OEE: O que é? E como calcular?
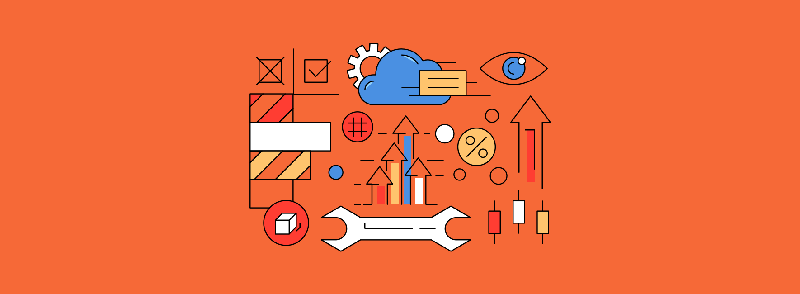
Por: Admin - 23 de Março de 2020
Baseado no artigo "Considerações sobre o desdobramento do cálculo do Índice de Rendimento Operacional Global (IROG) utilizado como pilar de sustentação para a abordagem de Gestão dos Postos de Trabalho (GPT) para sistemas produtivos" de Altair Flamarion Klippel, José Antonio Valle Antunes Júnior, Marcelo Klippel e Ricardo Augusto Cassel.
A sigla OEE tem origem na expressão em inglês Overall Equipment Effectiveness, que significa Eficiência Global do Posto de trabalho, e é um indicador utilizado para medir a eficiência global dos postos de trabalho (equipamentos).
O indicador OEE permite responder a três perguntas importantes:
- Quanto tempo o posto de trabalho fica disponível para operar?
- Qual é o desempenho do posto de trabalho enquanto ele estiver operando?
- Quantos itens foram produzidos que atendem aos padrões de qualidade?
O cálculo da eficiência dos postos de trabalho surgiu durante o desenvolvimento da metodologia Manutenção Produtiva Total (Total Productive Maintenance), realizado por Nakajima (1988), que utilizou a terminologia OEE para defini-lá.
Cálculo do OEE
O índice OEE pode ser calculado de duas maneiras:
- Através de uma equação geral, que relaciona o tempo de agregação de valor de um posto de trabalho em relação ao tempo que ele está disponível para produção;
- A partir do cálculo de índices que compõem a eficiência de um posto de trabalho.
A equação geral é utilizada considerando-se se o posto de trabalho é restritivo ou não restritivo, conforme explicado neste texto.
Equação 1 – Eficiência global de um posto de trabalho
onde:
µglobal = Eficiência Global do posto de trabalho
n = Quantidade de itens produzidos
i = Tipo dos itens produzidos
tpi = Tempo de ciclo de cada item produzido
qi = Quantidade boas de cada item produzido
T = Tempo total disponível para produção
Ao analisar-se esta equação, observa-se que a multiplicação do tempo de ciclo de um item pela quantidade boa produzida deste item, em um determinado posto de trabalho, corresponde na realidade ao tempo de agregação de valor deste posto de trabalho no processo de produção, ou seja, o tempo em que efetivamente o mesmo funcionou adicionando valor ao produto em processo, conforme a fórmula:
Tempo de agregação de valor = tpi x qi
O tempo de ciclo (tpi) é o tempo que um operador devidamente treinado processa um item em um posto de trabalho específico, de forma a realizá-lo normalmente, isto é, sem realizar esta atividade velozmente, de maneira a não conseguir manter o mesmo ritmo durante o seu período de trabalho, e sem realizá-la de forma muito lenta, como ocorre normalmente quando um operador se encontra em fase de treinamento ou não está familiarizado com a operação. Para tanto, é importante que a operação seja padronizada, documentada através de um Procedimento Operacional (PO).
Além do tempo de ciclo, é necessário entender três outros conceitos, são eles: Gargalos, Recursos com Capacidade Restrita (Capacity Constraints Resources - CCRs) e Recursos com Problemas de Qualidade (RPQ).
Os Gargalos são os recursos (posto de trabalhos, instalações e pessoal) cuja capacidade disponível é menor do que a capacidade necessária para atender a demanda do mercado. Estes devem dar a “batida” da produção, fornecendo o ritmo de produção para toda a fábrica.
Os Recursos com Capacidade Restrita ou CCRs são os recursos que, em média, apresentam capacidade de produção superior à demanda de mercado, porém quando estes recursos não são devidamente programados e gerenciados, o acúmulo da demanda pode se tornar maior que a capacidade produtiva, fazendo com que esse ativo apresente os efeitos de um recurso gargalo.
Os Recursos com Problemas de Qualidade ou RPQs são também importantes para a gestão visto que a ocorrência deles gera perdas e/ou retrabalho. Os RPQs se fazem ainda mais preocupantes se estiverem localizados após um recurso gargalo no fluxo de produção, pois indica que o recurso gargalo será sobrecarregado com alguns produtos que estarão fora do padrão de qualidade. Quando os RPQs encontram-se antes de gargalos, os produtos defeituosos podem ser descartados antes de passarem pelos gargalos, não sobrecarregando-os com itens fora do padrão.
