Caso Bibi Calçados: Os impactos do layout na competitividade
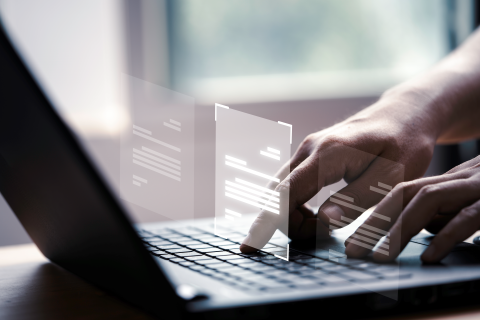
Por: Admin - 30 de Novembro de -0001
Neste vídeo, Rosnaldo Inácio da Silva, Diretor de Operações e Competitividade da Bibi Calçados, apresenta a metodologia utilizada e os benefícios alcançados com o projeto de redesenho de uma das unidades industriais da companhia, localizada na Bahia, proporcionando maior competitividade à empresa.
O redesenho de uma fábrica a partir de uma metodologia robusta de projeto de layout enxuto não é somente a troca física da localização das máquinas, mas é, principalmente, uma oportunidade para revisar o “conceito de fábrica” de forma a priorizar os fluxos produtivos, ou seja, a “função processo”, como diria Shigeo Shingo, um dos principais desenvolvedores do Sistema Toyota de Produção.
A Bibi sofre grande impacto em suas operações devido à sazonalidades de mercado muito fortes, típicas do setor de calçados, por ter grande interferência da moda, não sendo possível estabilizar o processo como ocorre com empresas de outros setores.
No vídeo conseguimos entender como a Bibi, uma empresa de produtos com ciclo de vida curto, alta diversidade de processos e de produtos, conseguiu, em um curto espaço de tempo, se tornar mais competitiva com o redesenho de sua fábrica, a partir de uma metodologia de redesenho de layout, conduzida em parceria com a Produttare.
Este vídeo foi extraído do evento online "Sistema Toyota de Produção raiz e Indústria 4.0 - Caso Layout da Calçados Bibi". Clique aqui para assistir o webinar na íntegra.
A empresa e o cenário antes da mudança
A Bibi Calçados conta com mais de 120 lojas próprias, além de lojas franqueadas e canais de distribuição desenvolvidos no exterior, exportando para mais de 60 países.
Sua matriz fica localizada em Parobé, no Rio Grande do Sul, e conta também com uma unidade verticalizada na produção de calçados em Cruz das Almas, na Bahia.
A metodologia de projeto para redesenho do layout foi aplicada, inicialmente, na planta da Bahia, que possuía quatro pavilhões, sendo duas unidades completas de produção que faziam anteriormente corte, costura e montagem.
Já o terceiro pavilhão tinha apenas uma unidade que fabricava componentes e conjuntos de solados para abastecer as unidades de montagem. Em anexo ao pavilhão, algumas estruturas abrigavam a área de serigrafia de alta frequência.
Assim, a fábrica estava dividida em quatro unidades montadoras, uma de fabricação de componentes, uma de serigrafia e uma de injetados.
A planta já trabalhava com rotas de transporte internas padronizadas para levar material do almoxarifado para o corte e serigrafia. Após, os materiais processados eram levados para outro pavilhão, totalizando 990m de deslocamento interno.
Premissas para alteração de layout
Antes de iniciar o processo de mudança de layout é necessário estabelecer as premissas a serem perseguidas e as metas que a empresa busca alcançar com o projeto.
Nesse sentido, a empresa estudou e definiu os seguintes objetivos para o projeto:
- Elevação da flexibilidade de processos, visto que há alta e crescente diversidade de produtos;
- Elevação da performance de equipamentos através da melhoria do OEE;
- Elevação da performance da planta como um todo;
- Redução do Lead time e custos;
- Evolução no nível de prontidão humana.
