Montagem Sistêmica dos Indicadores de Desempenho nas Empresas Industriais – Uma Abordagem a partir da Teoria das Restrições – TOC e do Sistema Toyota de Produção – STP
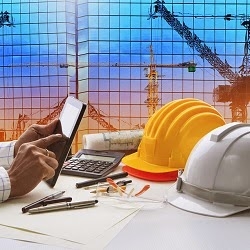
Por: Admin - 30 de Dezembro de 2014
Autores:
José Antonio Valle Antunes Júnior (UNISINOS) junico@produttare.com.br
Marcelo Klippel (UNISINOS) marcelo@klippel.com.br
Resumo
O presente artigo tem por objetivo apresentar uma proposta de construção de um Sistema de Indicadores de Desempenho nas Empresas Industriais, ampliando-se a lógica de Indicadores proposta pela Teoria das Restrições. Os autores utilizam a abordagem da Teoria das Restrições concomitantemente a um conjunto de indicadores propostos visando o acompanhamento da rotina de produção, que tem por base as melhorias em Engenharia Industrial, proporcionadas pelos princípios, conceitos e técnicas do Sistema Toyota de Produção. O artigo apresenta os indicadores propostos de maneira priorizada e hierarquizada, subdividindo-se em indicadores voltados para a Função Processo e indicadores voltados para a Função Operação. Sendo assim, os autores propõem e descrevem um Método de Trabalho, buscando a viabilidade da condução do trabalho de montagem do Sistema de Indicadores em Empresas Industriais.
Palavras chave: Indicadores, TOC, STP
1. Introdução
O presente artigo busca abordar um dos temas mais importantes na realidade das Organizações Industriais de hoje em dia - a definição de Sistemas de Indicadores que possam facilitar a implantação e desenvolvimento dos chamados Sistemas Modernos de Produção baseados na Teoria das Restrições (TOC – Theory Of Constrainst) e no Sistema Toyota de Produção (também chamado de Sistemas de Produção Enxutos, Just-In-Time, Lean Production, etc.).
Para a montagem destes Sistemas de Indicadores torna-se necessário explicitar os aspectos conceituais relativos a TOC e do STP e da problemática dos indicadores propriamente ditos. Os aspectos conceituais devem abordar os conceitos, princípios e técnicas que norteiam e suportam as duas teorias em cena.
2. Referencial Teórico
O referencial teórico do presente trabalho parte da necessidade de abordar alguns conceitos visando a montagem sistêmica de Indicadores de Desempenho de Empresas Industriais. Na seqüência do trabalho serão apresentados sucintamente estes conceitos.
A montagem consistente de um Sistema de Indicadores que suporte a implantação e desenvolvimento de um Sistema Moderno de Produção em uma Empresa Industrial deve levar em consideração a lógica global da Teoria das Restrições. A TOC propõe a existência de dois níveis de Indicadores de Desempenho, a saber: Os Indicadores Globais e Operacionais de alcance da Meta da Empresa. A Meta da Empresa é definida como “ganhar dinheiro hoje e no futuro” (Goldratt, 1997).
Os Indicadores Globais propostos pela TOC são: Lucro Líquido (LL), Retorno Sobre o Investimento (RSI) e Caixa (C). O Lucro Líquido consiste em um indicador absoluto do alcance da Meta. O Retorno Sobre o Investimento (RSI) é um indicador relativo do alcance da Meta. O RSI permite a comparação do desempenho de Empresas Industriais que trabalham com níveis diferenciados de investimentos. Já o Caixa representa uma condição necessária de alcance da Meta. Goldratt (1997) afirma: “se você tem Caixa, Caixa não é importante; se você não tem Caixa, Caixa é o mais importante”. Os Indicadores Globais são usualmente utilizados no âmbito da Alta Direção da Empresa.
Os Indicadores Operacionais propostos pela TOC são: Ganho (G), Inventários (I) e Despesas Operacionais (DO). O Ganho representa um somatório da multiplicação das margens de contribuição unitárias (preço – custos variáveis) pelas quantidades. Os Inventários na TOC se constituem basicamente de:
i) Matérias-Primas, Estoques em Processo (Work-In-Process) e Produtos Acabados;
ii) A parte relativa aos equipamentos (Custos Fixos) necessários para a efetivação da produção.