A importância de conhecer essas definições está no fato de que não se deve calcular da mesma forma o OEE para todos os posto de trabalhos, uma vez que o tempo disponível T, a ser considerado na fórmula, depende do posto de trabalho ser ou não um recurso restritivo no fluxo de produção.
Se o posto de trabalho é um recurso crítico (gargalo)
Neste caso, o indicador OEE é denominado de TEEP - Produtividade Efetiva Total do Posto de trabalho (Total Effective Equipment Productivity). O tempo T considerado na Equação 1 é o tempo calendário. Isto se explica pelo fato de que, sendo o posto de trabalho um gargalo, todo o tempo disponível deve ser utilizado na produção. Ou seja, não deve ser subtraído do tempo total disponível T o tempo de paradas programadas, como almoço, férias, etc. Este índice indica o tempo que pode ser ganho para produzir e corresponde a produtividade real do sistema produtivo no gargalo. A equação geral transforma-se em:
Equação 2 – Eficiência global de um posto de trabalho restritivo
Se o posto de trabalho é um recurso não gargalo (CCRs e RPQs)
O tempo T considerado na Equação 1 é o tempo programado, obtido pela diferença entre o tempo calendário e o tempo das paradas programadas. Por não se tratar de um posto de trabalho gargalo, é possível programar certas paradas como parada para almoço, ginástica laboral, etc., uma vez que a não paralisação deste posto de trabalho geraria estoques intermediários antes do gargalo. Este índice indica a eficácia do posto de trabalho durante o tempo de operação programado. A equação geral transforma-se em:
Equação 3 – Eficiência global de um posto de trabalho não restritivo
As considerações acima consistem no cálculo da eficiência global dos postos de trabalhos através da equação geral (Equação 1), na qual é utilizado o tempo de ciclo e o tempo total de produção. No entanto, o cálculo do OEE por meio da equação geral não permite identificar quais são as principais causas de ineficiência. Em vista disso, a Equação 1 pode ser expressa, também, em função dos índices de eficiência que caracterizam os três fatores que compõem o OEE: disponibilidade, desempenho e qualidade. Estes índices permitem identificar as principais causas das ineficiências observadas nos posto de trabalhos.
Equação 4 – Eficiência global de um posto de trabalho e seus índices
onde:
µ1 = Índice de Disponibilidade
µ2 = Índice de Desempenho
µ3 = Índice de Qualidade
Cada um destes índices é obtido por meio de uma equação complementar apresentada a seguir. Esses índices são importantes para identificar e tratar aspectos pontuais. Como pode ser observado no decorrer deste texto, estas equações buscam explicar as ineficiências observadas à partir da equação geral do OEE.
Disponibilidade
O Índice de Disponibilidade (µ1) corresponde ao tempo em que o posto de trabalho ficou disponível, excluindo-se as paradas não programadas. É relacionado, portanto, com a paralisação do posto de trabalho, isto é, quando a sua velocidade cai a zero, sendo calculado pela seguinte equação:
Equação 5 - Índice de Disponibilidade
sendo:
Tempo Total = tempo que o posto de trabalho está disponível para produzir (calendário ou programado)
Tempo Paradas = tempo de paradas não programadas
Quanto menor for o valor do Índice de Disponibilidade (µ1), maior será o potencial de aumento de utilização do posto de trabalho, pois um baixo valor indica que o posto de trabalho sofreu muitas paradas não programadas, o que provavelmente comprometeu a sua produção, impactando diretamente no OEE.
Cabe ressaltar que como o Tempo Total a ser considerado na Equação 5 se refere ao tempo em que o recurso ficou disponível. Se, por exemplo, por problemas de demanda de mercado, for programado a operação do recurso não gargalo apenas entre 2ª até 5ª feira, durante 2 turnos de 8 horas por dia, o tempo disponível na semana para ser considerado na Equação 5 será de 3.840 minutos (960 minutos / dia x 4 dias).
Este raciocínio é diferente se, por exemplo, o recurso ficar parado na 6ª feira e no sábado devido à falta de peças. Isto porque, havendo a programação de operação para estes dias, o recurso estará disponível neste período, devendo o Tempo Total a ser considerado na Equação 5 ser de 5.760 minutos (2ª até sábado, correspondendo a 1440 minutos / dia x 6 dias). (visto que a causa da paralisação foi outra que não a falta de programação).
Vale ressaltar que, para recursos gargalos, o Tempo Total utilizado corresponde ao tempo calendário, não considerando tempos de paradas programadas
Os recursos que processam pouca variedade de itens têm a tendência de ter este índice elevado, devido a pouca necessidade de paradas para setup. Quando há grande variedade de itens, são exigidos muitos setups, e os tempos de paradas aumentam consideravelmente.