A partir destas definições foram traçadas metas para orientar toda a equipe de projeto:
- Redução da área física das linhas de montagem em 50%;
- Aumento da produtividade em 10%;
- Elevação da eficiência global da unidade de 67% para 85%;
- Elevação da capacidade de fábrica em 15%;
- Payback inferior a 12 meses.
O processo de construção da proposta do novo layout
Após os estudos iniciais, a primeira proposta de projeto conceitual consistia em transferir toda a atividade industrial de dois pavilhões para somente um, reduzindo 50% da área.
Entretanto, a equipe identificou duas restrições relevantes, e partiu então para estudos de simulação preliminares, a fim de verificar a pré-viabilidade.
Com as simulações foi observado que a viabilidade dependeria de uma substituição da tecnologia de impressão serigráfica, a fim de os fluxos produtivos e buffers para secagem do material atendessem as necessidades de projeto.
A proposta final de layout viabilizou as quatros linhas de montagens dentro de apenas um pavilhão.
Questões relevantes, envolvendo, inclusive, a substituição de alguns equipamentos e o desenvolvimento de algumas soluções alternativas para substituir parte de processos existentes, foram simuladas e aprovadas.
O processo da alteração física do novo layout
A primeira etapa de alteração foi realizada em junho de 2019, com a localização de 3 linhas de montagem e da impressão serigráfica num único pavilhão.
A transferência da quarta linha foi planejada para a metade de 2020, em função da necessidade de desenvolvimento de alguns equipamentos e de algumas alterações tecnológicas. Com isso, será atendida a meta de eficiência acima de 85%.
Resultados pós alteração de layout - primeira etapa
Espaço físico
A melhoria no layout possibilitou a liberação de aproximadamente 1.400m² de espaço físico, sendo 1.000m² da montagem e 400m² em componentes, ou seja, redução de 35%.
Transporte
A alteração no layout permitiu uma de redução de 800m nos deslocamentos internos de matérias-primas e componentes, passando de 990m para 190m.
Produção
A produção média anterior à mudança era de 4.500 pares de calçados por mês. Nos 11 meses após a melhoria de layout, considerando a unidade que ainda não foi transferida para o pavilhão, passou a produzir 5.570 pares por mês,ou seja, um aumento de 16% na produção.
Havendo um aumento da demanda, o que era esperado antes da pandemia, a Bibi poderia intensificar os processos de produção e dobrar a sua capacidade de produção com o espaço liberado após a melhoria de layout
Eficiência
A eficiência da empresa antes da melhoria de layout era de 66,99%. Considerando a linha de montagem que não sofreu alteração, a eficiência teve um aumento de 13,82%.
Entretanto, se analisarmos somente os índices das linhas transferidas, temos um incremento de quase 30%, passando a eficiência para 87,47%.
Quadro de colaboradores
Visto que não houve aumento na demanda, ocorreu uma redução de 8,41% no quadro de colaboradores. A média mensal, anterior às alterações de layout, era de 648, passando a ser de 613.
Contudo, sabe-se que, se tivesse ocorrido o incremento na demanda conforme previsto antes da pandemia, o quadro de colaboradores permaneceria o mesmo ou seria aumentado.
Conclusão
Ao estudar um projeto de layout, percebe-se que o mesmo tem grande interferência na competitividade de uma unidade de produção.
A alteração dos aspectos físicos da fábrica proporciona a redução das perdas do sistema de produção, assim como instiga a liderança a buscar novas tecnologias, novas soluções para problemas conhecidos e que ficam evidenciados nas análises preliminares.
A mudança de layout apoiada por uma ferramenta de simulação, permite mensurar os ganhos potenciais a serem alcançados, não somente com as alterações físicas, mas também com a mudança de tecnologia e a adoção de outras soluções.
Assim, a análise de custo/benefício e o cálculo do melhor payback para diferentes opções, podem ser evidenciados de forma clara, apoiando a tomada de decisões sobre a melhor trajetória de mudança.