As Despesas Operacionais se constituem de elementos necessários para a efetivação da produção (por exemplo: energia elétrica e material de consumo). Obviamente na lógica da TOC boas decisões são tomadas quando se tende a obter aumento do Ganho e a redução dos Inventários e das Despesas Operacionais.
Dettmer (1997) apresenta uma discussão interessante acerca de quais dos Indicadores Operacionais seriam os mais importantes para uma Empresa genérica. O autor afirma que faz sentido empenhar, em um primeiro momento, tanto esforço quanto possível nas atividades que objetivam aumentar o Ganho da empresa. Em um segundo momento, o autor coloca que as ações devem ser direcionadas para a redução do Inventário e das Despesas Operacionais. Porém, ainda afirma que a redução do Inventário e das Despesas Operacionais devem ser buscadas sem penalizar o Ganho da empresa.
Os autores do presente trabalho propõem que sejam, também, utilizados Indicadores Locais de alcance da Meta. Os Indicadores Locais não estão previstos diretamente na TOC, porém são essenciais para a construção de um Sistema de Indicadores. Isto porque representam o dia a dia da Organização, ou seja, estão profundamente envolvidos com os aspectos a rotina e a melhoria do sistema produtivo das Empresas. Alguns exemplos de Indicadores Locais são: Sincronização da Montagem, Índices de Refugo, Índices de Retrabalho, Índice de Rendimento Operacional Global dos Equipamentos - IROG, Média de Produção Diária, índice de absenteísmo etc.
O problema central para a montagem de um Sistema de Indicadores eficaz consiste na seguinte questão: Como garantir um alinhamento entre os Indicadores Locais – que devem ser concebidos e utilizados - e os Indicadores Globais e Operacionais do alcance da Meta da Empresa? Em outros termos, a questão de centralidade consiste em assegurar que as melhorias nos Indicadores Locais (por exemplo, Melhoria da Sincronização da Montagem ou do IROG) realmente venham a conduzir a melhorias nos Indicadores Operacionais e Globais do alcance da Meta da Empresa Industrial.
A questão supracitada aponta para a necessidade de estabelecer critérios objetivos e eficazes que permitam hierarquizar os Indicadores Locais adotados. Os autores deste artigo propõem que os critérios básicos de hierarquização dos Indicadores Locais sejam:
1) A própria Teoria das Restrições para assegurar que os Indicadores Locais adotados estejam em consonância com a melhoria dos Indicadores Operacionais e Globais propostos por Goldratt;
2) A adoção dos princípios gerais do Sistema Toyota de Produção, mais especificamente da lógica do Mecanismo da Função Produção.
Um exemplo pode servir para explicar a necessidade de levar em consideração a visão de sistema proposta pela TOC. Ocorre que nem todos os Indicadores Locais adotados estão de acordo com a melhoria da Meta da Empresa. Pode-se tomar como exemplo o Indicador “Média Diária Produzida”. Ao aumentar-se a Média Diária Produzida em uma dada Fábrica ou Unidade de Manufatura sem que se tenham Vendas asseguradas (ou seja, produção para estoque) tem-se um incremento das horas trabalhadas, porém não das horas vendidas. Com isso tende-se a não aumentar o Ganho geral do sistema ((Preço – Custos Variáveis) X Quantidade Vendidas, enquanto os Inventários de Processo e de Produtos Acabados são incrementados. Neste sentido, este Indicador Local não está alinhado com o atingimento da Meta da Empresa.Obviamente, que está se falando de situações normais de trabalho. No caso de final do ano, por razões de ordem estratégica pode-se prever férias e adotar uma política de geração de estoques de produtos acabados. Neste caso, a produção sem que existe demanda imediata detectada – ou seja, trabalho levando em conta a Previsão de Vendas – pode ser aconselhável na medida em que pode melhorar o desempenho econômico-financeiro da Empresa.
