7 Perdas no Fluxo de Produção
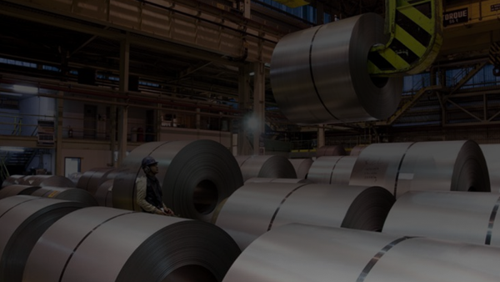
Por: Admin - 30 de Novembro de -0001
Como comentamos em um texto anterior, a quebra de paradigma de como um sistema de produção deve ser analisado e estudado, feita por Shingo e Ohno, construtores do Sistema Toyota de Produção - STP, atualmente também conhecido como Sistema de Produção Enxuta ou Lean Manufacturing System, se constituiu em um marco nas práticas de gestão da Engenharia de Produção.
O paradigma de que um processo de produção era simplesmente constituído por um conjunto de operações foi rompido, sendo necessário fazer sua análise através de dois eixos: o do processo, que corresponde ao fluxo do produto, no qual as matérias-primas e materiais se transformam em produto e o das operações, que corresponde ao fluxo do trabalho, quando operadores e máquinas interferem no fluxo do produto, fazendo a mais valia ao transformar as matérias-primas e materiais em produtos.
A partir desta forma de análise, foi possível identificar as sete perdas existentes no fluxo do produto, e, para cada uma delas, desenvolver ferramentas e metodologias para atuar sobre elas visando sua eliminação ou, quando não possível, sua redução, com o consequente aumento da produtividade e redução dos custos de produção.
A visão tradicional sobre o conceito de perdas, antes do surgimento do Sistema Toyota de Produção – STP, era de que as perdas se resumiam as perdas físicas, tais como refugos, retrabalho e perdas de material, facilmente visíveis. Com o Mecanismo da Função Produção – MFP perdas passam a ser caracterizadas como perdas no trabalho, ou seja, ineficiências na forma de realizar a produção.
Segundo Shingo, “Perdas são todas as atividades que geram custos e não adicionam valor ao produto”. Que visão! Isto muda tudo: somente quando há agregação de valor no produto é que não ocorrem perdas. As demais atividades, na visão do MFP, devem ser consideradas perdas e, portanto, eliminadas/reduzidas.
É importante lembrar que na realização de um trabalho, três tipos de atividades, que geram custos, acontecem: i) trabalho efetivo ou líquido, que compreende as atividades que agregam valor ao produto como, por exemplo, cortar, furar, soldar; ii) trabalho adicional, que compreende as atividades que não agregam valor, mas sem as quais as atividades que agregam valor não se realizam como, por exemplo, posicionar e remover peça em uma máquina para ser processada e iii) perda, que compreende todas as atividades que não agregam valor e não são necessárias para a realização do trabalho efetivo ou líquido como, por exemplo, transportar e inspecionar.
Na sequência, passamos a comentar as sete perdas do fluxo do trabalho identificadas por Ohno e Shingo.
Perda por superprodução. A perda por superprodução pode ser classificada como perda quantitativa ou perda por antecipação. Como o próprio nome indica, quantitativa quando é produzido a mais do que o necessário e por antecipação quando é produzida antes do necessário. É a pior das perdas porque ela esconde outras perdas. Entre as causas básicas desta perda podemos citar, entre outras, quebra de máquina; produção de refugos; deficiência do PCP; tempos de setup elevados e deficiência na previsão de vendas.
Perda por transporte. A perda por transporte corresponde às movimentações, tanto grandes como, por exemplo, transporte por empilhadeira ou paleteira, bem como pequenas, como transferência de peça de um palete para fixação na máquina para ser processada. É importante destacar que melhoria no transporte é diferente de melhoria no trabalho de transporte. Por exemplo, ao se aproximar os paletes de uma máquina está se realizando uma melhoria no trabalho de transporte ao passo que, ao substituir um transportador por transporte manual pode-se, dependendo da situação, realizar uma melhoria no trabalho de transporte.
Perda por processamento. A perda por processamento consiste na realização de atividades que não são necessárias para que o produto adquira suas características básicas de qualidade. Para atuar sobre essa perda, duas perguntas se fazem necessárias: i) Por que esse tipo de produto deve ser produzido? (Análise de Valor) e ii) Uma vez definido o produto, porque os métodos atuais devem ser utilizados nesse tipo de trabalho (Engenharia de Valor).
Perda por fabricar produtos defeituosos. Este tipo de perda é a mais perceptível das perdas, consistindo na produção de produtos que não atendem as especificações de qualidade requeridas pelo cliente.
Perda por estoque. A perda por estoque se refere aos estoques desnecessários tanto no almoxarifado de materiais/peças como no processo, entre as operações, e em produtos.
Perda por espera. A perda por espera está diretamente relacionada com o nivelamento e a sincronização do fluxo do trabalho, correspondendo a ociosidade dos operadores e a baixa utilização das máquinas.
Perdas por movimento. A perda por movimento consiste em detectar e eliminar os movimentos desnecessários feitos pelos operadores, os quais devem executar suas atividades com base em uma folha de operação padrão. Lembrando sempre, como afirma Ohno, que “movimentar-se não significa trabalhar”.