Performance
O Índice de Desempenho (µ2) corresponde à performance do recurso, sendo calculado em função do tempo disponível e à redução de sua velocidade, operação em vazio e pequenas paradas, conforme mostra a equação 6:
Equação 6 - Índice de Desempenho
Considerando que estes tempos de ineficiência são de difícil visualização, este índice é calculado a partir da equação 7 abaixo:
Equação 7 – Cálculo do Índice de Desempenho
Existem basicamente duas causas para que o Índice de Desempenho (µ2) tenha um valor baixo:
- Causas técnicas: operação em vazio por falta de alimentação de itens (não ocorrendo, neste caso, tempo de agregação de valor); ou tempo de ciclo muito alto – com consequente redução da velocidade de processamento – em função da falta de treinamento do operador. Um operador treinado e experiente tem um tempo de ciclo para determinado item inferior ao de um operador não treinado e inexperiente;
- Falta de registro no Diário de Bordo: quando o operador não registra os motivos das paradas (por exemplo, muitas pequenas paradas não registradas pelo operador, mas que no somatório acabam ocasionando um tempo de paralisação elevado, influenciando diretamente para um baixo valor do índice).
Qualidade
O Índice de Qualidade (µ3) está relacionado com a qualidade dos itens produzidos, sendo calculado em função do tempo de operação real, excluindo o tempo gasto com refugo e/ou retrabalho, através da Equação 7:
Equação 8 – Índice de Qualidade (Tempos)
O Índice de Qualidade (µ3) também pode ser calculado – caso não sejam conhecidos os tempos da Equação 8 – em função das quantidades produzidas conformes e não conformes, pela Equação 9:
Equação 9 – índice de Qualidade (Quantidades)
Como este índice está relacionado com a qualidade, ele é de fácil visualização, visto que normalmente o posto de trabalho é imediatamente paralisado após a constatação da fabricação de itens defeituosos, para correção do defeito que está originando o retrabalho ou refugo. Em função deste fato, a tendência é de que os valores deste índice sejam elevados. Valores baixos para este Índice são obtidos quando há muitos ajustes após uma operação de setup, ocasionando grande quantidade de peças refugadas.
A Figura 1 representa a relação entre o tempo decorrido e os índices de eficiência operacional de um posto de trabalho. A partir do tempo calendário (TEEP), as causas de ineficiência vão gradativamente reduzindo o tempo de agregação de valor obtendo-se o TEEP/OEE.
Figura 1 – Tempo x Ineficiências
Exemplos
A produtividade horária determina a quantidade de itens produzidos em um determinado posto de trabalho durante o período de uma hora. A questão importante acerca da produtividade horária consiste no fato de que esta indica a quantidade que deveria ser produzida em uma hora, com eficiência de produção de 100%. A capacidade real do posto de trabalho consiste no fator entre a produtividade horária e a eficiência global do posto de trabalho, ou seja, o OEE.
Para exemplificar, considere-se que um posto de trabalho gargalo tenha uma produtividade de 450 unidades por hora e produza, neste período, apenas 279 unidades. Assim, calcula-se que este gargalo tem uma eficiência de 62%.
Eficiência = 279/ 450 = 0,62
Desta maneira, observa-se que o cálculo da eficiência do posto de trabalho crítico é de extrema importância, pois através deste pode-se chegar à percepção da sua real capacidade e, consequentemente, da capacidade da fábrica.
Para reforçar os conceitos dos índices de eficiência acima abordados, considere a Figura 2 abaixo. Na tabela inserida na mesma destaca-se cada elemento que compõem a equação geral para o cálculo da eficiência global de um posto de trabalho:
Figura 2 – Elementos que compõem o cálculo da eficiência global de um posto de trabalho
Conclusão
Não raras vezes empresas calculam as eficiências dos postos de trabalho apenas através da equação geral do OEE (Equação 1). Porém, quando se deseja buscar as verdadeiras causas básicas da baixa eficiência observada nos ativos produtivos das Organizações Brasileiras, se faz necessária a aplicação das demais equações para se chegar aos índices que compõem o OEE:
- Índice de Disponibilidade (paradas)
- Índice de Desempenho (queda de performance)
- Índice de Qualidade (produção de itens não conformes)
A abordagem de Gestão de Postos de Trabalho (GPT) consiste em ampliar a utilização dos ativos (posto de trabalhos, instalações e pessoal) nas Organizações, tomando como base esse conjunto de índices que compõem a eficiência. A Gestão dos Postos de Trabalho - GPT visa otimizar os ativos, aumentando, assim, a capacidade e a flexibilidade da produção, sem que seja necessária a realização de investimentos adicionais em termos de capital.
Essa solução tem como objetivo gerir de modo mais eficaz possível os postos de trabalho das empresas industriais levando em consideração questões trazidas à tona pelo OEE, como a falta de recursos materiais e humanos, problemas de qualidade, etc. Para que essa gestão possa ser feita, é necessário que além de identificar todas as restrições dos sistemas produtivos com base conceitual da Teoria das Restrições (TOC), estas sejam tratadas de maneira correta de forma a buscar um melhor resultado econômico-financeiro para a empresa por meio de técnicas consagradas pelo Sistema Toyota de Produção (STP).
Calculadora de OEE e Benchmark da Indústria
Existem soluções de coleta de dados fabris automaticamente, como os sistemas MES, que auxiliam no controle e monitoramento das etapas de produção. Quer saber mais? Converse com a nossa empresa parceira, eFact.