A adoção dos princípios gerais do STP permite priorizar a análise dos Indicadores voltados à Função Processo, ou seja, para a melhoria dos fluxos produtivos (acompanhamento dos materiais no tempo e no espaço). Shingo (1996b) afirma que a Função Processo pode ser entendido como sendo o fluxo de produtos nos diferentes estágios de transformação gradativa pelos quais a matéria-prima se move nos Sistemas Produtivos. Já a Função Operação refere-se ao diferentes estágios no qual um trabalhador (e/ou máquina) pode trabalhar em diferentes produtos, isto é, um fluxo temporal e espacial, que é firmemente centrado no trabalhador (e/ou nas máquinas).
Neste sentido, indicadores como a Sincronização da Produção, Índices de Entrega, Índices de Refugo/Retrabalho estão diretamente alinhados com a Função Processo. De outra parte, deve-se adotar um conjunto de Indicadores ligados a Função Operação (acompanhamento das pessoas e equipamentos no tempo e no espaço). Alguns exemplos de indicadores voltados a Função Operação são: Índice de Rendimento Operacional Global – IROG, Horas Paradas de Manutenção, Eficiência de Alocação das Operações, etc.
Um exemplo da necessidade de adotar os princípios gerais do STP consiste em perceber que determinadas reuniões gerenciais que ocorrem nas Empresas Industriais não obedecem ao estabelecimento de uma clara hierarquia entre os Indicadores voltados ao Processo (por exemplo: Índice de Sincronização, Qualidade, etc.) e aqueles voltados para as Operações (IROG, etc.). Isto faz com que não fique claro, do ponto-de-vista da gestão, qual deve ser a hierarquia de trabalho em relação às Rotinas e Melhorias em termos de Tomada de Decisão.
A partir dos conceitos supracitados é possível propor um Sistema de Indicadores sistêmicos que tenha como características centrais: i) a simplicidade; ii) a facilidade de implantação e operacionalização; iii) a priorização em termos da análise. Desta forma será possível tomar decisões na Empresa da forma clara e direta possível.
Finalmente, uma regra prática importante consiste em adotar um Sistema de Indicadores sistêmicos que utilize o mínimo de Indicadores Operacionais e Locais possíveis. Embora este seja um critério difícil de justificar do prisma teórico, ele segue um princípio básico de tornar, o máximo possível, pragmático a implantação do Sistema.
A título de exemplo da abordagem geral proposta neste artigo apresentar-se-á no item que se segue um exemplo de aplicação dos conceitos acima discutidos em uma Empresa Industrial que Goldratt intitula de Empresas do Tipo A (Antunes, 1998). As Empresas do tipo A caracterizam-se por uma série de Minifábricas de Componentes que entregam para a linha de montagem da forma mais sincronizada possível. Este exemplo será apresentado na forma de um Método de Trabalho para a Montagem de um Sistema de Indicadores em Empresas Industriais do Tipo A.
3. Método de Trabalho Proposto para a Montagem de Sistemas de Indicadores em Empresas Industriais do Tipo A
A seguir apresenta-se um Método de Trabalho baseado em etapas (passos) para levar adiante a montagem de Indicadores de Desempenho Sistêmicos para Empresas Industriais do tipo A. É relevante destacar que, no exemplo explicitado a seguir, o Método de Trabalho Proposto considera simultaneamente: i) Priorização e hierarquização dos Indicadores propostos; ii) Os mecanismos de gestão que permitem colocar em prática a priorização e a hierarquização dos indicadores propostos.
