessidades líquidas, o número exato das quantidades de materiais precisos para a fabricação de todo o lote a ser produzido. Sendo assim, são inevitáveis a subtração dos itens existentes em estoque e a introdução de um montante em estoque que possa assegurar possíveis falhas de processo.
Nesta planilha são calculados os custos e as quantidades de materiais necessárias para atender a produção.
Na planilha NL primeiramente é desenvolvido um espaço para colocar a denominação dos itens a serem calculados e suas respectivas unidades. Então é criada uma coluna, onde é colada a soma das necessidades brutas para cada item. Para o cálculo das necessidades líquidas, criam-se mais três colunas: i) Coluna "QE": referente às quantidades existentes em estoque que é vinculada à planilha QE; ii) Coluna "ES": vinculada à planilha dos estoques de segurança, e refere-se ao estoque necessário para assegurar a empresa de possíveis falhas no processo; iii) Coluna "NL": onde contém a fórmula NL = NB - QE + ES, ou seja, a necessidade líquida é igual à necessidade bruta de um determinado item subtraídos da quantidade que a empresa possui em estoque, mais a quantidade calculada relativo ao estoque de segurança. E para finalizar é colocada a última coluna que multiplica a necessidade líquida pelo preço unitário do item, criando o custo que deverá ser investido para aquela produção simulada.
A entrada dos dados de simulação ocorre através da planilha Plano Mestre (PM). A simulação é feita quando são sugeridas uma previsão de demanda e uma data de planejamento. A entrada destes dados é efetuada através da tabela previsão de demanda.
É possível simular outros dados. As informações encontradas nas planilhas dos dados básicos de entrada podem ser manipuladas conforme a estratégia da organização, criando diversos quadros, descrevendo diversas situações.
As respostas ao MRP, com exceção das necessidades líquidas, encontram-se junto à planilha PM, onde ocorrem também as entradas dos dados de simulações. Esta junção entre a entradas e saídas de informações, foi feita para uma melhor visualização, mas fica a critério das empresas este feito. As respostas ao MRP encontradas na planilha PM, são divididas em dois momentos: i)Quando comprar e quando produzir - os dados de quando comprar e quando produzir, são simplesmente vinculados à planilha CDM; ii) Capacidade de processo - os dados da capacidade de processo são vinculados à planilha CC.
A Figura 2 apresenta uma parte destas respostas, ou seja, as informações referentes à data de compra e produção:
Figura 2 - Quando comprar e quando produzir
4. Considerações Finais
Na primeira etapa deste trabalho foi revelado o problema existente na realidade das pequenas empresa, que no qual trata-se, do desenvolvimento de um aplicativo para o cálculo das necessidades dos materiais justificando a necessidade da existência do mesmo. Em um segundo momento, foi resgatado o referencial teórico acerca do modelo de gestão de materiais conhecido por MRP. Na seqüência foi colocado a disposição a contextualização do aplicativo gerado, onde é demonstrado que é possível a construção de modelos de simulação baseado em planilhas eletrônicas. Com a utilização do modelo MRP, torna-se possível planejar as compras reduzindo os estoques e por conseqüência os custos envolvidos, mas o alto custo de softwares especializados força as empresas de pequeno porte a gerirem seus estoques sem o auxílio destas ferramentas, podendo-se concluir que isto acontece devido à falta de capital para investimentos, mas principalmente pela insegurança de adquirir um produto caro que não atenda satisfatoriamente a gestão dos materiais.
A construção de aplicativos em planilhas simples do Microsoft Excel propiciaria um modelo a resolver os problemas citados anteriormente a baixo custo, pois a conclusão que se chegou foi a da possibilidade de administrar os materiais através de aplicativos como o proposto pelo o objetivo específico.
Enfim, este trabalho demonstrou a importância do desenvolvimento de aplicativos construídos em planilhas eletrônicas como solução prática e de baixo custo para empresas de pequeno porte. O cálculo das necessidades de materiais teve a intenção de existir como modelo para a construção de protótipos a resolver problemas de outras empresas e de demonstrar que existe a possibilidade construir de modelos a partir de planilhas simples.
Os autores afirmam que é necessário aplicar sistematicamente o aplicativo construído durante um período de tempo suficiente para observação, análise e melhoria do seu desempenho, em empresas reais de pequeno porte.
Evidentemente que, atualmente, existem soluções muito mais sofisticadas e funcionais em termos de gestão de materiais, como por exemplo, o Planejamento Fino de Produção, porém a intenção do presente trabalho consistiu em desenvolver um aplicativo voltado para pequenas empresas, uma vez que soluções mais sofisticadas ainda estão completamente fora do alcance de empresas de porte.
5. Referências
ARNOLD, J. R. Tony. (1999). Administração de Materiais. São Paulo: Atlas.
DIAS, Marco Aurélio P. (1993). Administração de materiais: uma abordagem logística. São Paulo: Atlas.
IMAM. (1996). Gerenciamento da Logística e cadeia de suprimentos/ Logistc Training internacional; São Paulo: IMAM.
GONÇALVES, Paulo Sergio. Et. Al. (1979). Administração de Estoques. Rio de Janeiro: Interciência.
MOREIRA, Daniel Augusto. (2000). Administração da Produção e Operações. 5 ed. São Paulo: Pioneira.
SLACK, Nigel. Et. Al. (1997). Administração da Produção. São Paulo: Atlas.