PASSO 1 – Proposição de um Sistema de Indicadores
Em grandes linhas, as reuniões de gestão deveriam ser realizadas a partir da lógica apresentada na Tabela 1:
Tabela 1 - Sistema de Indicadores por Ordem de Hierarquia
Em Ordem de Hierarquia
Indicadores da Função Processo Indicadores da Função Operação
1. Indicadores de Aderência ao Programa – Sincronização da Produção
2. Índice de Refugos e Retrabalhos
3. Controle dos Inventários Globais de Matérias-Primas, Materiais em Processo e Produtos Acabados
4. Custos Gerais de Matéria-Prima
5. Despesas Operacionais
6. Indicadores dos Tempos de Preparação
7. Indicadores do IROG das Máquinas Críticas
a) Indicadores de Aderência ao Programa – Sincronização da Produção
Propõe-se adotar o Indicador de Sincronização da Linha de Montagem como um balizador essencial do Sistema de Indicadores proposto. Neste caso, a idéia consiste em mensurar aderência da montagem ao Plano de Montagem estabelecido a priori. Todas as causas do não atendimento da Montagem podem passar, se possível, a serem analisadas diariamente. Sugere-se a construção de um gráfico de PARETO semanal e mensal das principais causas de não aderência ao Plano de Montagem. As principais causas de não aderência ao Plano de Montagem devem ter um tratamento direto e explicito na construção dos Planos de Ação de melhorias.
No caso dos Indicadores Locais de atendimento das Unidades de Manufatura, uma das idéias consiste em montar um indicador de aderência a partir de duas lógicas distintas e inter-relacionadas (variedade de itens atendidos e quantidades de itens atendidos). Porém, as datas consideradas devem ser compatíveis com os buffers de tempo na montagem. Por exemplo, se um produto for montado no dia 20 de Janeiro e para isso o planejamento supor que os componentes devem chegar 5 dias antes, portanto no dia 15 de Janeiro, então o indicador de aderência das Unidades de Manufatura de Componentes deve ser calculado em relação ao dia 15 de Janeiro. Este critério pode ser justificado na medida em que a perda do prazo do dia 15 de Janeiro permite alertar o Sistema sem que, necessariamente, isto implique em que os prazos de montagem sejam perdidos.
b) Índice de Refugos e Retrabalhos
Estes são Indicadores Locais essenciais do prisma da Função Processo. A noção básica a ser perseguida consiste em analisar de forma detalhada, não somente os Indicadores Locais mais gerais do Índice de Refugos e Retrabalhos, como também explicitar os pontos onde eles foram gerados. Estes dados podem, por exemplo, alimentar o Banco de Dados da Empresa, para que as ações de melhorias objetivas possam ser planejadas e implantadas na prática.
c) Controle dos Inventários Globais de Matérias-Primas, Materiais em Processo e Produtos Acabados
A redução dos Custos Financeiros é um dos elementos centrais sugeridos no âmbito da aplicação do Sistema Toyota de Produção e da Teoria das Restrições. Desta forma, os estoques de matérias-primas, estoques em processo e de produtos acabados necessitam ser rigorosamente mensurados e controlados.
Cabe ressaltar que, para que uma análise global e sistêmica possa ser levada adiante, torna-se necessário olhar de forma conjunta os Indicadores Locais propostos. Por exemplo, um nível de atendimento ótimo pode ser obtido na Montagem as custas da utilização de estoques em processo elevados. Sendo assim, uma das noções básicas consiste em planejar um determinado nível de Estoques em Processo e Acabados máximo, e só então verificar o desempenho dos indicadores de sincronização da Montagem.
d) Custos Gerais de Matéria-Prima
O Ganho do Sistema Produtivo está diretamente associado à chamada Margem de Contribuição unitária dos produtos (Preço – Custos Variáveis). Entre os Custos Variáveis, o principal deles é a Matéria-Prima. Sendo assim, um acompanhamento do Custo das Matérias-Primas compradas é muito importante do prisma da Manutenção e da Melhoria do Ganho total da Empresa.
e) Despesas Operacionais
As Despesas Operacionais envolvem contas como Mão-de-Obra/Mente-de-Obra direta ou produtiva e indireta, Depreciação, Horas-Extras, Despesas Energéticas, Custo do Ferramental, etc. Neste sentido, representam o conjunto de despesas agregadas associadas a Função Produção. Desta maneira o seu acompanhamento, em termos de totalização, é relevante para verificar o desempenho global da Função Produção na Fábrica. A melhor idéia a ser desenvolvida neste caso, parece ser o gerenciamento por exceção através de Custo-Padrão. Ou seja, estabelece-se no início do mês um padrão total das diversas despesas (por exemplo, Despesas Gerais com Pessoal, Despesas Gerais com Ferramentas, Energia Elétrica, Utilidades etc.), que será confrontadas os custos realmente incorridos. Desta forma, ao final de cada mês, podem ser enfocados gerencialmente os itens onde as discrepâncias entre o planejado e o executado são maiores. Também, é interessante elaborar uma “Curva ABC” das despesas para que os itens A sejam controlados com o rigor necessário.
f) Indicadores dos Tempos de Preparação
A flexibilidade é tema fundamental para as Fábricas País (por exemplo: nas Indústrias do tipo Metal-Mecânica de montagem – tipo A) , em função basicamente das necessidades objetivas de mercado que apontam para a necessidade de produção de Volumes relativamente baixo, se comparados com os Países de Primeiro Mundo, associado com uma elevada Diversidade/Variedade de Produtos fabricados. Sendo os tempos de preparação essenciais para a obtenção desta flexibilidade, estes devem ser cuidadosamente controlados. Neste caso, a idéia consiste em controlar os tempos médios e as freqüências de setup das máquinas críticas em bases semanais. A partir destes dados, nas máquinas críticas devem ser feitos Planos de Ação para as principais causas de paradas. A execução destes Planos de Ação poderá, então, ser controlada sistematicamente.
g) Indicadores do IROG das Máquinas Críticas
É preciso incrementar a utilização dos ativos fixos da Empresa. Para isso o IROG (Índice do Rendimento Operacional Global) é fundamental. Nas máquinas críticas a idéia consiste em controlar o IROG em uma base diária. A partir deste indicador várias ações de melhorias podem ser realizadas, tendo como pressupostos os dados e os fatos objetivos das Quebras nos Postos de Trabalho.
Cabe ressaltar novamente que é preciso observar as questões de maneira sistêmica. Incrementos no IROG podem ser obtidos reduzindo-se o número de setups realizados. Caso isto venha a ocorrer, ter-se-á a formação de estoques em processo elevados – o que é contrário à idéia de melhorar a Função Processo – nos fluxos produtivos. Sendo assim, deve-se priorizar o indicador local que leva a redução do tempo de setup em relação ao aumento do IROG. Ou seja, de maneira geral, as melhorias no IROG devem ser buscadas sem a redução do número de setups. É interessante verificar o total de peças produzidas (“Média Diária Produzida”) quando da análise dos IROGs das Máquinas Críticas. Deve haver uma relação de causa-efeito clara entre os IROGs e a “Média Diária Produzida”.
Finalmente, sugere-se que nas reuniões diárias nas Unidades de Manufatura (Fábrica) sejam analisados os seguintes indicadores:
a) Indicadores de Aderência ao Programa – Sincronização da Produção;
b) Índice de Refugos e Retrabalhos;
f) Indicadores dos Tempos de Preparação;
g) Indicadores do IROG das Máquinas Críticas.
Outros tópicos específicos podem ser tratados nas reuniões (por exemplo: Segurança Industrial, Gestão Ambiental, Recursos Humanos, etc.), após a análise dos Indicadores Locais (a, b, f e g) que dão uma visão geral do desempenho econômico-financeiro das Unidades de Manufatura (Fábrica).
Sugere-se que sejam realizadas uma reunião mensal em cada Unidade de Manufatura (Fábrica ou Mini-Fábrica) e uma reunião geral com a Direção Industrial. Tanto na reunião mensal das Unidades de Manufatura como na com a Direção Industrial sugere-se que sejam analisados em detalhes os indicadores propostos (de a até g).
Cabe ressaltar que em todos os casos, sugere-se que seja respeitada a Ordem de Prioridade proposta (de a até g), o que permite obter uma visão sistêmica das ações realizadas. Outros Indicadores Locais de Melhorias podem ser acrescentados. Por exemplo, a melhoria dos Mapas de Habilidades dos Colaboradores ao longo do mês é interessante de ser discutido na reunião geral das Unidades de Manufatura com a Direção Industrial.
PASSO 2 – Reunião com a Direção Industrial para Avaliar as Sugestões Levantadas no PASSO 1
O passo 2 implica na realização de uma reunião com a Direção Industrial visando estudar criticamente as proposições de Indicadores feitas no Passo 1. Após esta reunião pode-se gerar um Documento de Referência básico a ser discutido com os gerentes das diferentes Unidades de Manufatura (Fábricas ou Mini-Fábricas) e outros profissionais que se julgar conveniente para que as melhorias no Sistema de Indicadores possam ser elaboradas.
PASSO 3 – Reunião Final para a Análise dos Indicadores Propostos
Sugere-se que seja realizada uma reunião com os profissionais envolvidos para validar a proposição de Sistemas de Indicadores (Indicadores Globais, Operacionais e especialmente Locais). Esta reunião é relevante para que seja possível compartilhar as idéias globais envolvidas na montagem dos Sistemas de Indicadores.
PASSO 4 – Detalhamento dos Indicadores Locais
Eventualmente, tornar-se-á necessário um detalhamento operacional para a obtenção dos Indicadores Locais (por exemplo, os Indicadores de Aderência - Sincronização da Montagem). Neste caso, é interessante propor um 5W1H para o levantamento objetivo de todos os indicadores.
4. Considerações Finais
O artigo apresenta uma proposta para Montagem de um Sistema de Indicadores de Desempenho de maneira sistêmica que tenha como características fundamentais a simplicidade em termos de operacionalização e gestão, a facilidade de implementação e disseminação pela Empresa e a priorização em termos da análise e acompanhamento dos indicadores propostos. Desta forma, os autores utilizam a abordagem dos Indicadores da Teoria das Restrições, Indicadores Globais e Operacionais, concomitantemente a definição de Indicadores Locais, voltados diretamente para as questões das rotinas e melhorias nos Sistemas Produtivos.
No decorrer do presente trabalho, os autores procuram justificar a elaboração deste Sistema de Indicadores, com uma ênfase especial nos chamados Indicadores Locais, evidenciando a necessidade concreta de acompanhar e gerenciar as tomadas de decisão no dia-a-dia da produção.
Finalmente, o artigo apresenta um Método de Trabalho, exemplificando com um caso de Indústrias do tipo A, visando o tratamento e construção do Sistema de Indicadores para Empresas Industriais. Uma etapa de fundamental importância consiste em montar o Sistema de Indicadores de forma que os indicadores propostos sejam ordenados de maneira hierarquizada, ou seja, existem critérios de acompanhamento e priorização que devem ser primeiramente definidos, e posteriormente seguidos. Nesta situação, os indicadores são classificados segundo critérios voltados para a Função Processo e para a Função Operação, buscando uma priorização das ações voltadas para a melhoria dos fluxos produtivos e das operações restritivas.
5. Referências
ANTUNES, José A. V. Antunes (1998). Em Direção à uma Teoria Geral do Processo na Administração da Produção: Uma Discussão Sobre a Possibilidade de Unificação da Teoria das Restrições e da Teoria que Sustenta a Construção dos Sistemas de Produção com Estoque Zero, Tese de Doutorado, PPGA/UFRGS, Porto Alegre
COX III, James F., SPENCER, Michael S. (2001). Manual da Teoria das Restrições. Porto Alegre, Editora Bookman.
DETTMER, H. William (1997). Goldratt-s theory of constraints: a system approach to continuous improvement. Milwaukee, Wisconsin: Quality Press.
GOLDRATT, Eliyahu M., COX, Jeff (1997). A Meta. 12.ed. São Paulo: Educator.
OHNO, Taiichi. (1997) – O Sistema Toyota de Produção – Além da produção em larga escala. Editora Bookman. Porto Alegre.
SHINGO, Shigeo. (1996a) – O Sistema Toyota de Produção – Do ponto de vista da engenhara de produção. Editora Bookman. Porto Alegre.
SHINGO, Shigeo. (1996b) – Sistemas de Produção com Estoque Zero: O Sistema Shingo para Melhorias Contínuas. Porto Alegre: Bookman.